Talk to an Expert
+1 888 786 7555Weld Failure Analysis - Identifying the Root Cause of Weld Defects

By Engaged Expert
Jeff MolnarJeff has been dynamically and actively engaged in materials science for nearly 30 years. He is a recognized expert at solving the most challenging forensic cases faced across national and international business sectors.
Even when the cause of weld defects may seem obvious, careful forensic investigation reveals opportunities to save time and money. The case studies below illustrate how weld failure analysis results can pinpoint vulnerabilities and areas for improvement in the welding process.
Weld failure analysis with electron microscopy
Excellent quality metallurgical welds that are reliable, robust, and fully fit for service are absolutely paramount to human safety. This is especially true in aerospace, transportation, and energy sectors where metallurgical weld failures often result in catastrophic events that are extremely costly; and, even worse, end up taking human life. The weld-metal itself; however, should not always be the very first thing to blame. Correctly and accurately identifying the root cause of weld failures requires an objective and thorough forensic investigation that almost always hinges on the application of electron microscopy (EM).
Below are a couple of detailed examples of forensic analyses where EM and optical workflows have been used to confirm that defective and/or contaminated weld material was the root cause of failure. In each case, the most likely pathway to the observed defects in the weld were also identifiable.
The impact of weld porosity on welding failures
CASE 1: Visually obvious and large voids within the weld metal (a) resulted in multiple origin fatigue fracture [progression lines and the coalescence of multiple fatigue cracks are indicated with yellow arrows in (a)]. This large series of void structures in the weld metal was initially thought to be formed because of contamination; and, lower spatial resolution imaging via backscattered electrons (b) did at first suggest this could be true {because of the apparent Z-contrast at the bottom of the voids}.
Moderate resolution imaging (c) at ~7500X coupled with energy dispersive spectroscopy (EDS); however, showed that contamination was not the case as many areas (blue triangles) showed mainly Fe/Mn being present that was known to be characteristic of the weld metal. This approach further revealed that the surface morphology at the base of large primary, secondary, and tertiary voids was crystallographic, faceted, highly directional, and non-contaminated (yellow ellipses); thus confirming weld metal solidification occurred within void spaces that were filled with entrapped gas.
Inspection within these micro-voids (d) at even higher spatial resolution (~30,000X) further revealed that nano-crystalline Fe-rich (i.e. not contaminated) weld metal had directionally solidified as “fingers” within the micro-voids; additionally confirming that high-velocity gas impingement most likely occurred during welding.
Preventing weld failures with good welding practice
CASE 2: The girth weld on a large diameter pipeline was fractured and the origin of the break was identified by tracing convergent steps and arrest lines to the location shown in (a). Stereo optical microscopy then revealed that the weld metal exhibited burn-through (black ellipse), and this confirmed that the field operator laid the weld bead too slowly thus allowing time for burn-through.
The optical inspection also showed that contamination was present at the origin of fracture. Looking at the origin of the break via SEM/EDS then confirmed that gross contamination was present, and was due to Ti, Si, Ca, O, and Al (blue triangles). Final confirmation that the observed contamination on the break surface was embedded within the weld metal was then obtained via cross-sectioning through the origin (c). This location was then further analyzed via SEM/EDS (d).
Taking the extra step to analyze the cross-section (white diamond) via EM additionally revealed that iron oxide platelets were embedded within Ti/Si/Ca rich contamination. Taking the time for this additional level of analysis on the cross section not only confirmed contamination was in the weld, but also that a rusted, dirty welding rod was most likely grabbed in the field, hastily cleaned, and used to manufacture the remaining portion of the girth weld.
This analysis case highlights the importance of good welding practice and how simple oversight of a single step can lead to a catastrophic release.
How Element can help
Whether your requirement is in weld procedure or welder certification, weld testing, inspection or forensic failure analysis, our welding services can support you at every stage of the asset life cycle. For more information about our weld testing methods, contact an expert today.
Find related Resources
More from Element
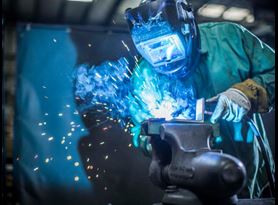
Weld Testing
Our team includes Certified Welding Inspectors (CWI), Certified Welding Engineers (CWEng), and industry-dedicated technical staff to assist with projects across sectors and applications.
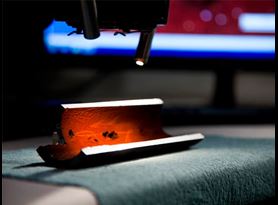
Failure Analysis
Find out how Element's global team of failure analysis experts learn from the past, to help prevent failures in service.
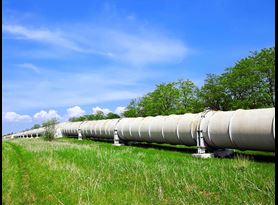
Identifying the root causes of weld failures
Read this free white paper to go behind the scenes of an investigation of the fundamental causes behind a coating failure.
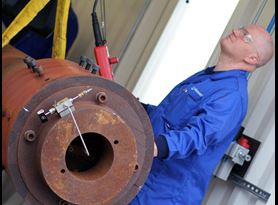
Fatigue Testing of Pipeline Girth Welds
Read our case study to understand the approach to validating the fatigue performance of pipeline girth welds. In particular, the variables that need to be considered when planning a test program to qualify such welds' fatigue performance