Verify the internal design, materials, construction, and workmanship of your electronic components with expert destructive physical analysis (DPA).
Destructive physical analysis is a testing process that helps to ensure electronic components are fabricated to the required standards. DPA can also be useful in uncovering process defects for identifying production lot problems.
Element's component analysis laboratories perform all major analytical functions like DPA, failure analysis (FA), counterfeit analysis, and material analysis on electronic components. Our DPA testing techniques align with industry standards and methods used in most military and space program requirements. Our expertise can help you resolve production challenges, uncover counterfeit parts, and build a better, more reliable product.
Destructive physical analysis test methods
Our standard DPA program includes external visual inspection (EVI), hermeticity testing, acoustic microscopy, decapsulation/delidding, internal visual inspection, bond pull testing, die shear testing, scanning electron microscopy/energy dispersive X-ray spectroscopy (SEM/EDS), X-ray radiography, X-ray fluorescence (XRF), microsection (cross-section) analysis, and optical microscopy.
We commonly perform DPA to MIL-STD-1580 using the test methods MIL-STD-202, MIL-STD-883, and MIL-STD-750
Counterfeit component investigations
Our counterfeit component test group includes industry experts and SAE committee chair working to develop the first industry-recognized test method standard to provide uniform requirements, practices and methods for testing electronic parts to mitigate the risks of receiving or using suspect counterfeit electronic parts.
Why choose Element?
Element has decades of experience performing destructive physical analysis and is well-versed in DPA procedures. In addition to the common industry standards, Element frequently performs client specified DPA test flows based on custom requirements. We provide a full-service laboratory with knowledgeable technicians and industry-leading technology, allowing us to perform a variety of testing services for PCBs, assemblies, and other electronic components, including in-depth failure analysis and investigations for counterfeit parts.
Contact our experts to learn how we can help you bring superior products to market.
Learn more
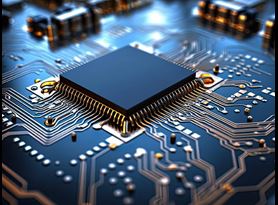
Printed Circuit Board Testing
Ensure your printed circuit boards and finished printed circuit assemblies are of the highest quality and compliant with relevant standards with comprehensive PCB testing from Element.
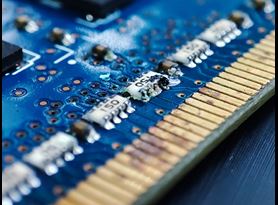
Printed Circuit Board (PCB) Failure Analysis
Understand and rectify the root causes of PCB failure with industry-leading PCB failure analysis from the testing experts at Element.
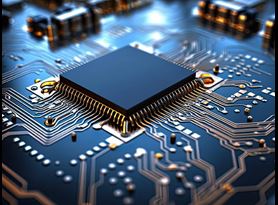
IPC Testing & Certification
Element is accredited by IPC to inspect and test printed boards, components, and materials, and to validate products subject to IPC standards.
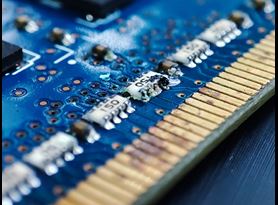
Surface Insulation Resistance (SIR) Testing
Measure the reliability of your printed circuit boards under real-world temperature and humidity conditions with surface insulation resistance (SIR) testing from Element.