Element’s Non-Destructive Testing (NDT) and Inspection services help you ensure your products' integrity and reliability while in-service and save you time and money when evaluating your products, troubleshooting, or carrying out research.
What is non-destructive testing (NDT)?
NDT covers a broad group of techniques used to evaluate the properties of a material, component, assembly, part, product, weld, or system, without materially affecting the integrity of the unit being inspected or investigated under the test procedure.
Non-destructive testing services
The NDT service methods we offer are designed to comply with a variety of industry standards, unique customer requirements, government contracts, and military specifications. We serve many sectors and can test metallic and composite materials from raw materials such as sheet, plate, bar, and pipe to stand-alone components.
We use ASNT Central Certification Program (ACCP), SNT-TC-1A certified technicians, and Certified Weld Inspectors (CWIs) to deliver a full range of NDT services. Our experts assist clients in projects ranging from material analysis or product qualification testing to quality assurance and audit programs.
Non-destructive testing methods
We provide a full suite of NDT methods, including, but not limited to:
- Radiographic testing
- Digital radiography
- Computed tomography
- Eddy current testing (ET)
- Liquid penetrant testing (LPI - fluorescent & color)
- Magnetic particle inspection (MPI)
- Dimensional inspection
- Visual inspection
- Ultrasonic testing and inspection services
- Weld inspection services
- Surface roughness testing with optical profilometry
- Acoustic Emission (AE) testing
- Leak testing
- Infrared Thermography
- Video Borescope Inspection
- Linear Accelerator (LINAC) Testing
The Element advantage
At Element, we have unrivaled expertise in testing; our personnel are highly trained and experienced, holding certification from Levels 1 - 3 across recognized schemes, including SNT-TC-1-A (ASNT), ISO 9712 PCN, BS EN 4179, and NAS 410.
Contact our experts to learn more about our non-destructive testing (NDT) testing and inspection services or request a quote today.
“Excellent service !”
Martin Beer
SWP Hydraulics Ltd
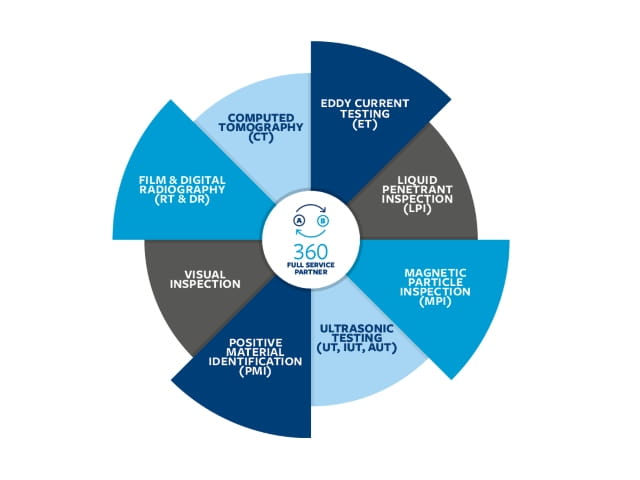
Non-Destructive Testing (NDT)
From nuclear reactors to bridges and aircraft fuselage, our NDT services guarantee regulatory standards are met before components are put into service. Element uses NDT to determine cracks, porosities, welding defects, and material properties on-site, in-field, and in our laboratories.
As a leader in NDT services, Element harnesses the world’s most advanced testing capabilities and expertise to help our customers transform the world we live in.
Replication Metallography: A Non-Destructive Solution
Element discusses replication metallography as a non-destruction solution to metallurgical evaluation.
Read MOREThe Benefits of Immersion Ultrasonic Inspection of Composites
Read the article to explore the benefits of two methods of ultrasonic inspection of composites: contact and immersion ultrasonic testing (IUT).
Read MOREMagnetic Particle Testing of Flanges
Magnetic particle inspection is a method of detecting flaws in ferrous materials using magnetic fields. This testing is best suited to magnetic materials, such as iron, nickel, cobalt, and their alloys.
Read MOREWhite Paper: Ultrasonic Phased Array Testing
Ultrasonic testing (UT) is a non-destructive test method that utilizes sound waves to detect cracks and defects in parts and materials. This white paper provides an overview of the inspection method and the benefits toward material approval.
Read MOREOur Services
Element has one of the most comprehensive ranges of non destructive testing services.
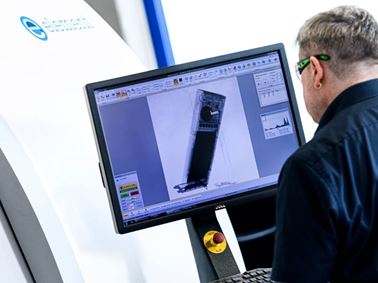
Industrial Computed Tomography
Element offers high-resolution industrial computed tomography to provide a detailed examination of components that can be used for production defect detection, dimensional inspection, and reverse engineering.
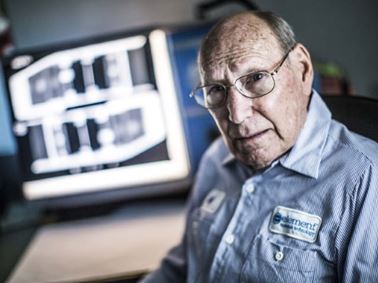
Radiographic Inspection (RT)
Element has the capabilities to perform conventional film radiography to Computed and Digital radiography, a highly sensitive method that produces an image in a digital format that is viewable on any laptop or computer.
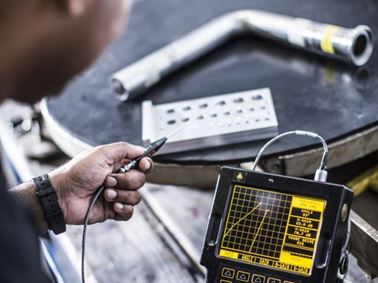
Eddy Current Testing (ET)
Eddy current techniques are commonly used for the non destructive examination and condition monitoring of a large variety of metallic structures, including heat exchanger tubes, aircraft fuselage, and aircraft structural components.
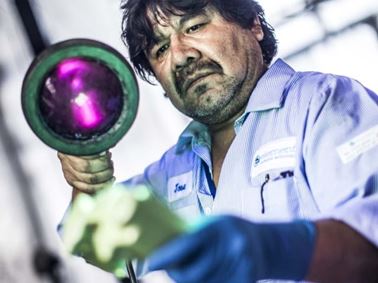
Liquid Penetrant Inspection (LPI)
LPI has the advantage of being able to detect flaws in nonmetallic and non ferromagnetic materials and is also one of the most portable of the surface inspection methods, allowing us to conduct a comprehensive onsite penetrant inspection.
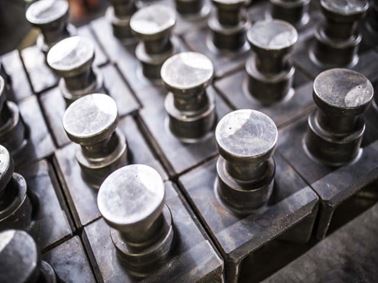
Magnetic Particle Inspection (MPI)
Magnetic particle inspection is one of the fastest and most cost effective non destructive examinations available for ferromagnetic materials such as castings, weldments, forgings, machined or stamped parts. Element performs on-site evaluations using portable equipment and in-lab inspections on large components weighing up to 12,000 pounds.
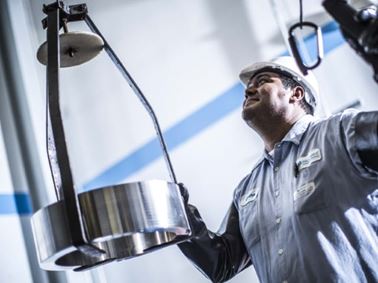
Ultrasonic Testing (UT)
Our inspectors use ultrasonic waveforms to pass through a material to detect flaws and provide a complete volumetric inspection. Contact testing, Phased Array and the Immersion technique are available for complex geometric parts that otherwise may not be subject to complete volumetric inspection.
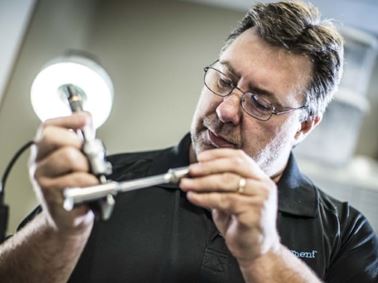
Visual Inspection
Element provides a number of visual testing services that in most cases can be the first method of inspection to detect defects and observe problems in the earliest stages of fabrication.
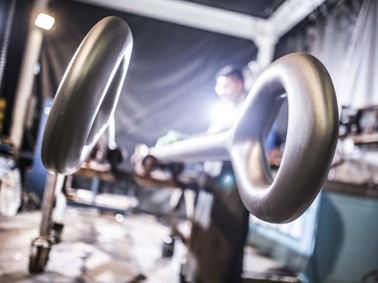
Non Destructive Hardness Testing
Element supports a variety of portable and non destructive hardness testing methods. Methods such as UCI (Ultrasonic Contact Impedance), TIV (Through Indenter Viewing), and improvements in the rebound method (Leeb) provide a critical solution for verification of hardness on large components with complex geometries.
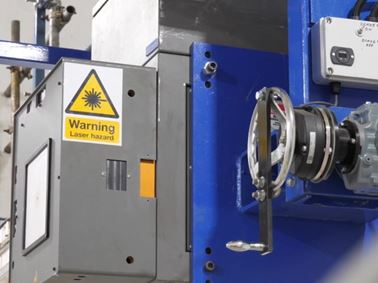
Linear Accelerator Testing
Element's 6Mev Linear Accelerator emits high-energy radiation to detect defects in weld quality, castings, and structures to enable quick and efficient radiographic testing of think steel castings.
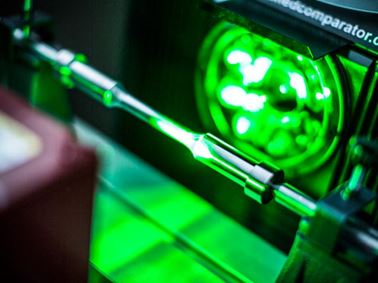
Dimensional Inspection
For projects that require accurate dimensional measurements, Element offers a broad range of 2D and 3D metrology services.
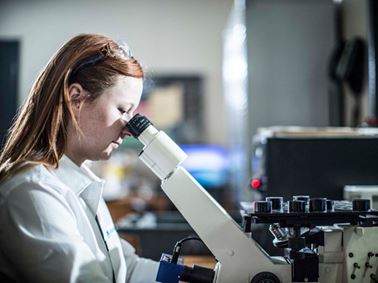
Weld Inspection Services
Element's weld inspection services ensure your welds meet required quality standards, leading to reduced failure rates and extending the potential operating life of components.
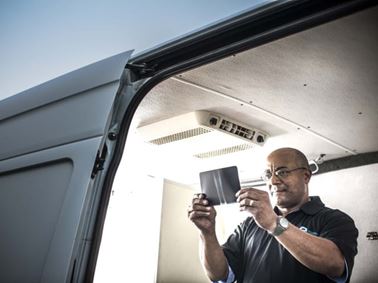
NDT Field Services
When employed at critical stages of the manufacturing or fabrication process, our NDE technicians work in the field to optimize production and ensure the quality of your finished product.