Preconditioning Stents for Fatigue Testing through Simulated Use Testing
Simulated use testing of implantable cardiovascular medical devices is a well-established non-clinical engineering test used to serve many purposes including delivery, deployment and retraction of a stent, particulate evaluation, and surgeon training.
The FDA’s Non-Clinical Engineering Tests and Recommended Labeling for Intravascular Stents and Associated Delivery Systems document outlines performing simulated use testing by tracking the device through an in vitro fixture, and mimicking challenging in vivo conditions (e.g., a tortuous path, aqueous environment). ASTM F2394-07 (2017) – Standard Guide for Measuring Securement of Balloon Expandable Vascular Stent Mounted on Delivery System provides further guidance with an example of such a setup for coronary indication stents.
Simulated use testing for fatigue preconditioning
While tracking fixtures are routinely used for simulating device deployment in vitro, one application that is not discussed often is their use for fatigue preconditioning. There are typically a few thousand cycles of fatigue loading applied to the device as preconditioning, but how about preconditioning of the device before it is deployed in the fatigue test instrument?
Fatigue test instruments typically employ straight or bifurcated mock vessels that may not fully mimic the tortuous deployment paths devices are subject to in vivo. Preconditioning devices before fatigue testing is where anatomically-correct in vitro fixtures come into play. The fixtures help precondition devices that will undergo fatigue testing in a physiologically-relevant environment by several cycles of deployment and retraction, often repeated 5 to 10 times.
In some cases, more complex mock vessel geometries are designed, as we discussed in a recent article on Pulsatile Durability Testing of Complex Intravascular Devices. However, even these designs may come up short on the complexity of the actual in vivo geometries. Therefore, preconditioning in simulated use environments ensures that devices have been exposed to the forces they will experience in vivo prior to fatigue testing.
Simulated use fixtures and environments
A few standards describe deployment tracking fixtures for specific applications. For example, the aforementioned ASTM F2394 includes engineering diagrams in its appendix that simulate coronary vessels with a moderately difficult degree of tortuosity. According to the standard, the fixture can be used with a guide catheter, a guide-wire and the stent-balloon catheter delivery system to simulate the forces the device will encounter in the clinical setting as it is deployed to the lesion site.
There are several commercially-available simulated use setups for a variety of intravascular devices and indications. However, manufacturers often develop their own custom designs based on their specific device, finite element analysis (FEA) and computational fluid dynamics (CFD) modeling. Custom anatomical models are manufactured out of glass or silicone, or 3D printed.
During the simulated use test, in vivo models are immersed in water or saline baths heated at 37°C, and temperature is allowed to equilibrate before devices are deployed. Each device is labeled with a unique identifier for traceability purposes, and labeling continues on to fatigue testing. Devices and delivery systems are closely inspected for any damages or defects prior to and after deployment. After preconditioning in the tortuous path geometry has been completed, devices are ready to be deployed in the durability test instrument for further testing.
In need of simulated use testing?
Our Engaged Experts excel at cardiovascular device fatigue testing and have worked with many challenging device designs and test setups over the last several decades. Contact us to discuss how we can help with your test project.
Element has one of the most expansive medical device testing scopes in the world ranging from orthopedics and cardiovascular implants testing to EMC/EMI product safety testing, and biological and packaging evaluations. We strive to meet all your medical device testing needs in the most expedient, efficient and responsive way.
Find related Resources
Related Services
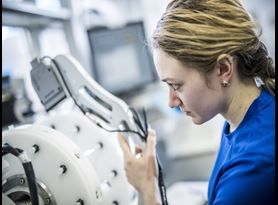
High Speed Stent and Graft Testers
Our medical device manufacturing customers are regularly challenged with short timelines to bring products to market.
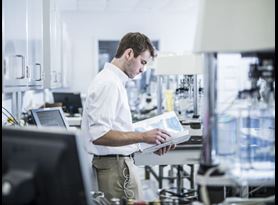
Test Protocol for Medical Devices
A protocol and plan will mitigate your risk, prevent confusion, set clear expectations, and preserve the necessary information for future reference and use.
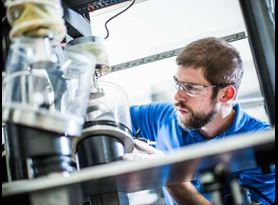
Medical Device Testing
As a comprehensive testing partner, you’ll enjoy the benefit of a single supplier source for all of your testing needs, from mechanical testing and environmental simulation to EMC and wireless device testing.
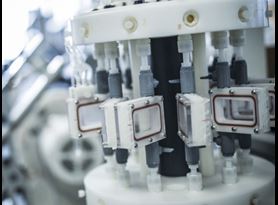
Cardiovascular Device Testing
Element specializes in a wide range of testing for cardiovascular devices, such as stents, grafts, occluders, catheters, heart valves and pacemaker leads.