Avoid costly and hazardous infrastructure damage with Element’s Corrosion Under Insulation (CUI) inspection and testing services . Our ISO-accredited labs ensure reliable results and full regulatory compliance. Choose Element for precise, cost-effective CUI solutions.
What is CUI Inspection?
CUI (Corrosion Under Insulation) inspection helps identify corrosion that occurs under insulation due to exposure to moisture and oxygen. This type of corrosion typically affects insulated carbon and low alloy steel equipment operating at high temperatures in cyclic service within the CUI temperature range. When moisture infiltrates the insulation, it creates an aggressive environment that accelerates corrosion. This corrosion often goes undetected for long periods, causing significant damage to infrastructure, which can be hazardous and expensive to repair. In severe cases, this damage can lead to costly site remediation, prolonged downtime, and legal issues.
Benefits of CUI Inspection
- Safety Enhancement: Ensuring the integrity of insulated equipment minimizes the risk of hazardous incidents, protecting both personnel and infrastructure.
- Regulatory Compliance: We offer a wide range of testing services following ISO 19277:2018, including heat conditioning, adhesion testing, artificial aging, thermal cycling, and Cryogenic exposure. This ensures that coatings and materials are thoroughly evaluated for performance under various conditions.
- Operational Efficiency: Element's thorough inspection processes ensure continuous operation by maintaining the reliability of essential equipment, reducing unexpected shutdowns.
- Industry Expertise: Element’s team of experts provides valuable insights and support tailored to your requirements. We serve a range of diverse industries, providing customized solutions to meet specific industry challenges.
- Customized Solutions: Element offers bespoke testing programs tailored for research and development, including testing of alternative materials and modified test regimes, providing specific solutions based on unique client needs.
To provide a comprehensive evaluation of your materials' integrity, Element offers extensive expertise in various corrosion testing methods, including electrochemical corrosion testing alongside comprehensive Corrosion Under Insulation (CUI) testing. This ensures your products remain reliable and safe in diverse environments, simplifying your testing needs under one roof.
Reducing the High Costs of Regular CUI Inspections
Regular and thorough CUI inspections can be expensive, requiring specialized equipment and skilled technicians. The costs associated with unexpected repairs and replacements can be substantial, adding to the financial burden. Our comprehensive testing services, such as heat conditioning and thermal cycling tests, ensure that coatings and materials perform optimally, thereby extending the life of your infrastructure and minimizing maintenance costs. Investing in Element's CUI inspections ultimately leads to cost savings by preventing severe damage and reducing the need for frequent inspections.
Addressing Reliability Issues in CUI Inspections
Ensuring the consistency and reliability of inspections across different inspectors and cycles can be challenging. The risk of false positives or negatives can lead to unnecessary repairs or missed corrosion, both of which have significant implications. Element’s CUI inspection services are built on a foundation of accuracy and reliability. Utilizing a variety of testing methods, including artificial aging and cryogenic exposure tests, ensures that our inspections provide consistent and precise results. Our experienced specialists follow standardized protocols in accordance with ISO 19277:2018, reducing the risk of false positives and negatives. By delivering reliable data, Element enables you to make informed decisions about maintenance and repairs, ensuring that resources are allocated efficiently and effectively.
The Impact of Protective Coatings on CUI Prevention
As part of a holistic approach to CUI prevention, protective Coatings are often utilized in conjunction with installation design, insulation choice, and inspection regimes. In such cases, selecting an appropriate coating requires understanding the material's performance characteristics when subject to high-temperature cyclic and CUI conditions.
Why Choose Element?
Element’s team of specialists has extensive experience in CUI products and testing to standards like ISO 19277:2018. Our experts bring years of industry knowledge to every inspection, ensuring that you receive the highest quality service tailored to your specific needs.
Our specialized corrosion laboratories adhere to stringent international standards and protocols, including ASTM, NACE, and API and are all ISO/IEC 17025-accredited. By leveraging our expertise and state-of-the-art facilities, you can trust Element to deliver accurate and reliable corrosion under insulation testing inspections that meet or exceed industry benchmarks.
To learn more about Element’s credentials, please visit our About Us page. For more information about our corrosion under insulation testing, or to speak to our experts, contact us today.
Failure Analysis of Pipeline Coatings
This free white paper includes an extensive case study of the failure analysis of a 12-inch diameter Fusion Bonded Epoxy (FBE) coated steel pipe that showed blistering of the coating and corrosion on the surface.
Read MorePredicting component life with corrosion modeling
Erosion within oil and gas pipelines is a serious problem. Corrosion modeling using the Computational Fluid Dynamic method can accurately predict the location of burn-throughs.
Read MoreMore from Element
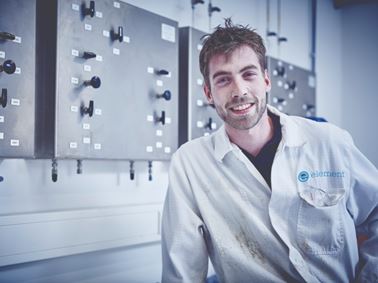
Hydrogen Embrittlement Testing
Element performs Hydrogen Embrittlement (HE) testing to ASTM F591, Galvanically Induced Hydrogen Stress Cracking (GHSC) to NACE MR0175/ISO 15156 and Hydrogen Induced Stress Cracking (HISC) testing.
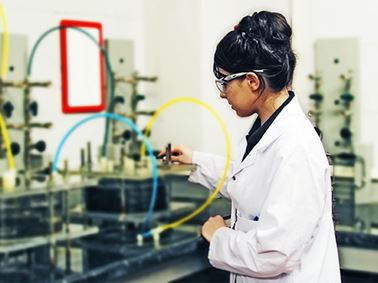
Hydrogen Induced Cracking (HIC) Testing
Element’s HIC tests evaluate material susceptibility to hydrogen induced cracking in a sour environment in accordance with NACE TM0284.
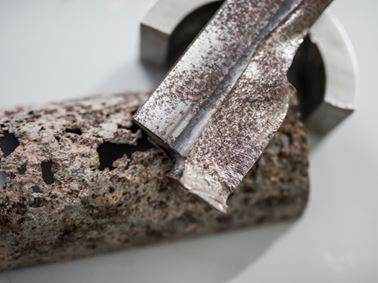
Pitting & Crevice Corrosion Testing
Element’s ASTM G48 corrosion testing ensures the quality of material and resistance to pitting and crevice corrosion in ambient, elevated pressure and chloride environments.
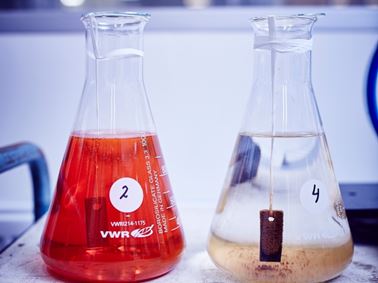
Corrosion Testing Services
Find out about Elements extensive corrosion testing expertise in the Energy industry across a global network of laboratories.