DRUM PEEL

Miguel Jiménez is an innovation expert with over 12 years of experience in the field of advanced materials and product qualification technologies across a wide range of sectors including aerospace, defense, renewables, metallurgic and healthcare industries.
Development of test tooling and procedure for in situ characterization of peel and interlaminar fracture properties
DRUM PEEL is a national project led by Element Seville. This project is focused on the characterization of the behavior of different elements joint by adhesives at service conditions. It is crucial to evaluate the quality of the bonded joint and the determination of parameters which define its mechanical behavior under fracture, not only for designers but only for the quality control of the manufacturing process.
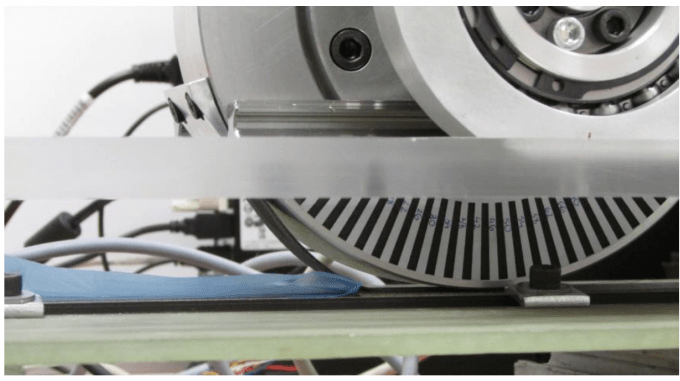
Main goals of DRUM PEEL project
In aeronautics industry and other technology areas, there exists an increasing use of composite materials in the primary aircraft structures. Moreover, the use of bonded joints between composites instead of mechanical bolted joints is increasingly widespread. This requires a better understanding of the behavior of these joints under real loading conditions causing a detachment of the joint elements.
DRUM PEEL aims to develop a portable system for drum peel test able to assess interlaminar and peel strengths of aircraft components which are joint through adhesives. This will allow performing the validation of aeronautic elements in their manufacturing lines, strongly saving costs, since logistics and operation times are reduced.
Element Seville role in DRUM PEEL project
As mono-beneficiary, Element Seville is in charge of all of the tasks within DRUM PEEL project. Its activity starts with a research of the state-of-the-art, identification of needs and definition of the product requirements. At the same time, a study of the stresses which are produced during the test is carried out through numerical modeling. Then, prototype design and manufacturing is conducted, followed by the definition and performance of the validation system and qualification process.
The results of the projects are disseminated as part of a specific work-package, which includes a patentability study for the developed device. Thus, Element Seville achieves a unique equipment in the current field of adhesive joint validation, enabling its consolidation as one of the reference laboratories in the aeronautic industry at European level. DRUM PEEL project execution is planned through a time span of 15 months, starting in March of 2017 and finishing in May of 2018, with a total budget of Funding entities: CDTI PiD EXP: 00098733 / IDI – 20170386; & CTA
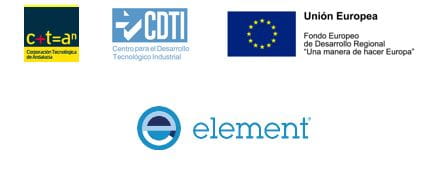
Find related Resources