Element Pointe-Claire's state of the art 3D laser microscope scans a laser across a given surface in order to gather topographical information. Until recently, laser microscopes were limited to either an 8-bit or 14-bit photomultiplier to receive reflected laser light, which limited the resolution to the micrometer scale. Now, Element Pointe-Claire has a 16-bit laser microscope capable of producing high resolution and high-magnification 3D images across any shape or material with resolution in the nanometer scale. The end result is a no-contact, low-noise 3D microscope that provides surface detail with color variations (65,536 shades) and resolution in three dimensions that conventional microscopes simply cannot match.
The microscope is capable of producing complex geometric measurements and detailed surface profiles, in addition to wear path depth and surface morphology. The high angle of detection makes it an ideal solution for measuring curved, sloped or even tilted parts.
These capabilities make the 3D microscope the ideal choice for surface roughness and erosion damage measurement and characterization. While conventional microscopes can provide a top-level view of porosity or inclusions within a given material, the 3D microscope can give these anomalies scale with nanometer resolution.
This makes the 3D microscope an excellent complement to Pointe Claire’s existing Scanning Electron Microscope (SEM), a tool heavily relied upon in failure analyses of fractured surfaces. The SEM provides magnification from above, while the 3D microscope shows the depth of fracture and depth of measurement.
- • Complex geometry measurements
- • Detailed surface profiling
- • Wear path depth and characteristic morphology;
- • Transfer layer measurements (Tribology)
- • Erosion damage characterization
- • Surface tension measurements
- • Porosity and contamination (NACE/SSPC)
- • Film thickness and anomaly characterization
- • Detection of coating pits (depth measurement)
Current applications involve failure analysis, inclusion counting, porosity tracking and identification, surface profiling, film thickness and surface roughness. Industries and applications that could benefit from the 3D microscope include coating and plating applications (where maintaining plating thickness is a concern), the additive printing market, repairs of corroded and defective parts by cold spray, in addition to hard-facing markets using plasma-transferred arc (PTA), laser cladding (LC), High Velocity Oxygen Fuel (HVOF) and High Velocity Air Fuel (HVAF).
Element's 3D microscope analysis capabilities can provide you with the best failure analysis available. Trust Element to be your testing partner, and request a quote today!
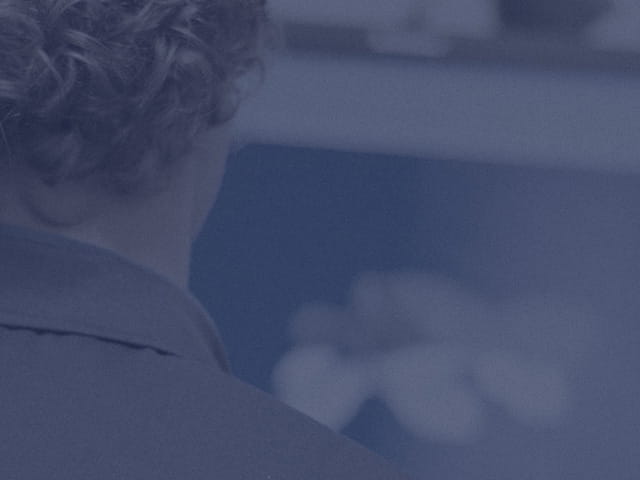
Request a Quote
Our team of over 9,000 Engaged Experts working across North America, Europe, The Middle East, Australia, Asia and Africa are ready to support you.
Learn more
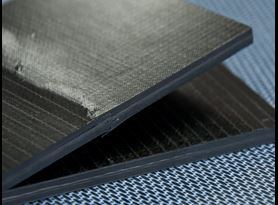
Failure Evaluation
Element offers comprehensive capabilities to assist in determining root cause failure.
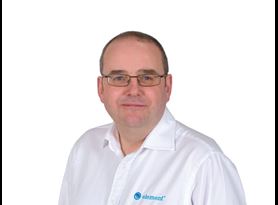
Expertise our most valuable asset
Our people are the key to our success and our most valuable asset, working tirelessly to solve our clients' most complex challenges.
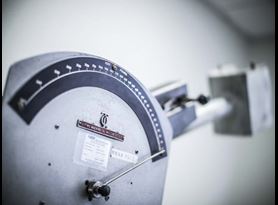
Charpy Impact Testing Services
Find out about the complete range of Charpy impact testing services that area available from Elements worldwide network of accredited laboratories.
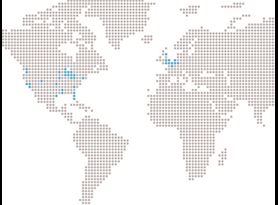
Element Locations
Learn more about our laboratories - where they are located; the unique capabilities they have and how they can help you solve your technical and commercial challenges.