Ensure your aerospace systems meet the highest safety standards with Element’s precise and reliable windmilling testing. Our advanced capabilities simulate the extreme vibrations caused by fan blade-out events, validating the resilience and compliance of your engines and components. With cutting-edge equipment and proven expertise, we help you confidently address regulatory requirements, minimize risks, and optimize performance, keeping your projects on track and your reputation for safety intact.
What is Windmilling Testing at Element?
Windmilling testing at Element evaluates aerospace systems under extreme conditions caused by fan blade-out events, where detached rotor blades result in significant vibrations and sustained engine imbalance. While these extreme conditions are difficult to replicate in standard testing, our LDS V8 electrodynamic test system can simulate even extreme events, providing the certainty you need to demonstrate your product’s compliance to any standard. Trusted by aerospace manufacturers worldwide, our testing ensures your systems comply with industry standards, withstand real-world stresses, and maintain operational integrity.
What We Offer for Vibration and Windmilling Testing
Components and Materials We Test
Methods and Solutions Offered
Cutting-Edge Equipment We Use
Which Labs We Offer This Service At
Your Challenges, Our Solutions
your testing partner
Replicating Extreme Real-World Conditions
Simulating fan blade-out events is complex. Our LDS V8 electrodynamic test system replicates these conditions, ensuring systems withstand real-world stresses and provide reliable data for safety & performance validation.
Meeting Stringent Compliance Standards
Ensuring compliance can be challenging. Our windmilling testing delivers precise results to demonstrate your products meet industry and regulatory requirements, giving you the confidence to bring compliant systems to market.
Preventing Critical System Failures
Unexpected stresses can lead to critical failures. Our testing identifies vulnerabilities under extreme conditions, helping you design and deliver systems that maintain integrity and protect passengers and assets.
Access to Cutting-Edge Facilities
Specialized testing equipment isn’t always accessible. At Element Warwick, our advanced lab offers the tools and expertise required to meet the most demanding windmilling test requirements with efficiency and precision.
Element Experts at your Service
Browse our experts by discipline and specialty, and explore their skills and experience.
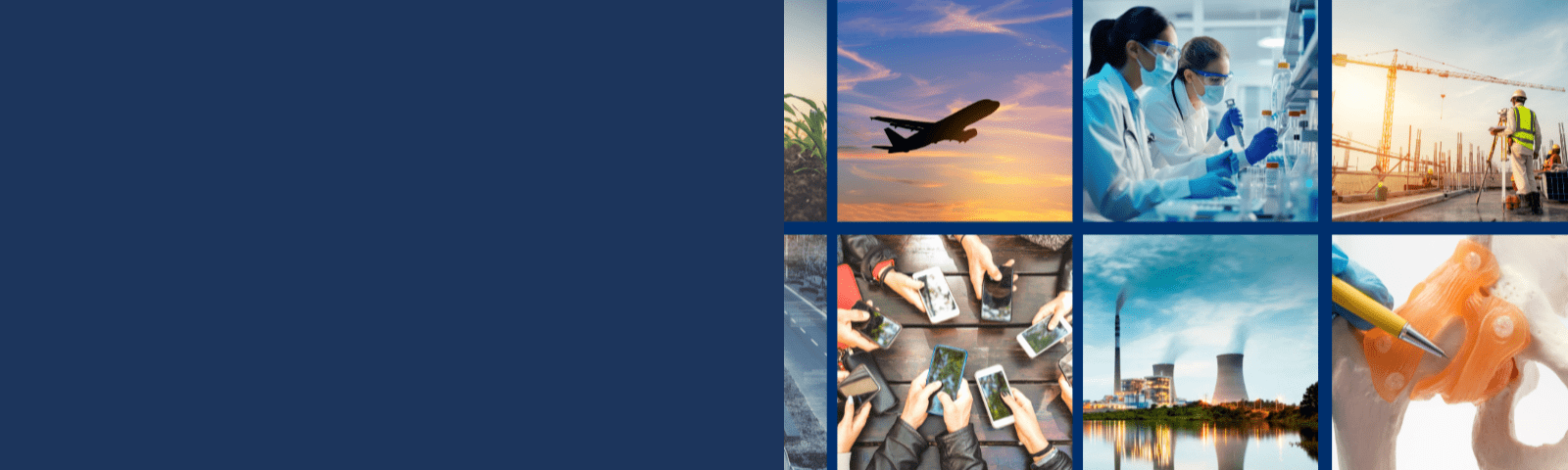
Why Choose Element
Advanced Testing Capabilities
Our state-of-the-art LDS V8 system ensures accurate replication of extreme conditions for reliable results.
Trusted Industry Expertise
Decades of experience in aerospace testing make us a reliable partner for your most critical projects.
Compliance You Can Count On
We help you meet tough industry standards, ensuring your systems perform safely and effectively.
Global Reach, Local Support
With a network of specialized labs, we offer accessible and comprehensive testing solutions tailored to your needs.

Explore our global network of Labs and find your nearest location
View all locationsRelated Services
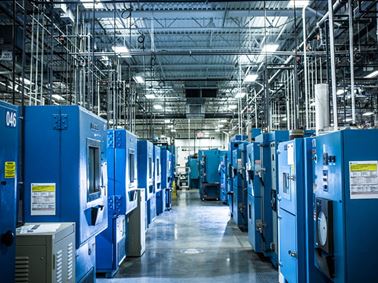
Product Qualification Testing Services
Find out how Element provides critical compliance, reliability and qualification testing to clients in Aerospace, Transportation, Energy and more.
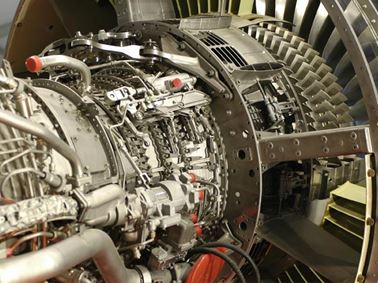
Aerospace Engine Testing
Find out how Element makes certain that aircraft engines meet all safety standards and testing requirements, even in the eventuality of a catastrophic, fan blade out event.
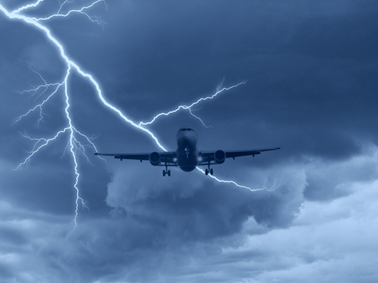
Aircraft Lightning Strike Testing
Our lightning protection testing services help ensure that, in the event of a direct strike, your electronics, equipment and materials continue to perform without failure.

Aerospace EMI EMC Testing
State-of-the-art ISO/IEC 17025:2005 accredited laboratories enable us to test a wide range of products from the smallest components to the largest electrical power management systems for commercial and military aircraft.
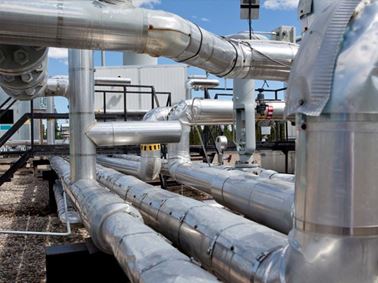
Explosive Atmospheres Testing
Find out how Element works with airplane manufacturers to produce and design equipment that can operate in fuel-air explosive atmospheres.
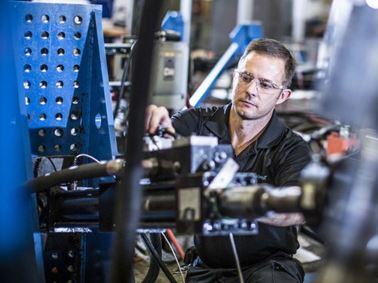
Dynamics Testing
In addition to vibration testing, Element provides a range of dynamics testing including acceleration, shock, drop, structural, fatigue and rotating load simulations.
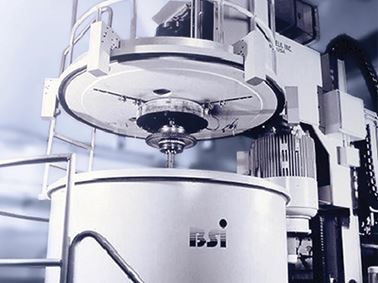
Spin Testing
Find out how Element tests all rotating components within aero engines to help make certain that they are safe and reliable when in-service.
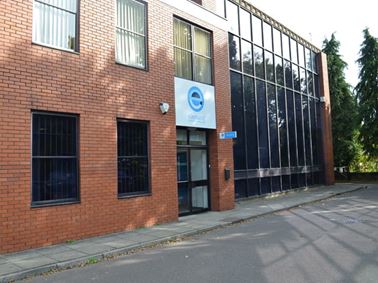
Element Warwick
Our Warwick site is our European Environmental Testing centre of excellence and an SC21 signatory site, with UKAS accreditation to BS EN ISO/IEC 17025:2005.