Integrity Assurance to Determine Additive Manufacturing Safety for Critical Components

By Engaged Expert
Rob KulkaRob is a chartered mechanical engineer with over 15 years’ experience in structural integrity assessment and asset management, through the use of complex computational analysis, damage tolerance assessment, mechanical testing, and safety case development.
The Challenge
Additive manufacturing, often called “3D printing”, uses techniques such as laser fusion of metal powders to create optimal design solutions that could not be made in any other way. Such components are lighter and stronger than conventional parts, but because of the way they are made the standard methods for assuring their quality cannot be used. This is a particular problem for safety-critical components in industries like nuclear and aerospace.
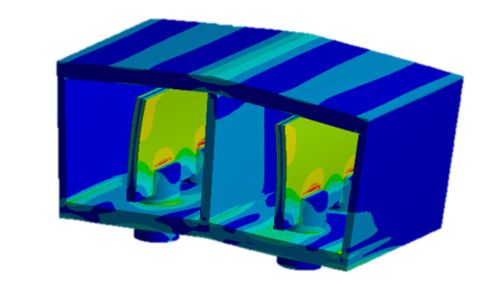
The Solution
Working with UKAEA, inspection bodies, and aerospace companies, a risk-based analysis methodology was developed that assessed the fatigue lives for an otherwise perfect component based on a number of worst-case potential flaws then statistically assessed the probability of inclusions, voids, or unfused particles with the critical region. The method was complex but could be automated easily for any given geometry, quickly leading to a risk assessment for that component that would inform the test regime during manufacture.
The Result
In a rapidly expanding field this methodology remains to be further developed to account for the growing range of material types and manufacturing techniques. However, the initial test applications have been very successful.
Find related Resources
Related Resources
Related Services
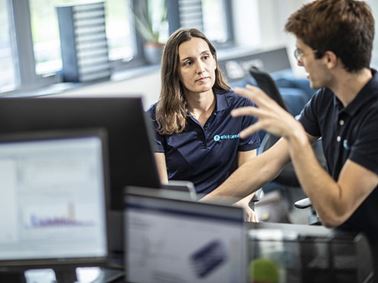
Digital Engineering Case Studies
Read examples of how Element Digital Engineering utilize modeling, simulation, and other digital tools to help our customers innovate and solve complex challenges.
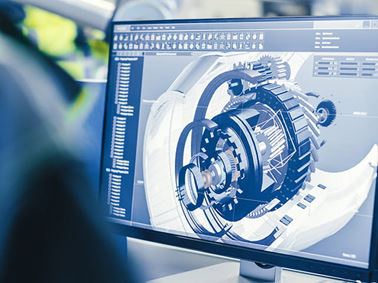
Modeling and Simulation
We specialize in modeling and simulation to accelerate your research and development initiatives, optimize your designs and support safe, efficient operations.
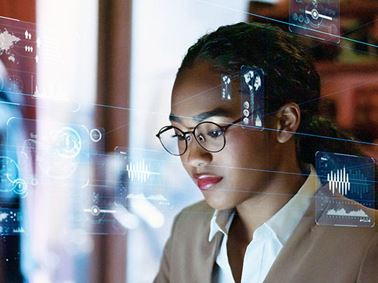
Data Science and Machine Learning Services
We combine state-of-the-art data science and machine learning to provide insights that help you improve performance and increase productivity.
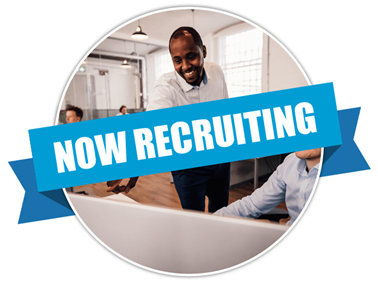
Join The Digital Engineering Team
Element Digital Engineering is growing fast. We work at the forefront of Element's digital transition, delivering insight, guidance and answers to complex engineering and technology challenges. Start your Element journey today!