E&L With Dr. Scull: Materials Risk Assessment for E&L Studies
Extractable and leachable testing shortens time to market and ensures patient safety by validating the quality and effectiveness of your drug product.
What is a Materials Risk Assessment (MRA)?
- To review all data provided by the vendor regarding the materials of construction (MOC) of the individual components, including any vendor-supplied extractables data
- To provide an assessment of the gaps between the vendor data and the data required to meet regulatory agency expectations
- To provide a study design that, when executed, will fill the identified data gaps, resulting in a complete E&L submission package
- The MRA serves as a “submission-ready” document that provides a comprehensive review and assessment of the MOC and outlines target compounds that are likely to be found during the E&L study
- The MRA not only provides a study design but also includes the rationale behind it
- The conclusion of the MRA may determine that the vendor-supplied data for the MOC is sufficient for satisfying the extractables requirements, thus eliminating the need for further testing and allowing the project to progress directly to the leachables portion
How do we get started on our MRA?
I have the information. What do I do with it?
The Results (an example)
Figure 1: The schematic of a piston pump used to contain and deliver a topical gel product. (Figure courtesy of Dr. Michael Ruberto)
Component |
Schematic # |
Leachables Risk |
Container Round |
Not Shown |
Moderate Risk |
Piston round |
Not Shown |
Low Risk |
Cap |
1 |
Low Risk |
Actuator outer |
2 |
Low Risk |
Membrane |
3 |
Low Risk |
Actuator inner |
4 |
Low Risk |
Reduction plug |
5 |
Low Risk |
Bellows |
6 |
Moderate Risk |
Adapter Ring |
7 |
Low Risk |
Adapter |
8 |
Low Risk |
Label |
Not Shown |
Moderate Risk |
In future blog posts, Jim will discuss how we get from the vendor data to the final risk designation and, ultimately, the E&L study design.
To be notified via email about the latest blog posts, articles, certification updates, and Element news, update your subscription preferences here.
For more information about extractable and leachable studies or to request a quote, please contact us today!
About the Author
James R. Scull, Ph.D., Technical Director for Element Life Sciences, has more than 32 years of pharmaceutical development experience spanning all areas, from discovery support through manufacturing. His expertise includes applied analytical chemistry, toxicology, multi-dimensional separation science, extractable & leachable studies, CMC product development and oligonucleotide analysis.
Find related Resources
Learn more
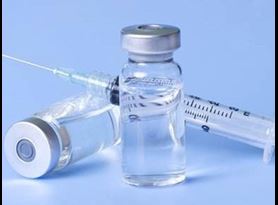
Extractables and Leachables Studies
Element's extractables and leachables studies offer tailored solutions that ensure patient safety and compliance with industry standards.
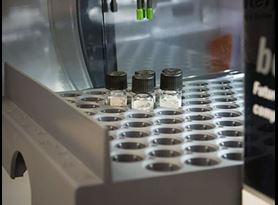
Pharmaceutical Method Development and Research
Element provides a full suite of pharmaceutical method development and research services to bring your products to market at optimal speed.

Pharmaceutical Container and Packaging Testing
We provide professional testing services for containers, container closures and pharmaceutical packaging on polymers and glass containers to several pharmacopeia methods, including USP, EP, and JP methods.
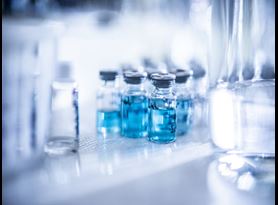
USP <761> Qualitative and Quantitative NMR Analysis
Cathy Moore, Ph.D., provides an overview of NMR spectroscopy in this free recorded webinar to help you better understand the technology, data output, and capabilities of the method.