ASTM G154 and ASTM G155 Explained

By Engaged Expert
Dr. Todd MennaDr. Todd Menna is a highly experienced Materials Failure Analyst who focuses on polymeric, rubber, metallic, ceramic, and composite materials and devices.
The ASTM G154 and G155 tests evaluate the resistance of a nonmetallic material to simulated sunlight and moisture exposure. When rays of sunlight—particularly UV rays—bombard a surface, they degrade smaller pigment particles, changing the surface color and creating a chalky effect. Cracking, peeling, de-glossing, oxidation, and loss of mechanical properties are additional outcomes of exposure; sometimes such deterioration can even occur through glass. Moisture takes its own toll on surfaces, and the combination of sunlight and moisture can amplify damage, costing millions of dollars of depreciation each year. The ASTM G154 and G155 tests assist manufacturers in designing products that can withstand exposure to sunlight and moisture.
However, it’s important to remember that both tests provide exposure approximations. Ultimately, the most realistic way to test for weathering is to allow the product to degrade in real-time, with outdoor testing panels. Such real-time testing facilities are typically situated in hot locales, as sunlight’s damaging effects are magnified at high temperatures. In the United States, the gold standard locations for outdoor exposure testing facilities are located in Arizona (for simulating hot, dry climates) and south Florida (for simulating hot, humid climates). Due to time constraints, however, many producers employ the G154 and G155 laboratory chamber tests to obtain exposure results in shorter time periods.
Florescent vs. Xenon Arc Testing
Accelerated testing instruments used in the G154 and G155 tests approximate performance via intense exposure to the most damaging elements in sunlight - ultraviolet light. UV Rays make up just 5% of sunlight, yet they cause the majority of exposure damage. By exposing a product to UV rays, a test instrument can simulate these exposure results.
In the ASTM G154 test, fluorescent bulbs simulate sunlight exposure within a controlled test chamber. The ASTM G155 test is similar, but it utilizes xenon arc lamps to simulate full-spectrum sunlight weathering. Because the xenon arc light is most similar to natural sunlight, the ASTM G155 test is most used for outdoor weatherization testing. Fluorescent light has a lower correlation to natural sunlight than xenon arc light; therefore, ASTM G154 test method is generally used to simulate indoor or interior exposure.
ASTM G154: Our Most Popular Accelerated Weathering Test
Although an infinite variety of exposure conditions can occur, the ASTM G154 test typically consists of exposing samples to alternating cycles of UV light exposure followed by periods of darkness. Cycles of moisture can be distributed throughout the light exposure cycles.
In ASTM G154 testing, UVA-340 bulbs create the best correlation with outdoor exposure, as they emit the closest wavelengths to damaging wavelengths within natural light (295 to 365 nm). Different UV bulbs are useful for different testing purposes. For instance, UVA-351 lamps can recreate the portion of UV light filtered through windowpanes. Therefore, these bulbs are useful for testing interior applications. UV-B light accelerates the brittleness that materials, particularly polymers, may suffer as they age indoors. In contrast, UV-A bulbs have a propensity for accelerating color fading and yellowing. If the aim of testing is to boost colorfastness, UV-A bulbs are ideal.
Exposure Testing Considerations - ASTM G154 and G155
It is impossible to recreate nature in the lab. Every location around the globe has its own unique combination of damaging elements, such as pollution, salt spray, and biological attack. Without testing in a specific location over a number of years, it is impossible to perfectly predict product response. As such, the ASTM G154 and G155 tests produce comparative, not absolute data, but these comparative evaluations can still prove extremely valuable to designers. For instance, a slight shift in formula may produce twice as much resistance to weathering. Such outcomes cannot be quickly obtained in outdoor settings; therefore, these weatherization tests are invaluable in timely product development.
Recreate specialized conditions with filters. In xenon arc testing, different optical filters may be applied to shift testing conditions for daylight, window glass, or extended UV spectrum exposure. Similar filters can be used in fluorescent light testing.
Include a control, to act as a weatherization standard. ASTM International recommends that a comparable material of identified performance (a control) be exposed at the same time as the test specimen. This allows for an accurate comparison. Additionally, it’s best to include a minimum of three replicates of each specimen material, for optimized statistical evaluation. Remember, these accelerated weatherization tests cannot exactly reproduce outdoor conditions, as they cannot account for altitude, seasonal variations, local geographical features, and other variables. Control samples and multiple material samples produce the best comparative data.
There is no easy exposure formula. Calculations can be made that estimate the equivalent energy exposure within the test instrument and its correlation with various locations around the world. However, because the actual results can vary with temperature, humidity, altitude, and weather and biological conditions, there is no simple equation for calculating exposure.
Don’t fall for common weathering myths. It may be tempting to assume that shorter wavelengths, continuous exposure, high temperatures, and other variables can result in more intense acceleration. But, each of these variables brings uniquely different results. For example, constant exposure with no temperature cycling fails to recreate the expansion and contraction stresses that materials face in outdoor locations.
The Element Advantage in ASTM G154 & ASTM G155
Element has been helping companies make certain for over 188 years. We can work with you to ascertain the most cost-effective, accurate testing approach for your material. Costs for weatherization testing will vary according to a number of factors, including moisturization, sample size, number of cycles, and more.
Find related Resources
More from Element
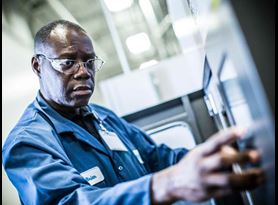
Accelerated Weathering Testing
We provide Xenon Arc testing, Carbon Arc testing and UV Exposure testing to simulate exposure of your products or materials to ultraviolet radiation, temperature and moisture.
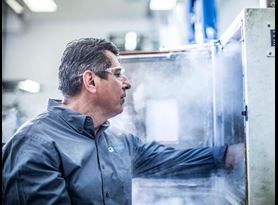
Product Testing
From environmental & dynamic testing to highly specialized tests such as bird strike and hydrodynamic ditching testing, we're the trusted testing partner to the world's most recognized component and system manufacturers.
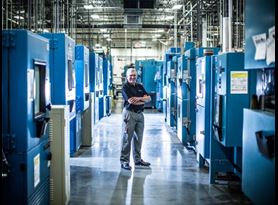
Environmental Testing
Element can provide you with critically important data on your product or part's performance in response to typical or extreme environmental stresses and conditions.
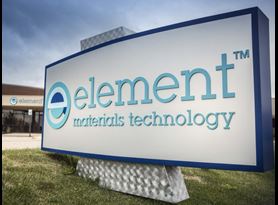
Product Testing Laboratories
Element's product qualification testing labs span the US, UK and Germany, providing testing services to clients in Aerospace, Transportation, Oil and Gas and more.