Ensuring the Quality of Laser Welds
Need a small, precise weld joint between two pieces of metal? Consider laser welding it.
It’s hard to believe that only a half-century ago the “laser” (originally an acronym for Light Amplification by Stimulated Emission of Radiation) made the leap from concept to reality.
The year was 1960, when the first laser – a 694 nm ruby laser – produced the first of those characteristic bright-red spots. The early lasers, while a significant technical accomplishment, were low on power and had limited industrial application. It wasn’t until the mid-1970’s that lasers crept into everyday life.
Notable early applications included supermarket barcode scanners and laser printers.Eventually, higher-powered lasers were developed which were suitable for industrial uses such as welding and cutting of metals. Today, laser beam welding (LBW) is widely used to join (weld) small, intricate metal parts. When focused on the joint, the laser beam heats the two metal components to their melting points - creating a molten “puddle”. As the beam advances along the joint, the molten “puddle” cools and solidifies, joining the two metals into one.
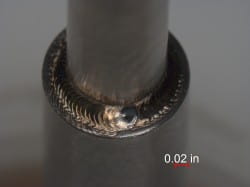
Laser welding has some distinct advantages over other welding processes:
- Great for thin materials; capable of welding thicker sections too
- Minimal shrinkage & distortion
- Capable of automation with high travel speeds
- High depth-to-width ratio (deep penetration with narrow bead width)
- Small heat affected zone
- Can be used on irregular shaped parts or hard-to-reach areas
As with all welding processes, laser welding must be carefully controlled to ensure quality. A poorly controlled process opens the door to cracks, porosity, insufficient penetration, and lack of fusion – any of which could cause failure of the weld joint if present in sufficient amounts.
You might be saying to yourself, “These welds are so tiny, how in the world am I supposed to ensure their quality?!” The good news is there are established methods for ensuring quality of laser welds. Here are the three I believe to be most important:
1. A Written, Qualified Welding Procedure
In the welding world, document welding procedures using a Welding Procedure Specification (WPS). A WPS is a document that specifies all of the essential variables that must be defined and controlled when making a particular weld joint. Some of these essential variables are joint design, base metal types, filler metal types, shielding gases, laser type, and laser settings.
A WPS is usually required to be qualified (or proven) through testing. This usually involves making test welds following the WPS, and subjecting the test welds to appropriate materials tests to ensure they meet all engineering requirements. WPS qualification tests may include nondestructive inspection (visual, penetrant, x-ray, leak check), or destructive testing (bend, tensile, hardness, metallography). Exact testing requirements are usually specified in the contract documents (engineering drawings or quality specifications). WPS qualification test results are documented in a Procedure Qualification Record (PQR).
Sample laser welding WPS and PQR forms can be found in AWS C7.4 Process Specification and Operator Qualification for Laser Beam Welding, Appendix A & B.
2. Qualified Welding Operators
The person operating the laser welding machine should be trained and should demonstrate his/her ability to produce welds that meet the applicable quality requirements. Training should include not only proper operation of the equipment, but also the safety considerations of working with lasers.
Demonstration of the operator’s ability usually involves testing similar to WPS qualification. Operator qualification may include nondestructive and/or destructive testing, depending on contract requirements. The results of this testing are documented in an Operator Process Qualification Test Record (OPQTR), or similar form.
Samples laser welding OPQTR form can be found in AWS C7.4 Process Specification and Operator Qualification for Laser Beam Welding, Appendix C.
3. Quality Inspection of Welded Production Parts
To ensure the ongoing quality of laser welded parts, a manufacturer should have a quality assurance procedure in place. The details of this quality assurance procedure may vary from organization to organization, or from contract to contract. Most will include sampling plans, inspection procedures, acceptance criteria, and periodic destructive evaluation.
Laser welding comes with many benefits. If properly controlled, it can produce reliable, high-quality weld joints in your product.
Find related Resources