Element’s range of fracture mechanics and fracture toughness testing services for all environments help you accurately estimate and prolong component lifespan, reduce costly repairs andimprove designs. Leveraging years of experience in testing for the energy sector, coupled with state-of-the-art laboratory facilities, our experts can also conduct fracture toughness tests in highly corrosive environments, including elevated and sub-ambient temperatures, providing results that closely mimic actual material behaviour in real-world use.
Fracture Toughness Testing vs Fracture Mechanics Testing – what’s the difference?
Fracture toughness testing measures a material's resistance to crack propagation, helping to determine the point at which a crack in your material will grow uncontrollably and cause failure in service. In comparison, fracture mechanics testing broadly evaluates your material's behaviour in the presence of cracks. It involves studying how cracks start, grow, and propagate under various conditions and stress scenarios.
By performing both fracture toughness and fracture mechanics testing, you can ensure that materials possess the necessary resistance to crack propagation (fracture toughness) and will behave predictably under various stress conditions (fracture mechanics). This combined approach leads to the development of safer, more reliable materials and structures.
Benefits of Fracture Mechanics and Fracture Toughness Testing with Element
- Meet Industry Compliance: Ensure that your components are fit for international markets by providing evidence of adherence to a range of standards, from BS 8571 to ASTM E1921.
- Set Custom Test Schedules: Our experts will work with you to create a custom test procedure and can accommodate nonstandard fracture mechanics protocols tailored to your specific application or environment.
- All Your Mechanical Tests Under One Roof: As a single-source provider of mechanical testing services, we can offer a streamlined approach and provide a comprehensive range of supporting tests, helping you optimize resource utilization.
- Predict Material Behaviour: By combining Data from fracture toughness testing and fracture mechanics testing services, our experts can help you conclude your material's real-world behaviour. This proactive approach helps you identify weaknesses and vulnerabilities before the product goes to market, enabling necessary improvements to mitigate risk.
Specialized Fracture Toughness Testing for Sour Service Environments
Element provides specialized testing services designed for challenging environments, such as sour service, with a focus on the oil and gas industry. Pipelines and equipment in this sector are often exposed to corrosive gases and liquids. With extensive experience in corrosion testing and advanced laboratory facilities, we perform in-situ fracture toughness tests under highly corrosive conditions, accommodating both elevated and sub-ambient temperatures. Our dedicated sour service fracture toughness testing includes designing and characterizing test procedures specifically for carbon steels and corrosion-resistant alloys, guaranteeing reliable and appropriate data essential for Fitness For Service (FFS) and Engineering Critical Assessment (ECA) analyses.
Reduce costly repairs
Element’s fracture toughness and fracture mechanics testing helps reduce spending by offering in-depth analysis and understanding of material behaviour under diverse conditions. By identifying potential weaknesses and failure points in materials, our experts help you make proactive improvements in design, reducing the likelihood of unexpected failures. This early detection and correction of flaws prevent failures that would otherwise lead to expensive repairs and downtime. Additionally, our custom testing analyses cater to specific applications, ensuring materials are suitable for their intended use, which enhances overall product reliability and longevity. By accurately estimating your component lifespan and optimizing maintenance schedules, we can help you avoid unnecessary replacements and extend the operational life of your equipment, reducing costs.
Our Fracture Mechanics and Fracture Toughness Testing services and capabilities
Element is well equipped to perform this testing and analysis on a vast range of specimen size and crack geometries, including but not limited to:
Why choose Element?
Whether you operate in Transportation, Aerospace and Defense, Oil and Gas, Power Generation, or Infrastructure industries, our tailored fracture mechanics and toughness testing solutions ensure your products meet the highest standards. Our experts collaborate with you to select the ideal fracture toughness and fracture mechanics tests, enabling you to accurately estimate the lifespan of your components, reduce costly repairs, improve designs, and extend component life expectancy.
In addition to standard fracture mechanics testing methods, we offer specialized testing for sour environments, ensuring your components perform reliably. We help you draw vital conclusions about the safety, fitness, and longevity of your metallic, non-metallic, and advanced materials. Contact us today to elevate your product quality and performance.
Fracture Mechanics Testing Whitepaper
Applying fracture mechanics to predict pipeline cracking and failure. This article provides an understanding of the different test methods and sample geometries used to determine fracture toughness. FREE DOWNLOADFracture Mechanics in the Environment
To learn more about the detrimental effect of environmental parameters on fracture toughness, download our article below.
FREE DOWNLOADFracture Toughness Testing in Sour Service
Our Engaged Expert, Rodolfo Amoriello has carried out research to develop a better understanding of how the SENT test technique influences fracture toughness in sour service. LEARN MOREFracture Toughness Testing of PMMA Bone Cement
In this article, we discuss the methodology for measuring fracture toughness of polymethyl methacrylate (PMMA) bone cement, used within the medical industry for arthroplasty surgery.
LEARN MORERelated Services
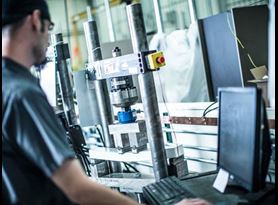
Fatigue Testing
Find out how Element's fatigue testing labs help companies meet quality requirements and create safer, stronger, more successful parts and products.
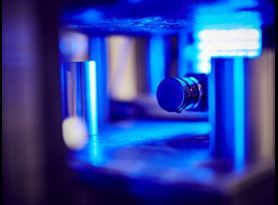
Engineering Critical Assessment (ECA) Services
Element provides Engineering Critical Assessment (ECA) to determine if a flaw in welded structures is safe from brittle fracture, fatigue, or creep.

Metallurgical Testing
Find out about Element's range of metallurgical testing services, including microscopy, corrosion evaluation, hardness and on-site services.
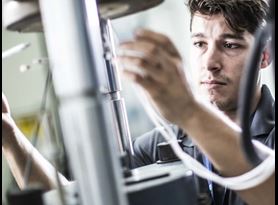
Mechanical & Destructive Testing
Element's mechanical tests are part of our destructive testing services, they show whether a material or part is suitable for its intended mechanical applications.