Has your product or component failed and you need to understand why? Learn from the past and prevent future failures with Element’s expert Failure Analysis services. Uncover root causes, reduce risks, and enhance the overall quality and performance of your products, materials, or components to prevent future damage.
What is Failure Analysis and why is it Important?
Failure analysis is a multi-faceted, holistic approach to understanding why materials or products fail. It is a critical aspect of product development and system improvement which not only helps you learn from the past but helps prevent future failures.
While the root cause analysis and associated impacts of any failure are the primary goals, the results can also help you make changes in your processes or material selection to prevent future occurrences. Read our article to find out three reasons to perform failure analysis.
Element teams provide expert failure analysis and reporting through a range of technical services, including stress analysis and material characterization, trace evidence analysis, forensic engineering, and more.
Key benefits of Failure Analysis Services with us
- Gain insight into failures with our precision root cause identification: Our initial investigation involves an in-depth discovery phase, considering environmental factors contributing to failure, type of application, how long it’s been in service, and design characteristics. Element's analysts apply diverse methods and tools for detailed inspection leading to root case determination.
- Conquer complex non-metallic material challenges: Non-metallic material failure analysis presents a unique challenge. While the initial analysis process is the same, our labs use specialist fractographic interpretation and analytical testing, tailored to these types of materials. As there are so many different formulations and combinations of non-metallic materials, we often use intensive material identification programs to help pinpoint the origin and degradation of non-metals.
- Ensure safety and compliance: We know that reliability and safety are paramount in your industry. Our failure analysis experts combine extensive global and national standards knowledge with years of experience, so you can feel confident in the accuracy and compliance of their solutions, no matter the industry you’re in.
- Mitigate risks and navigate litigation challenges with our expert witness services: Our wide-ranging expert witness services deliver critical testimony or expertise in legal and insurance cases involving material, product, or component failures. Whether it’s compliance cases, patent infringements, or detecting evidence of abuse or defects, we provide comprehensive support.
- Digital solutions for advanced Finite Element Analysis (FEA): Our FEA experts use computer-aided design (CAD), in-service data, and material data for in-depth analysis, efficiently examining multiple failure scenarios without full-scale testing expenses. We collaborate with physical testing experts to suggest solutions and validate simulations with physical testing.
- Specialists in the Oil & Gas Industry: For the Oil & Gas sector, our experts specialize in analyzing pipelines, drilling equipment, pumps, valves, and seals. We acknowledge the criticality of key asset failures, providing detailed insights, recommendations, and potential litigation support.
Your Failure Analysis Experts
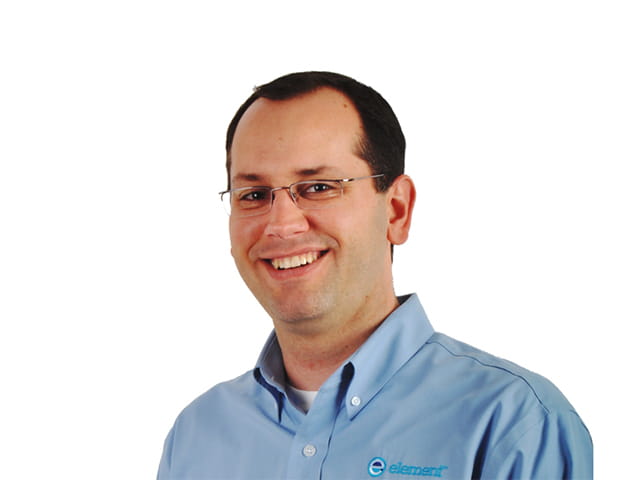
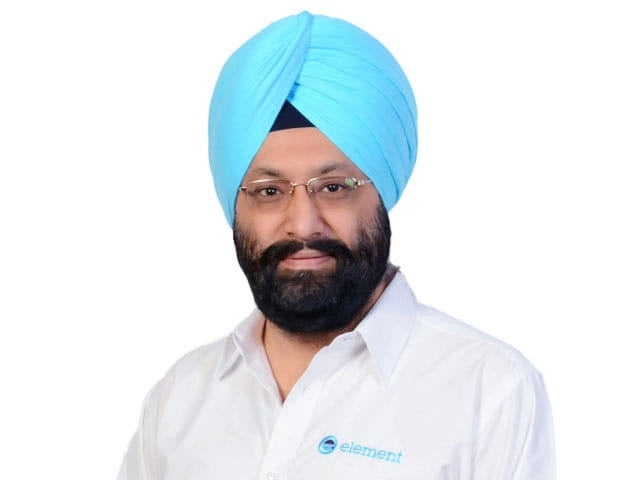
“Every time we've needed a failure analysis with a quick turnaround, Element has been there to fill that role with impeccable quality and turnaround time. ”
Ryan Camiré
Leach International Corporation
Rapid, Reliable, and Comprehensive Solutions for Future Failure Prevention
Based on findings from the failure analysis process, Element’s experts provide recommendations and work closely with you to find solutions for a wide range of products and materials. Our combination of materials expertise and understanding of environmental impacts means we can swiftly deliver comprehensive results, ensuring resolutions and preventing future in-service failures. You can rely on the certainty, speed, and flexibility we provide.
Multidisciplinary Failure Analysis Approach Across the Whole Product Life Cycle
Our approach to root cause analysis of failures stretches across your whole product life cycle, from the design and selection of materials through the manufacturing process and how the product is used in service. Since issues during any one (or combination) of these stages can cause failures, we know it’s important to investigate them all thoroughly.
Such a broad variety of circumstances requires an equally wide range of analysis methods; that’s why we offer services ranging from fractography, composition determination, mechanical property testing, microstructural analysis, and material comparison to specifications and expectations. With insights into design influences, processing, component use, and future behavior, rest assured that we can help identify and troubleshoot your product’s failure, whenever it occurred.
Expert Failure Analysis Services that you can Trust
Corrosion Analysis:
Fracture Analysis/ Fractography:
Chemical analysis:
Residue analysis:
On-site failure analysis:
Failure analysis of metals/metallurgical failure analysis
Additional services:
- Failure analysis investigations
- Metallurgical consulting and expert witnessing
- Failure analysis of non-metals
- Crack analysis
- Scanning electron microscopy (SEM)
- Energy dispersive spectroscopy (EDS)
- Optical microscopy
- Optical stereo microscopy
- Hardness testing
- Metallographic preparation
- Microhardness testing
- Inclusion analysis
- Tensile testing
- Joint plaintiff-defense investigations for lawsuits
- Weld failure analysis
- Printed Circuit Board (PCB) failure analysis
- Fatigue failure
Why Choose Element?
Element’s labs in the US, UK, Europe, Middle East, and Asia have decades of hands-on experience in performing failure analysis. Our global network of experts is recognized as some of the most trusted in their field for providing reliable failure analysis to diverse clients across many industries, including Aerospace, Energy, Transportation, Construction, Medical Device, and Consumer Products.
Our testing meets a wide array of standards set by local, national, and global regulatory bodies so you can be confident that recommendations from Element will be compliant. We collaborate with organizations like the American Society for Testing and Materials (ASTM), the International Organization for Standardization (ISO), the Food and Drug Administration (FDA), and many others, ensuring the rigorous regulation of your materials and products.
To learn more about Element’s credentials, please visit our About Us page. To discuss how we can support your failure analysis needs, contact an expert today.
The Importance of Failure Analysis Testing
A guide to understanding how engineering failure analysis is used to prevent failures and improve your product’s design, materials, fabrication techniques, and inspection methods.
LEARN MOREMechanical Failure Analysis Storytelling
When we receive an initial RFQ for failure analysis, we have basic questions that will help us determine how complex the story is. To learn more about mechanical failure analysis, or if you have any questions, contact our team today. LEARN MOREThree Reasons to Perform Failure Analysis
Failure analysis is a process by which a failed product is inspected to determine what caused it to fail. Methods vary in approach, but all seek to determine the root cause of the failure by looking at the characteristics and clues left behind.
LEARN MOREFurther Reading
Our Services
Our teams provide expert failure analysis and reporting through a range of technical services, including stress analysis and material characterization, trace evidence analysis and forensic engineering.
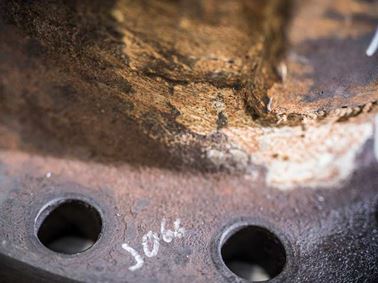
Root Cause Analysis for the Oil & Gas Industry
Element’s failure analysis experts help you understand the causes of asset failure, advise on remedial action, and support you in any potential litigation you may face.
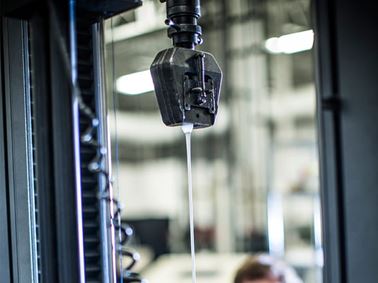
Polymer Failure Analysis
Element experts are here to help you with your failure analysis on plastics, composites, rubbers, adhesives, sealants, paints and coatings.
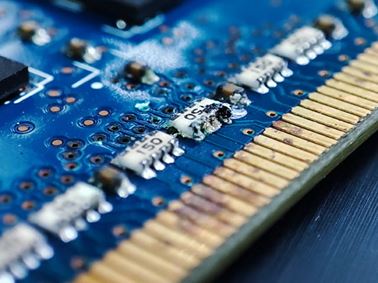
Failure Analysis for Electronic Devices & Components
Understand the root cause of electronic device failure and build better, more reliable components with electronic device failure analysis from Element.
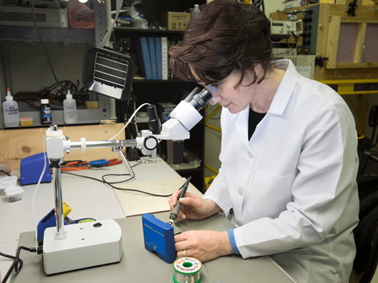
Battery Failure Analysis
Identify the root cause of battery failures and build better, safer products with data from Element’s comprehensive battery failure analysis.
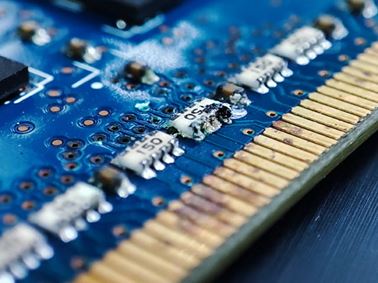
Printed Circuit Board (PCB) Failure Analysis
Understand and rectify the root causes of PCB failure with industry-leading PCB failure analysis from the testing experts at Element.
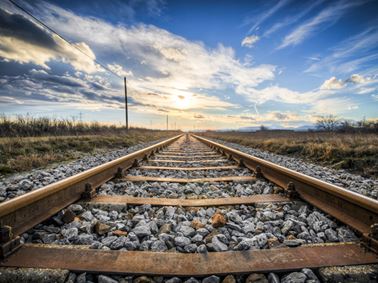
Railroad Failure Analysis
Element's dedicated rail testing experts work with you through every step of the process, helping you understand defects and failures before further damage occurs.
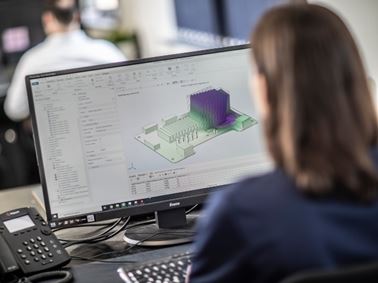
Finite Element Analysis Services (FEA)
Element offers advanced numerical analysis service using Finite Element Analysis (FEA) techniques using industry standard software to predict the long term behavior of materials components and products when in service.
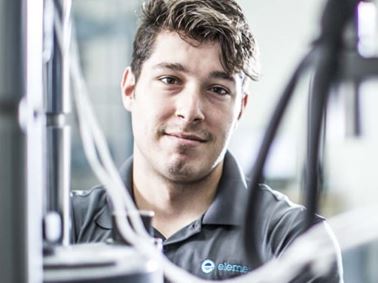
Expert Witness Services
Element offers expert witness services to legal and insurance firms to provide testimony with precision and expertise.
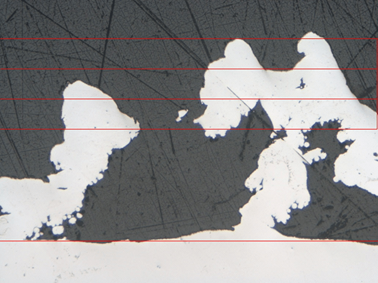
Fractography Services
Our fractography services can help determine the cause of failure, fatigue, or defects in metallic materials.