Fatigue Testing of Femoral Knee Components

By Engaged Expert
Maciej JakuckiMaciej Jakucki has performed and managed a wide variety of medical testing projects and programs to meet FDA and CE requirements.
Total knee replacements undergo a significant battery of tests designed to measure fatigue, constraint, stress distribution, wear, interlock strength, and a variety of other forces. Fatigue testing provides an understanding of a component’s material properties and behavior during cyclic loading. This article will focus on fatigue testing of femoral knee components in both closed and open condition.
Total knee replacement (TKR), or total knee arthroplasty (TKA), is a surgical procedure used to replace the articulating components of the femur and the tibia to eliminate pain due to damaged bone surfaces. The weight-bearing cartilage covering the bones can get worn out or damaged over time, usually due to different types of arthritis such as:
- Osteoarthritis – a degenerative joint disease that breaks down joint cartilage
- Rheumatoid arthritis – a disease that inflames the synovial capsule resulting in excessive synovial fluid
- Post-traumatic arthritis – a condition often occurring from the trauma of injury to a joint
Once the soft, smooth cartilage wears out, the bones contact each other directly, causing severe pain. This can also result in additional bony growths (spurs) as the joint tries to repair and fuse itself, often resulting in additional pain. During a total knee arthroplasty, the surfaces of the bones and the cartilage between them are replaced using either a unicondylar or bicondylar implant. The implants generally consist of three components:
- Femoral component for the distal femur, typically made of Cobalt Chrome per ASTM F75 or other similar specifications
- Tibial tray component, typically made of titanium or Cobalt Chrome
- Congruent plastic insert, made of polyethylene (UHMWPE)
Test specifications and guidance documents
Existing FDA guidance documents and industry test specifications:
- Class II Special Controls Guidance Document: Knee Joint Patellofemorotibial and Femorotibial Metal/Polymer Porous-Coated Uncemented Prostheses; Guidance for Industry and FDA
- ASTM F2083 - Standard Specification for Knee Replacement Prosthesis
- ASTM F1800 - Standard Practice for Cyclic Fatigue Testing of Metal Tibial Tray Components of Total Knee Joint Replacements
- ASTM F1223 - Standard Test Method for Determination of Total Knee Replacement Constraint
While specifications exist for most test methods for knee replacements, there are several additional methods, including fatigue testing of femoral knee components that are not yet defined. Even though this test is commonly performed, no testing standard exists as of the writing of this document. ASTM is in the process of developing a new standard with a potential release in 2020.
As the push for implants to be thinner or more patient-specific continues, it creates a risk of fracture at the different angular junctions. Although rare, some clinical failures have been observed, so mitigating risk with the appropriate test program is crucial. Fatigue testing of femoral knee components is an important step in the validation process to ensure patient safety and device longevity.
Element provides fatigue testing of femoral knee components in several configurations.
Femoral knee component fatigue test configurations
Closing conditions: This configuration applies the load at some flexion angle, usually 90 degrees, inward toward the center of the axis of rotation. The setup simulates loading conditions where improper implant fit or bone loss results in gaps under the femoral component, and it is not fully supported. Failures on the articulating surfaces or intercondylar notch are most common. Closing conditions are currently the most common configurations tested.
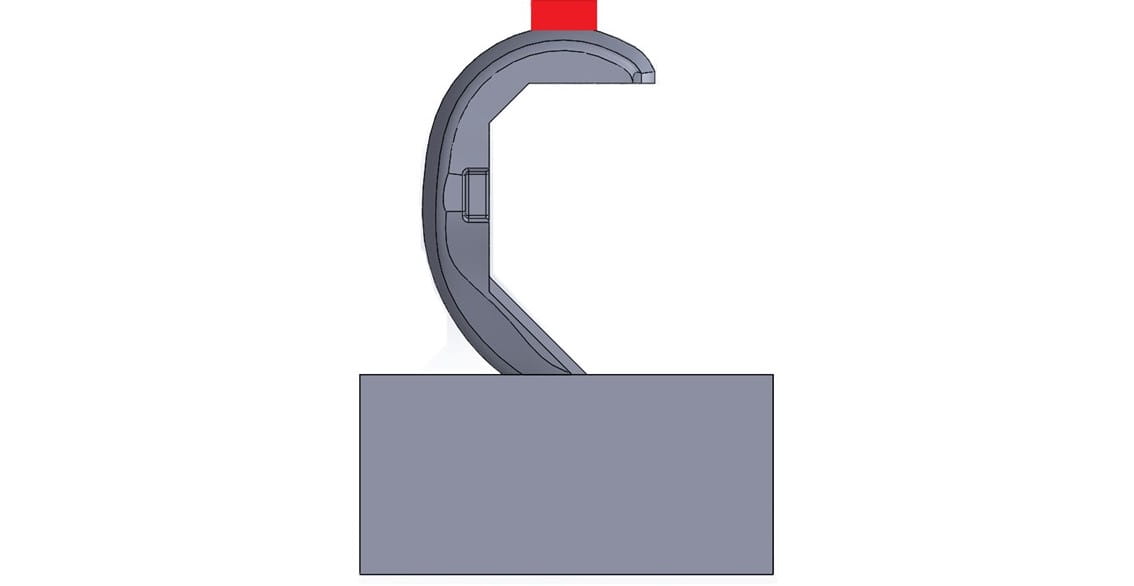
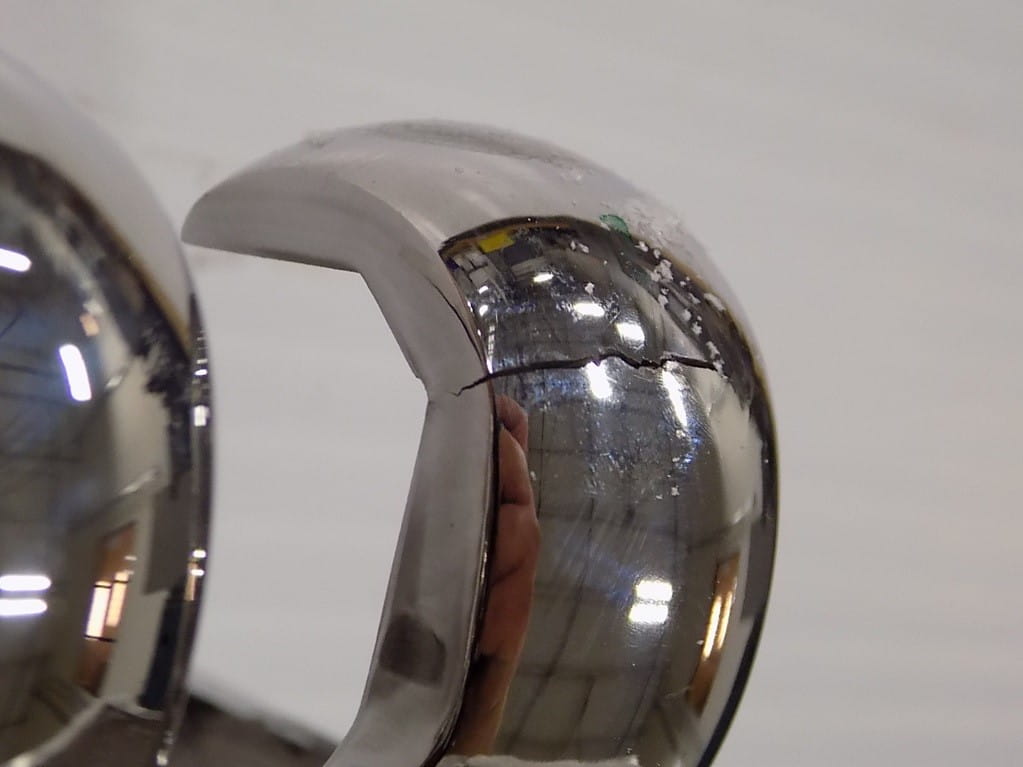
Opening Conditions: In this configuration, the device is loaded so that it splays open the femoral component and applies high stresses to the rough surfaces on the inside of the implant. These forces may cause failure in the clinical setting due to a lack of bony support on the distal femur or improper preparation of the femur during surgery. There are two ways to simulate these forces during testing:
- The femur rests on a fixture replicating the femur with either no distal bony support or mis-angled sagittal cuts. The joint compressive force is applied, forcing the femur onto the fixture and resulting in a splaying or opening load.
- The anterior flange of the femur is clamped, and hooked fixtures apply an opening load to the posterior condyles. This setup is essentially reversed loading of the closing-style test.
Both test methods of opening conditions can generate failures that initiate from the roughened surfaces that contact the bone.
Assembly Configurations: Fatigue testing can also be performed on an assembled knee replacement, modifying the setup to include wedges, revision extensions, offset connectors, angles, or simulating minimum levels of bone support. These configurations are often tested for several reasons:
- To confirm runout to a target load level
- Measure pre and post disassembly forces of components after fatigue testing
- Evaluating fretting corrosion on the modular connections
In Element’s experience, assembly configurations don’t result in femoral fracture of the condyles, unless supported on only one side, but often result in the loosening of components or revision extension post-fracture. The most common configurations involve testing at 0 degrees and multiples of body weight (710 N).
For all of these test configurations, typical testing parameters include:
- Load: multiples of body weight or aligned with the tibial tray cantilever requirements per ASTM F1800 of 900 N.
- Frequency: can range up to 15 Hz depending on the configuration
- Load profile: sinusoidal
- R ratio: 10
- Embedding medium: bone cement or similar
- Target cycles: 10,000,000
The Element advantage
As ASTM works to develop the test specification, our orthopedic device testing experts routinely perform and design custom femoral knee component fatigue testing programs. While most knee implants use similar angles in their femoral components, understanding the impact of the radii, contours, and stress risers due to the angles is critical in understanding femoral fatigue performance, ultimately resulting in less risk for the patient.
Element has one of the most expansive medical device testing scopes in the world, ranging from orthopedics and cardiovascular implant testing to EMC/EMI/product safety testing, and biological and packaging evaluations. We strive to meet all your medical device testing needs in the most expedient, efficient, and responsive way. Contact us today.
Find related Resources
Related Services
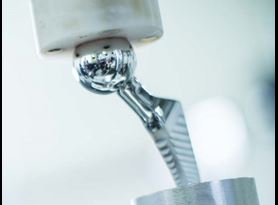
Orthopedic Implant Testing
As a global leader in orthopedic implant testing, Element has years of experience in evaluating hip replacements, knee prostheses, spinal devices and many other implants.
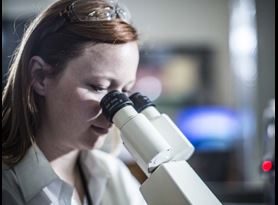
Preventing Fretting Corrosion of Orthopedic Devices
The human body is a corrosive environment that can compromise the performance of orthopedic devices. The test methods outlined in this article aid in preventing fretting corrosion in your device designs.
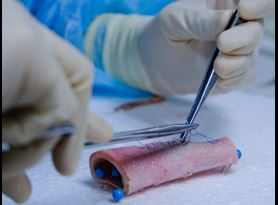
Biomechanical Testing of Cadaveric Specimen
Cadaveric biomechanical testing is one of the most beneficial forms of mechanical testing in the medical industry. Our medical device testing experts explain the advantages and challenges of testing with cadaveric specimens.
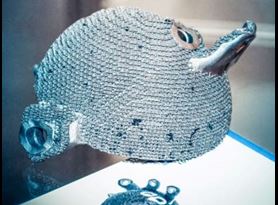
Evaluation Methods for 3D Printed Implants
Compared to traditional materials, additive manufactured materials require qualifying and validating of the powders, structures, individual printers and overall design, creating additional steps for characterization.