Element’s pipeline testing facilities perform fatigue testing on steel catenary risers in our laboratory and on-site at the point of fabrication. Our testing containers can quickly be mobilized to various locations, making Element both flexible and faster than any other testing provider on the market.
Offshore oil companies commonly employ Steel Catenary Risers (SCRs) as a means of connecting surface installations with subsea pipelines. Steel catenary risers are subject to harsh environmental conditions that include cyclic loading as a result of wind and wave motion, tidal flow, vortex-induced vibration (VIV), and operational changes to temperature and pressure.
These conditions make welds, and other stress concentrating features, sensitive to fatigue cracking when in service. To mitigate against premature failure while in service, fabricators are often required to test the fatigue resistance of any proposed weld procedures before their use in SCR installations.
Weld fatigue testing
Two approaches are used to assess the fatigue sensitivity of welds; small-scale testing on extracted coupons, and full-scale testing on entire welds:
- Small-scale testing, while cheaper, has several limitations. The residual stress profile of the weld is altered by coupon extraction, the applied stress profile is not representative of operation, and it can miss stress-sensitive features present in the original weld.
- Full-scale testing, conversely, allows the entire weld to be tested without alteration to its stress profile, using rotating bending stress that more accurately simulates the stress conditions seen in service. This stress can be applied by using large equipment to mechanical bend the welded pipe string, or by vibrating the test string near its natural resonant frequency (near resonance method). The advantage of this is that it can produce high-stress ranges in samples using relatively small, low-powered vibratory motors. It tests the full 360 degrees of girth welds, and it can provide higher cycle frequencies (generally: 25-30 Hz), which speeds up testing.
Element’s mobile fatigue testing solutions
Element’s resonant fatigue testing rigs are fully integrated into modified shipping containers, making the rigs self-contained, modular, and mobile. All containerized test rigs are capable of testing pipe strings ranging from 4.0 m to 10.0 m in length, and with outside diameters (OD) up to 24 inches (610 mm), while fixed rigs have the capacity to test beams with outside diameters up to 38 inches (965.2mm).
All rigs use state-of-the-art software developed in-house by Element, which allows precise control of system parameters during testing, such as pipe deformation, temperature, and test cycles. Each container is equipped with its internal lifting system, and all equipment necessary to load, test and unload prepared test strings.
The containerized design has several benefits over conventional lab-based models:
- It allows each rig to be mobile, allowing for quick and easy mobilization between Element and Client sites.
- It creates an intrinsic barrier between the test equipment and personnel by limiting access and improving security, as well as increasing safety for operators and site staff.
- It enables tests to be remotely monitored through the use of external workstations and CCTV cameras.
- It removes the need for overhead lifting during sample loading due to the presence of integrated dual hoist systems.
- It allows the rigs to be located in uncovered areas outside of site buildings, freeing up valuable floor space.
To find out how our experts can advise on weld fatigue testing on catenary risers, or to request a quote, contact us today.
Fatigue Testing of Pipeline Girth Welds
This white paper provides an overview of the approach and the variables that need to be considered when planning a test program to validate the fatigue performance of pipeline girth welds.
Read MoreFracture Mechanics in the Environment (in-situ)
Learn more about the detrimental effect of Cathodic Protection, CO2, and H2S or other environmental parameters on fracture toughness of carbon steel pipe material.
Read MoreFracture Mechanics in Sour Service: Some Characterization Tests on SENT and SENB Specimen
This article provides better understanding of how the SENT test technique influences fracture toughness of pipelines in sour service environments.
Read MoreMore Services
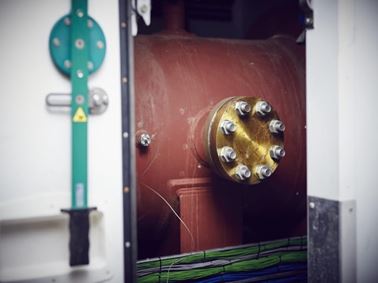
Corrosion Testing
As a world leader in corrosion testing services, Element provides effective corrosion testing programs to help you ensure your materials are safe, reliable, and fit for purpose.
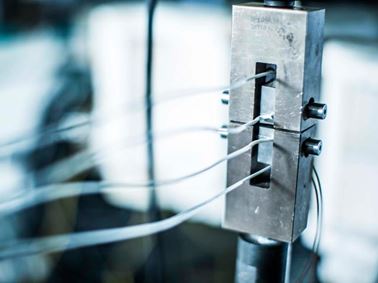
Fracture Toughness Testing
Element provides fracture toughness testing for determining material characteristics and longevity of metallic, nonmetallic, and advanced materials.
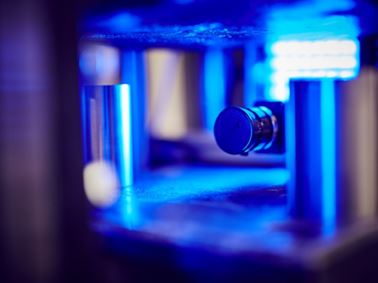
Engineering Critical Assessment (ECA) Services
Element provides Engineering Critical Assessment (ECA) to determine if a flaw in welded structures is safe from brittle fracture, fatigue, or creep.
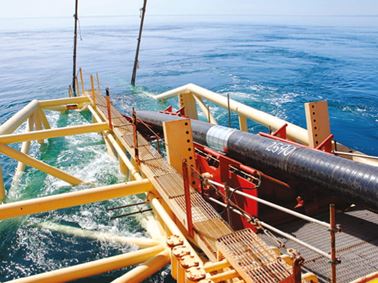
Coatings Testing
Find out about Elements range of coatings testing services designed to help to make certain that materials, products and pipelines we test for our customers are protected from corrosion, ultraviolet light, water penetration, heat, abrasion and chemicals.