Protect your assets, avoid failure and loss production, qualify welds, assess your materials, and improve safety with Element’s wide range of ISO/IEC 17025-accredited corrosion testing services.
What is Corrosion and why does Corrosion Testing Matter?
Corrosion is a natural process that occurs in every material under certain environmental conditions, causing degradation of the material and, in turn, failure of critical equipment, products, and assets. These losses are expensive to remedy and could result in production downtime, environmental impact, and reputational damage. Corrosion testing is mission-critical to the design, development, and durability of metallic materials, components, and products.
Benefits of Corrosion Testing with Element
- Regulatory Compliance Assurance: Meet industry standards effortlessly with Element's corrosion testing services. We adhere to international protocols—ASTM, NACE, and API—ensuring safety, compliance, and top-notch quality for your materials and products.
- Rigorous Testing for Your Products and Materials: Put your materials and products to the ultimate test with Element. From standardized corrosion testing methods such as salt spray and intergranular corrosion evaluations to highly specialized testing such as cyclic corrosion testing and sour service corrosion, we create real-life conditions to ensure optimal performance.
- A Partner for Global Testing: Wherever you operate globally, Element is your corrosion testing partner. Our global network of corrosion testing labs across North America, the UK, Europe, the Middle East, and Asia offers consistent and reliable testing, making sure your operations comply with international standards.
- Material Selection Made Simple: Choosing the right materials for corrosive environments can be challenging. Our experts guide you in selecting materials tailored to your environment, providing confidence in their performance and durability.
- Customized Testing to Match Your Unique Needs: Your environment is unique, and your testing should be too. Element offers specialized corrosion testing methods to accurately mimic your unique environmental conditions, ensuring solutions that meet your specific needs.
- Innovative Cutting-Edge Solutions: Stay ahead with Element's innovative corrosion solutions. Our engaged experts continually develop new testing methods, providing cutting-edge techniques for assessing corrosion in diverse applications.
- Combat Reservoir Souring: Our corrosion labs are fully accredited to test both metallic and non-metallic materials, specializing in the qualification of “sour” service applications such as Hydrogen Induced Cracking (HIC) or Sulfide Stress Cracking (SSC).
- Reduce Environmental Impact: Element helps you protect the environment. Beyond equipment, our services ensure your operations remain eco-friendly by mitigating the effects of corrosion.
Your Corrosion Testing Expert
Ensure your Materials’ Reliability with Data-Driven Corrosion Insights
We understand your concerns about the long-term reliability of your materials in corrosive environments. Our corrosion testing services provide you with real-life data for informed design, material, and chemical selection decisions. With our in-depth analysis, you can be sure your materials will stand the test of time, giving you peace of mind.
Reduce Costly Failures and Minimize Production Downtime
Corrosion-related material failures can be expensive and can lead to production downtime, affecting productivity and profitability. At Element, we can help you identify and address potential issues before they become costly problems, whilst carrying out timely and accurate testing to keep your operations running smoothly.
When critical failures occur, Element’s world-renowned corrosion testing experts provide you with real-world solutions to improve your processes and programs and reduce the risk of future occurrences.
Corrosion Testing Services that you can Trust
Element provides a wide range of corrosion testing services for various industries, including Oil & Gas, Aerospace, Medical Devices, and Transportation. We offer both lab-based and on-site testing services to help with evaluations, material selection, assessments, and proactive mitigation measures. Our services cover everything from developing advanced corrosion-resistant materials to monitoring production parts.
Our services include but are not limited to:
- Accelerated Corrosion Testing (ACT)
- Advice and guidance
- Assessing materials for resistance to crack propagation
- ASTM G48 pitting and crevice corrosion testing
- Corrosion failure analysis
- Corrosion fatigue
- Corrosion testing and evaluations
- Dezincification resistance test in accordance with ISO 6509
- Electrochemical corrosion testing
- Galvanic corrosion testing
- GMW 3172 cyclic corrosion testing
- Intergranular corrosion testing
- Material selection
- MFG testing mixed flowing gas
- Salt spray testing
- SCC stress corrosion cracking test
- Simulated service environments: sour, sweet, brines, seawater
- SSRT slow strain rate testing
- Weld corrosion testing
Why Choose Element?
Element provides a broad range of ISO/IEC 17025:2017, NADCAP, UKAS, and A2LA corrosion testing services. With a global reach of corrosion testing laboratories in the US, UK, Europe, the Middle East, and Asia we have the right combination of technical expertise, capabilities, and accreditations to support your testing corrosion needs.
As one of the world’s most trusted corrosion testing companies, we are the obvious choice to assist you with corrosion services for a range of applications.
To learn more about Element’s credentials, please visit our About Us page. For more information about our corrosion testing services, or to speak to our experts, contact us today.
“Reliable, professional and always helpful with ongoing testing and any last minute requirements we need.”
Matthew Moore
Atlas Copco IAS UK Limited
Specialists in the Oil and Gas Industry
Element offers global corrosion testing services for the Oil & Gas industry, ensuring compliance, safety, and longevity of your pipelines and infrastructure assets.
Read MORE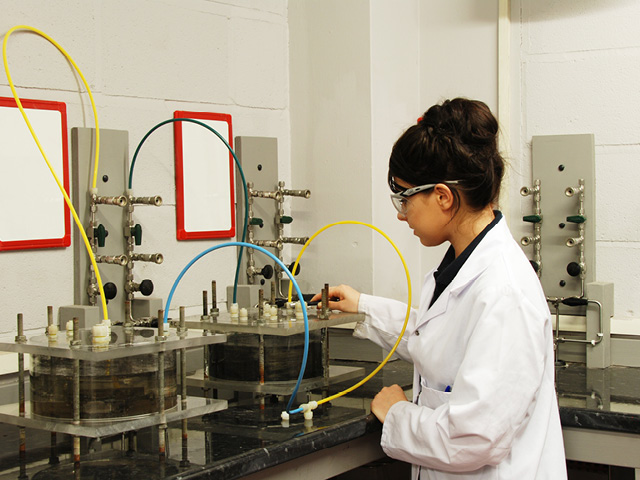
Webinar: Corrosion of Stainless Steel
This webinar shows examples of corrosion damage and guides you through how to avoid corrosion in your stainless steel products to prevent product failure and costly repairs.
Watch NowIntergranular Corrosion Testing: An Overview of ASTM A262
ASTM A262 is a common intergranular corrosion testing method that can quickly screen batches of material to determine corrosion susceptibility. The ASTM A262 testing specification contains five unique intergranular corrosion tests.
LEARN MOREMedical Device Corrosion per ASTM F2129
Element offers medical device corrosion testing per ASTM F2129. Learn more about how our Engaged Experts use this method to assist manufacturers in assessing their implants' resistance to pitting and crevice corrosion.
Learn MOREOur Services
Element has one of the most comprehensive ranges of mechanical and physical testing services.
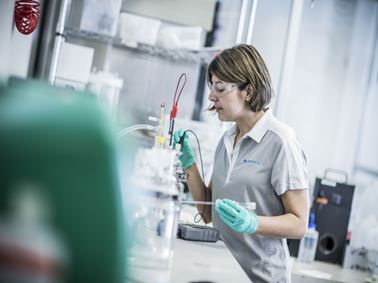
Electrochemical Corrosion Testing
Find out how electrochemical corrosion testing helps prevent harmful interactions between metallic medical devices and biological processes by assessing corrosion susceptibility using cyclic potentiodynamic polarization per ASTM F2129.
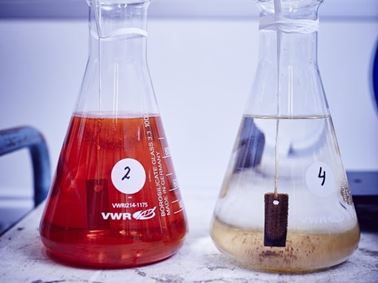
Intergranular Corrosion Testing
Find out more about Element's intergranular corrosion testing service (IGC) to help prevent deterioration of materials along grain boundaries.
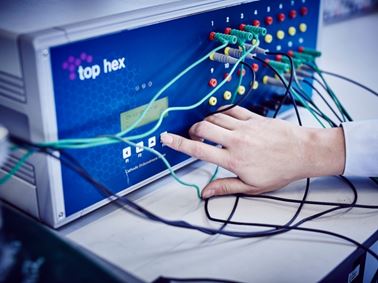
Galvanic Corrosion Testing
Element offers galvanic corrosion testing to ASTM G71, ASTM G82 and to clients' specific standards to help select the right material combinations for an application.
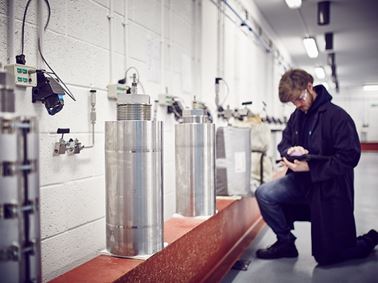
High Pressure High Temperature (HPHT) Testing
Element offers an advanced HPHT testing program for polymers, metals, coatings and components used in highly aggressive environments.
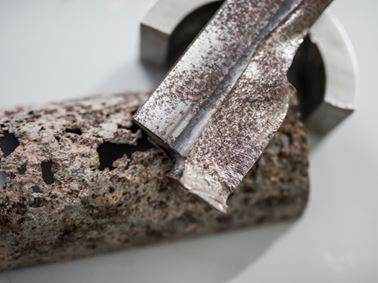
Pitting & Crevice Corrosion Testing
Element’s ASTM G48 corrosion testing ensures the quality of material and resistance to pitting and crevice corrosion in ambient, elevated pressure and chloride environments.

Slow Strain Rate Testing (SSRT)
Element’s Slow Strain Rate Testing (SSRT) uses Rippled SSRT methods to ensure the safety and reliability of metals.
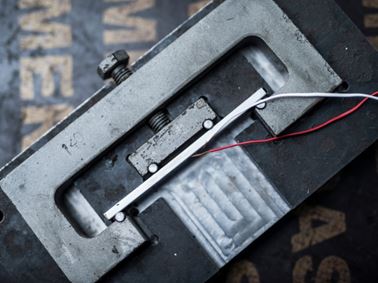
Stress Corrosion Cracking (SCC) Testing
Element’s Stress Corrosion Cracking (SCC) testing evaluates the susceptibility of metals to cracking failure under tensile stress and corrosion.
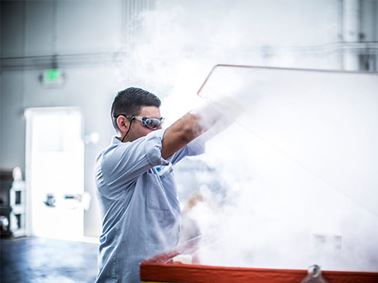
Salt Spray Testing
Element's Engaged Experts conduct salt spray testing, or natural salt spray (NSS) to evaluate the integrity of a coating in a corrosive environment or to test the corrosion resistance of a product or material.
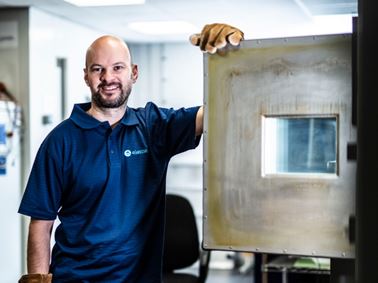
Mixed Flowing Gas (MFG) Testing
Element tests the impact that mixed flowing gasses (MFG) and contaminants have on aerospace, automotive, consumer products (electronics) and medical devices to determine the resistance to corrosion from gasses in the atmosphere and increase product life span.