Why risk unexpected or premature failure in your materials due to hydrogen embrittlement (HE)? Element offers precise hydrogen embrittlement (HE) testing to the ASTM F519 standard for the Energy, Aerospace, and Automotive sectors, ensuring the reliability and safety of critical metal components. With many years of expertise in corrosion testing, you can trust Element to mitigate risks and maintain industry compliance, providing you with peace of mind.
What is Hydrogen Embrittlement (HE) Testing?
Hydrogen embrittlement (HE) testing determines the performance of materials in a corrosive environment under the influence of tensile stress by evaluating the material’s ductility as a result of hydrogen absorption. Hydrogen embrittlement occurs when metals absorb hydrogen during plating processes or corrosion, leading to a loss of ductility and toughness, ultimately resulting in premature failure under static loads.
There are two types of hydrogen embrittlement:
- Internal HE: This occurs when hydrogen enters metal during forming, coating, plating, cleaning, and finishing operations.
- Environmental HE: This results from hydrogen absorption from the environment.
Key Benefits of Partnering With Element For Hydrogen Embrittlement (HE) Testing Services
- Reliable Performance: Our HE testing ensures that your materials will perform reliably in corrosive environments under tensile stress, reducing the likelihood of premature failure and ensuring product longevity.
- Improved Safety: By identifying potential weaknesses in materials due to hydrogen embrittlement, our testing helps identify issues before they arise, protecting both your products and end-users from potential hazards.
- Cost Savings: Early detection of hydrogen embrittlement issues through our testing can prevent costly failures and downtime, ultimately saving you money in the long run by avoiding expensive repairs or replacements.
- Enhanced Product Quality: Through comprehensive evaluation of materials' ductility and toughness, our HE testing helps maintain high product quality standards, ensuring that your materials meet or exceed performance expectations.
- Industry Compliance: Following strict industry standards such as ASTM F519, our testing procedures guarantee compliance with regulatory requirements, giving you confidence in the reliability and legality of your products
- Advanced Expertise: Properly conducted HE testing requires specialist knowledge of materials science, metallurgy and testing methods. Our experts have deep knowledge and years of experience in corrosion testing, to support you with your hydrogen embrittlement assessment.
- Assurance In All Conditions: You need to know your product will withstand corrosion in a diverse range of environments and conditions. Our advanced simulations and test methodologies help test a wide range of eventualities, providing you with assurance.
“The greatest benefit of conducting hydrogen embrittlement testing is that it helps to ensure the safety and reliability of critical components that are subject to high stress and exposure to hydrogen, such as those used in the aerospace, automotive, and energy industries. ”
Vikram Nanda
METALLURGY & METALLURGICAL FAILURE ANALYSIS EXPERT
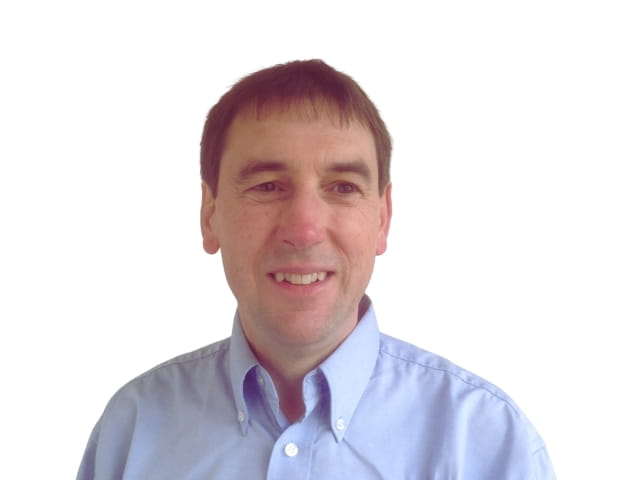
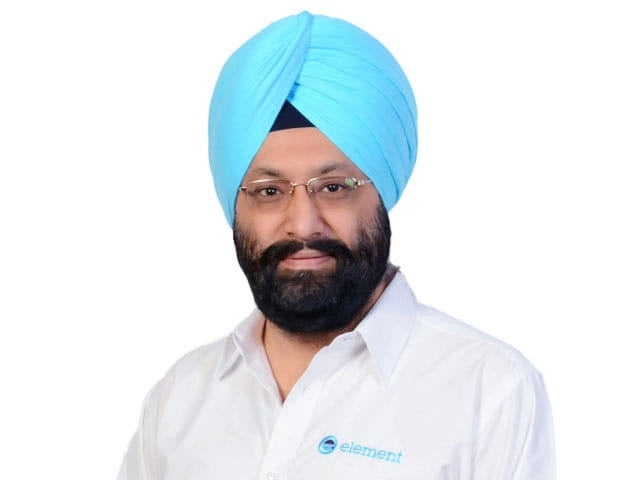
Sustained Load Testing (SLT)
Element performs mechanical hydrogen embrittlement testing according to ASTM F519. The test specification outlines the use of Sustained Load Testing (SLT) to measure the possibility of hydrogen embrittlement in steel materials by applying uniaxial tension for up to 200 hours. Additionally, ASTM F519 provides guidance for evaluating the processes of surface preparation, pretreatments, and the plating/coating of steel parts.
Galvanically Induced Hydrogen Stress Cracking (GHSC)
The presence of hydrogen (introduced via corrosion) in metal may result in reduced ductility and increased susceptibility to cracking in the presence of tensile stress (applied and /or residual). Element’s GHSC testing helps evaluate the hydrogen embrittlement sustainability of the corrosion-resistant products and metal materials, when galvanically coupled, as the cathode, to another metal (carbon steel). We perform testing in accordance to NACE MR0175/ISO 15156.
Hydrogen Induced Stress Cracking (HISC)
Subsea Oil & Gas production equipment is exposed to severe conditions which have led to a number of failures of Corrosion Resistant Alloys (CRAs). Our hydrogen embrittlement testing labs can carry out HISC testing of nickel alloys and duplex stainless steels, widely used in subsea components, to investigate how hydrogen influences materials’ behavior under mechanical stress.
Why choose Element?
Element conducts HE testing according to ASTM F519 standards, serving many industries including Energy, Aerospace, and Automotive. With our deep knowledge and years of experience in corrosion testing, we ensure accurate assessment of materials in simulated service environments. Our comprehensive testing services rigorously follows industry standards, guaranteeing reliability and compliance. Additionally, our specialized testing for industries like subsea oil & gas production equipment demonstrates our commitment to tailored solutions.
FAQ: What is Hydrogen Embrittlement?
Discover hydrogen embrittlement as Vikram Nanda, an expert in metallurgy and metallurgical failure analysis, provides answers to commonly asked questions in this article.
Read MOREHydrogen Fuel Cell Design Analysis
To improve the design of hydrogen fuel cells, Element Digital Engineering used CFD modeling to help optimize the flow paths within the cell core.
Read MORERelated Services
As a recognized world- leader in the provision of corrosion testing services, Element performs a number of testing services related to hydrogen embrittlement.
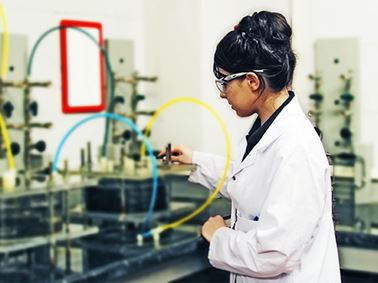
Hydrogen Induced Cracking (HIC) Testing
Element’s HIC tests evaluate material susceptibility to hydrogen induced cracking in a sour environment in accordance with NACE TM0284.
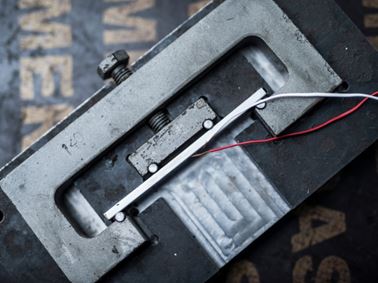
Stress Corrosion Cracking (SCC) Testing
Element’s Stress Corrosion Cracking (SCC) testing evaluates the susceptibility of metals to cracking failure under tensile stress and corrosion.

Slow Strain Rate Testing (SSRT)
Element’s Slow Strain Rate Testing (SSRT) uses Rippled SSRT methods to ensure the safety and reliability of metals.
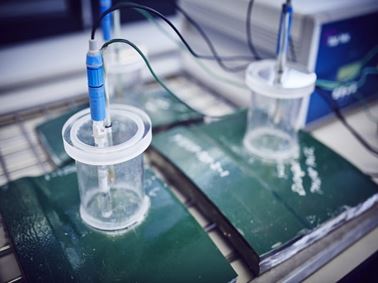
Sour Service Corrosion Testing
Find out about Element's sour service corrosion testing services for evaluating how equipment and materials will hold up in environments rich in hydrogen sulfide and other caustic gases.