Understand and rectify the root causes of PCB failure with industry-leading PCB failure analysis from the testing experts at Element.
Most modern electronic devices – from singing birthday cards to supercomputers – rely on printed circuit board (PCB) technology, but electronics manufacturers continue to demand circuit boards that are both more sophisticated than ever and cheaper to produce. With the increased complexity of PCBs, the need for comprehensive failure analysis of new PCB designs is paramount for ensuring product safety. At Element, our experts specialize in PCB failure analysis, providing invaluable insights to design engineers and helping them identify the root causes of failures.
Techniques for PCB failure analysis
Our experts employ a range of cutting-edge techniques and industry-standard tests to isolate the key factors contributing to PCB failures:
- Micro-sectioning analysis allows us to examine the internal structure of a PCB, providing crucial insights into potential defects and weaknesses.
- Solderability testing ensures that the solder joints are robust and reliable
- PCB contamination testing helps identify any contaminants that may compromise the performance of the board.
- Optical microscopy and scanning electron microscopy (SEM), helps us perform detailed examinations of PCB surfaces and components, allowing us to uncover hidden flaws.
- X-ray inspection enables us to inspect the internal features of a PCB non-destructively, facilitating accurate failure analysis
Unique challenges
Understanding the challenges faced by PCB fabricators is instrumental in conducting effective failure analysis. Some common issues we encounter include the integration of components in high-speed printed circuit boards (HSCBs), which introduces complexities arising from the use of multiple materials and the potential for incorrect component placement. The lead-free assembly process, necessitating higher temperatures, poses risks to solder joints and electronic components. Barrel fatigue, caused by differential expansion between copper plating and the board's coefficient of thermal expansion, emerges as a prevalent failure mode. Selecting the appropriate surface finish is crucial, as it directly impacts process yield, rework, field failure rate, testing, scrap rate, and cost. Moreover, conductive anodic filament (CAF) is a phenomenon involving electro-chemical processes leading to current leakage, intermittent electrical shorts, and dielectric breakdown between conductors in PCBs.
Why choose Element?
At Element, our team of experts is well-versed in addressing the unique challenges faced by manufacturers. By working closely with clients, we provide tailored solutions that enhance product quality and reduce failures. Our in-depth understanding of failure analysis and extensive knowledge of PCB technology allows us to deliver comprehensive reports and recommendations, empowering design engineers to revise their designs effectively and prevent future incidents.
When it comes to PCB failure analysis, trust Element's expertise to deliver accurate insights and actionable solutions. With our commitment to excellence and passion for ensuring product safety, we are your trusted partner in navigating the complexities of the PCB industry. Contact us to learn how we can support you in delivering the highest-quality products.
Learn more
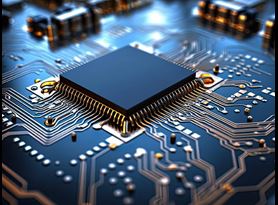
Printed Circuit Board Testing
Ensure your printed circuit boards and finished printed circuit assemblies are of the highest quality and compliant with relevant standards with comprehensive PCB testing from Element.
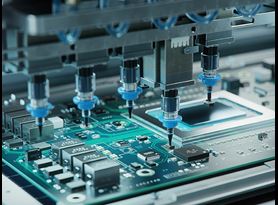
Electronic Component & PCB Assembly Testing
Element’s testing experts provide the insight you need for complex electrical component and printed circuit board (PCB) assembly testing.
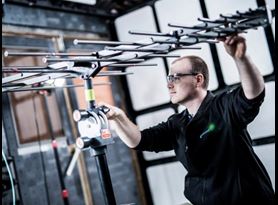
Consumer Electronics Testing & Certification
Element’s consumer electronics testing and certification services help your products meet EMC, Electrical Safety, and Radio national & global requirements.
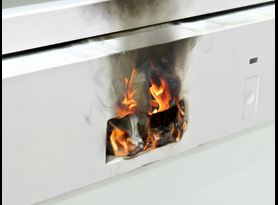
Electrical Safety Testing and Certification
Discover how Element combines its range of electrical testing with EMC, radio, wireless and IoT compatibility services to get your products to market faster.