Pressure test programs are critical for verifying pressure ratings and evaluating the integrity of vessels, components, and systems. Element offers hydraulic and pneumatics static and dynamic pressure testing. The fluids can be conditioned to extreme high and low temperatures.
What is Pressure Testing at Element?
Pressure testing evaluates the integrity of vessels, components, and systems under controlled pressure conditions. At Element, we provide both static and dynamic testing using hydraulic and pneumatic methods, with the ability to condition fluids to extreme temperatures. Our comprehensive testing validates pressure ratings and ensures product reliability across your entire system.
What Can Element Offer You For Pressure Testing?
Components and Materials We Test
We test a comprehensive range of pressure-bearing components, from individual parts to complete systems. Our expertise covers pressure vessels, pipes, tubing, fuel assemblies, boiler components, fuel tanks, and ventilation systems. We can evaluate virtually any product requiring pressure certification.
Key Tests Offered
- Hydrostatic pressure testing for material integrity
- Pneumatic pressure testing for leak detection
- Cyclic pressure testing for fatigue evaluation
- Ultimate pressure testing for maximum tolerance
- Burst pressure testing for failure point analysis
- Proof pressure testing for operational validation
- Mechanical and structural pressure testing to evaluate environmental forces on structures and materials
- Depth and submerge testing for underwater applications
Methods and Solutions Offered
Our testing methods adapt to your specific needs. We offer pressure conditioning at extreme temperatures, rapid pressure cycling up to 200,000 PSI per second, and comprehensive system evaluation. All testing aligns with industry standards while accommodating custom requirements.
Which Labs Offer This Service
Our 9,000-strong team operates from product qualification testing hubs across the world, providing global access to our expert capabilities. Find out where your nearest product qualification testing hub is on our Locations Page.
Specialized Industry Solutions
We offer dedicated testing solutions for specific sectors, including specialized mechanical and structural pressure testing for building products. Our experts evaluate environmental forces through comprehensive load testing programs tailored to construction industry requirements.
Your Challenges, Our Solutions
your testing partner
Preventing Catastrophic Failures
Our ultimate pressure testing determines maximum safe pressure levels, while expert analysis helps establish optimal operating parameters to prevent equipment failure in the field.
Ensuring Long-term Reliability
Through advanced cyclic pressure testing, we simulate lifetime usage patterns and validate your product's ability to withstand repeated pressure stress without fatigue failure.
Meeting Industry Standards
Comprehensive testing to ASME, ASTM, and military standards, plus customer-specific requirements, ensures your products achieve the necessary certifications and compliance.
System Integrity Verification
Our hydrostatic and pneumatic pressure testing methods thoroughly evaluate both components and complete systems, identifying potential issues before they become problems.
Element Experts at your Service
Browse our experts by discipline and specialty, and explore their skills and experience.
Why Choose Element
Complete Testing Solutions
Comprehensive range of pressure testing services covering all industry needs.
Advanced Technical Capabilities
Industry-leading pressure ramp rates up to 200,000 PSI per second.
Custom Testing Programs
Expert-designed testing programs tailored to your specific requirements.
Global Testing Network
Access to testing facilities and experts worldwide.

Explore our global network of Labs and find your nearest location
View all locationsRelated Services
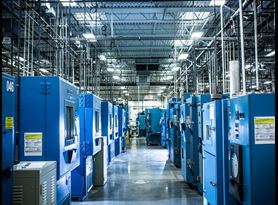
Product Qualification Testing Services
Find out how Element provides critical compliance, reliability and qualification testing to clients in Aerospace, Transportation, Energy and more.
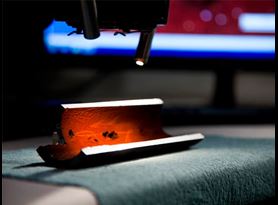
Failure Analysis
Find out how Element's global team of failure analysis experts learn from the past, to help prevent future failures in service.
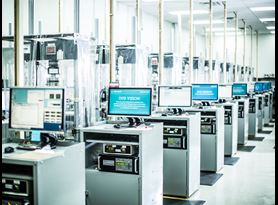
Materials Testing
Our materials testing labs are staffed by Engaged Experts working tirelessly to solve our clients' most complex technical and commercial challenges.
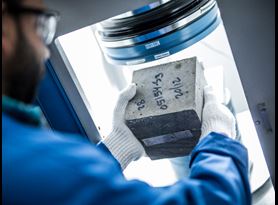
Construction Materials Testing
Element offers a full spectrum of construction materials testing to ensure the materials are safe in their application, compliant, and ultimately fit for purpose.