Protect your electrical components from environmental corrosion with our Mixed Flowing Gas (MFG) Testing. Get real-world simulation at parts-per-billion precision to identify issues before they impact your aerospace, automotive, or medical devices. Save on warranty claims and ensure product reliability through our streamlined testing process—all while meeting industry standards with one efficient testing partner.
What is Mixed Flowing Gas (MFG) Testing at Element?
Mixed Flowing Gas (MFG) testing evaluates material and electronic component corrosion resistance under controlled environmental conditions. At Element, we replicate real-world exposure by precisely controlling temperature, relative humidity, and gaseous pollutant concentrations for manufacturers in aerospace, automotive, consumer products, and medical device industries. Our testing process delivers detailed insights into your product's long-term performance and durability.
What Can Element Offer You For MFG Testing?
Components & products we test
We comprehensively test electrical and electronic components across aerospace, automotive, medical device, and consumer product applications. Our specialized chambers accommodate various component sizes and configurations, delivering precise corrosion resistance data for materials exposed to multiple atmospheric contaminants. From simple electrical contacts to complex electronic assemblies, we provide thorough testing for all your component needs.
Key tests offered
Our MFG testing capabilities include exposure to multiple gas combinations including chlorine, hydrogen sulfide, nitrogen dioxide, and sulfur dioxide at parts per billion precision. We conduct both standardized and custom testing protocols that adhere to ASTM B827, ASTM B845, IEC 60068-2-60, and EIA-364-TP65A standards, ensuring that testing processes meet globally recognized benchmarks for reliability and accuracy. Our comprehensive testing suite ensures complete coverage of your corrosion testing needs.
Testing capabilities include:
- Multi-gas exposure testing
- Temperature and humidity-controlled environments
- Parts per billion precision testing
- Custom test protocol development
- Long-term exposure assessment
- Accelerated aging tests
Methods and solutions offered
We provide comprehensive corrosion resistance evaluation that helps mitigate risks by delivering precise and accurate data on how your products will perform over time under various environmental conditions. Our testing methods align with global standards while allowing customization to meet your specific industry requirements and product specifications. We deliver detailed reports with actionable insights for product improvement.
Our solutions include:
- Customized test protocol development
- Real-world environmental simulation
- Detailed performance analysis
- Compliance verification
- Comprehensive reporting
- Improvement recommendations
Common Gasses Used for Our Mixed Flowing Gas Testing Include:
- Chlorine
- Hydrogen sulfide
- Nitrogen dioxide
- Sulfur dioxide
- Gasses are tested at levels in the parts per billion range in our advanced chambers.
Cutting-edge equipment we use
Our state-of-the-art MFG chambers feature advanced control systems for precise temperature, humidity, and gas concentration management. These specialized facilities enable highly controlled and repeatable test conditions, ensuring accurate simulation of real-world environmental exposure scenarios and identifying specific factors that contribute to corrosion. Our equipment maintains precise control at parts per billion levels, delivering consistently reliable results for your testing needs.
Equipment features:
- Advanced MFG testing chambers
- Precision gas concentration controls
- Environmental parameter monitoring systems
- Data acquisition technology
- Real-time monitoring capabilities
Which labs offer this service
Our team operates from Product Qualification Testing hubs across the world, providing global access to our expert capabilities. Find out where your nearest Product Qualification Testing hub is on our Locations Page.
How we accelerate product success
Element's MFG testing delivers superior reliability data through our state-of-the-art testing chambers and expert analysis. Our advanced facilities precisely control environmental conditions at parts per billion levels, providing a seamless and efficient process that saves you time and resources while ensuring thorough evaluation of your products. Combined with our comprehensive testing capabilities and global expertise, we provide you with actionable insights that directly improve your product's performance and longevity.
Your Challenges, Our Solutions
your testing partner
Preventing premature component failure
Our advanced MFG testing identifies potential corrosion issues before deployment, helping you prevent costly component failures and maintain product reliability by addressing factors contributing to corrosion. This extends the lifespan of your electrical components and ensures optimal performance in real-world conditions.
Reducing warranty claim costs
Precise environmental simulation and early problem detection enable you to address potential issues during development, significantly reducing future warranty claims and associated costs through enhanced product robustness and customer satisfaction.
Meeting complex industry standards
Our adherence to ASTM B827, ASTM B845, IEC 60068-2-60, and EIA-364-TP65A standards ensures your products meet globally recognized benchmarks for reliability and accuracy, streamlining your compliance process across all relevant industry and manufacturer-specific requirements.
Optimizing testing time and resources
Consolidate all your testing needs through one provider with our integrated testing approach, saving valuable time and resources while maintaining thorough evaluation standards.
Element Experts at your Service
Browse our experts by discipline and specialty, and explore their skills and experience.
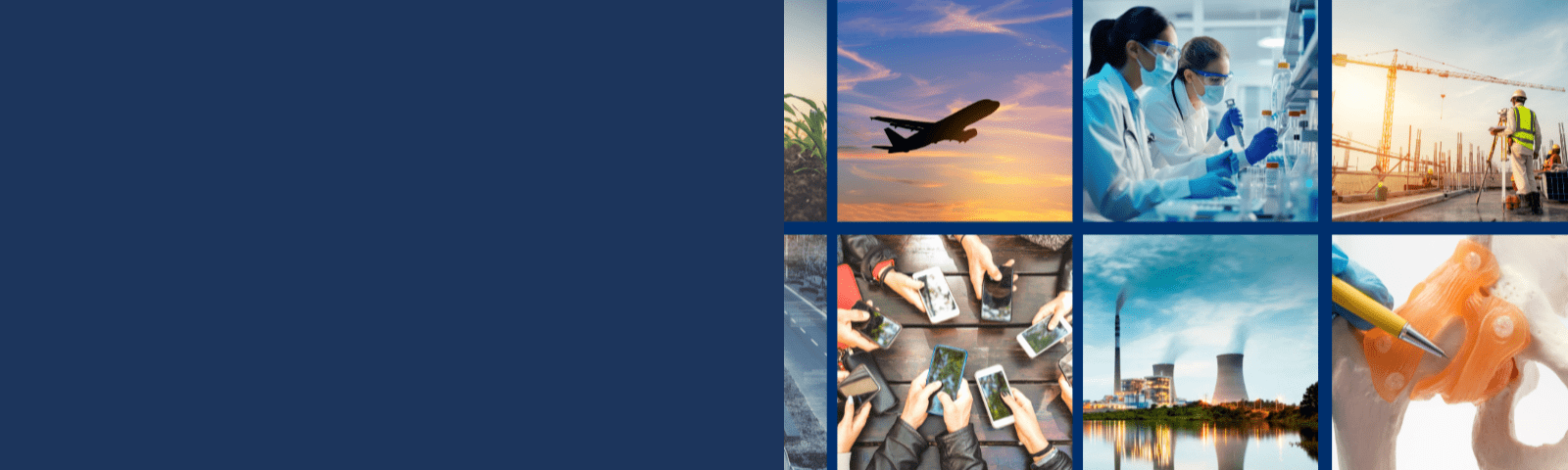
Why Choose Element
Comprehensive testing solutions
One trusted partner for all your testing needs, from MFG to salt spray testing and beyond.
Accurate Simulation
MFG replicates real-world environmental corrosion conditions with parts-per-billion precision to provide reliable data, helping you predict product performance over time.
Quality Control
Element experts help you identify potential corrosion issues before products reach the market, increasing product robustness and customer satisfaction.
Extended Lifespan
Element aids in prolonging the lifespan of electrical components by identifying and mitigating factors that cause premature failure.

Explore our global network of Labs and find your nearest location
View all locationsRelated Services
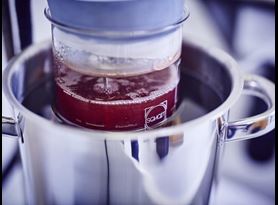
Corrosion Testing
Find out about Element’s corrosion testing services, from salt spray to cyclic corrosion, pitting and crevice corrosion testing.
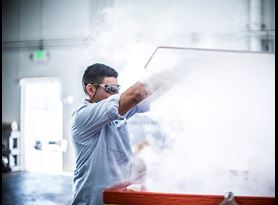
Salt Spray Testing
Find out how our Engaged Experts conduct salt spray testing, or natural salt spray (NSS) to evaluate the integrity of a coating in a corrosive environment or to test the corrosion resistance of a product or material.
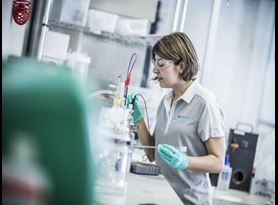
Electrochemical Corrosion Testing
Find out how electrochemical corrosion testing helps prevent harmful interactions between metallic medical devices and biological processes by assessing corrosion susceptibility using cyclic potentiodynamic polarization per ASTM F2129.
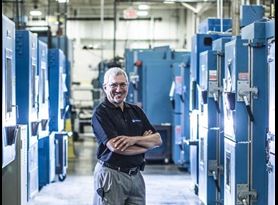
Automotive Weathering
Find out about Element's automotive weathering testing services for materials and components, including a plethora of different tests, from UV light to xenon arc and carbon arc.