CE Marking For Electrical Equipment - Expert Tips For Compliance and Safety

By Engaged Expert
Stephen TaitStephen Tait has over 19 years' experience in testing and certification of telecoms products
Navigating the complexities of CE marking for electrical equipment is crucial for manufacturers aiming to enter the European market. This article explores the importance of conducting thorough risk analyses, adhering to harmonized standards, and utilizing third-party testing to ensure compliance. Drawing on over 19 years of experience in testing and certification of telecom products, expert Stephen Tait offers invaluable insights and practical advice for achieving CE marking compliance for your electrical equipment.
What is CE marking for electrical equipment?
CE Marking for electrical equipment is essentially a self-declaration by the manufacturer that the product meets safety, health, and environmental requirements and therefore allows free movement within the European marketplace. However, self-declaration still requires a level of technical support to allow this claim to be made by a manufacturer. As part of the 2016 NLF updates, risk analysis in relation to the essential requirements of the legislation has been made an important part of the CE Marking process.
Business risks associated with CE marking electrical equipment
Manufacturers must consider and record in their risk analysis, all possible risks posed by their product to determine:
- Which essential requirements apply to their products.
- How they are addressing the identified risks to ensure compliance with the applicable essential requirements (e.g. through the application of harmonized standards, and third-party accredited testing).
There are two specific business risks associated with CE Marking:
- Are you willing to take the risk of self-declaring against the CE legislation without satisfactory evidence that your product meets all the essential requirements of the legislation (e.g. Low Voltage or Machinery Safety Directives)?
- Ensuring your product is safe, not just functionally acceptable, but also ensuring the devices are used in a way that will not cause harm to the user, domestic animals, and property during installation, use, or maintenance (the ‘What if?’ scenario).
The combination of both risks and not acting on them correctly could be very costly both financially and potentially loss of reputation and creditability in the marketplace. Everyday product recalls are listed on the RAPEX website on the basis that devices do not meet the essential health and safety requirements of the CE marking legislation and are therefore potentially not safe for use; one of the most common risks being identified with these devices are defects that could cause Electric Shock or Fire.
The best way to mitigate potential product recalls and ensure you meet the correct requirements is to progress with third-party testing.
Why is electrical safety testing required?
Electrical safety testing using a harmonized standard is a key step to ensure products meet the essential requirements of the Low Voltage Directive (LVD) or Machinery Safety Directives and thus ensure a manufacturer can demonstrate presumption of conformity to the applicable legislation. Using a third-party test laboratory is the most efficient and reliable way to ensure devices are fully compliant with harmonized standards and suitable for their end application. Third-party testing from an accredited test laboratory guarantees the product has been tested in accordance with the correct requirements of the standard and gives the manufacturer confidence when signing the final part of the process, the Declaration of Conformity. It is essential that products have undergone the correct level of test and review to ensure that:
- The product is not liable for overheating and causing fire
- The product has suitable electrical isolation and cannot cause an electric shock hazard
- Potential non-primary use case risks have been considered or identified
- The product is correctly marked and the instructions for use are clear and allow the user to install and operate the equipment safely
Appropriate third-party safety testing will increase credibility when looking to sell products to a global market. Most countries will not accept test reports unless they have been issued by an appropriately accredited test laboratory. This is also true for retailers and consumers who require assurance that a product is safe and will not cause issues when placed on the market or put into service.
How Element can help?
Ensuring compliance with CE marking electrical equipment standards is not just a regulatory obligation but a critical step in guaranteeing product safety and marketability. Thorough risk analysis, adherence to harmonized standards, and third-party testing are essential components in this process.
Engaging with an experienced and accredited testing partner like Element provides the assurance needed to confidently navigate the complexities of CE marking and succeed in the global marketplace. Through Element’s certification services, you can access major international electrical safety certification schemes, including the IECEE CB Scheme (operating in over 50 countries), CE marking (Europe), and NRTL certification (North America).
Find related Resources
Understanding Electrical Product Safety Standards
Learn how to avoid common pitfalls on an electrical product’s compliance journey and adhere to electrical product safety standards. LEARN MOREElectrical Product Safety: Changes in IEC 62368-1 Edition 4
With the publication of Edition 4 of IEC 62368-1, manufacturers of audio/video, information and communication technology equipment are affected by numerous normative changes.
More from Element
[No text in field]
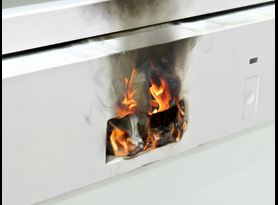
Electrical Safety Testing
Element helps companies achieve compliance against global safety standards for 167 countries.
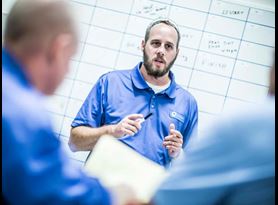
CE Marking and Testing
CE marking is a mandatory conformity mark enabling you to enjoy free movement between all 28 Member states.
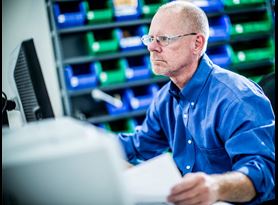
Product Compliance
Element provides one of the widest range of test and support services in the world aimed at getting your product to market and complying with the V&V requirements.
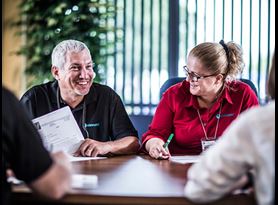
Advisory Services
Our team of safety experts can guide you through the most effective way of getting your product onto the prospective market quickly.
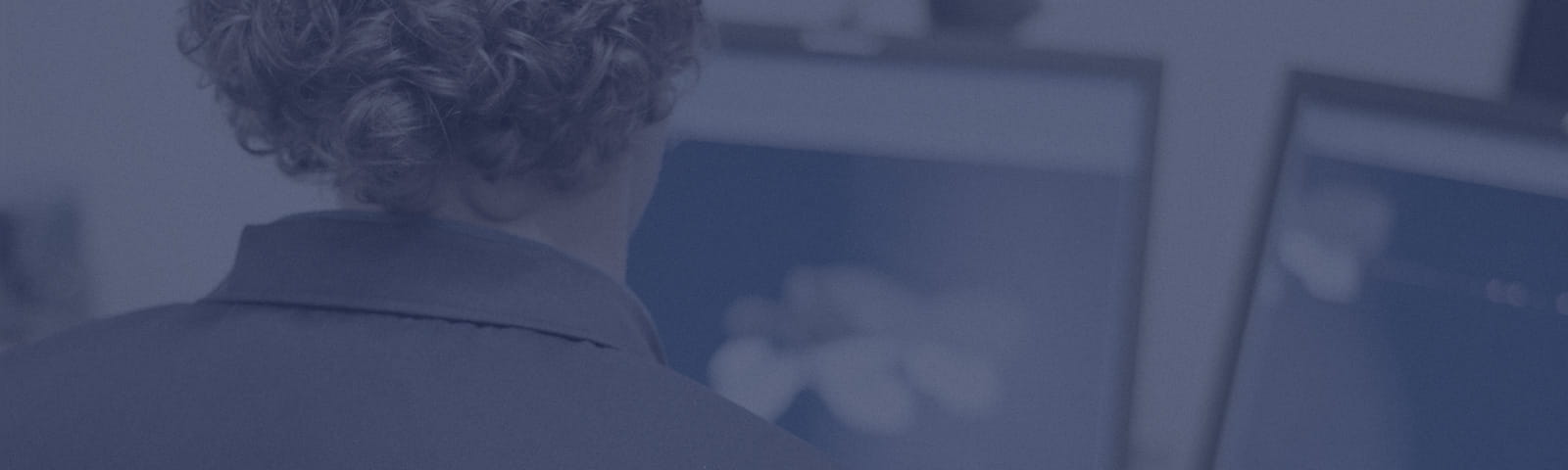