What are Corrosion Inhibitors and Why is Testing Important?
Benefits of Corrosion Inhibitor Testing with Element
- Enhance Safety and Compliance: By conducting corrosion inhibitor testing, you can improve the safety and compliance of your pipeline assets, reducing the risk of failures and enhancing overall operational safety. Adhering to the most relevant ISO and ASTM standards will provide stakeholders with confidence in the reliability and industry compliance of your pipelines and infrastructure.
- Reduce Costs and Mitigate Risk: Effectively preventing corrosion-related failures, such as leaks and bursts, you can mitigate operational and financial risks, leading to cost savings over the lifespan of your critical infrastructure.
- Gain Comprehensive Insights: Our experts can simulate a wide range of high-pressure, high-temperature, flow regimes, and sweet and sour environmental conditions, providing a comprehensive picture of corrosion inhibitor effectiveness across all potential future operating environments.
- Receive Global Support: Element's global network of laboratories allows you to receive consistent, high-quality testing results no matter where you are currently based.
- Learn from Experts: Our corrosion experts possess specialized knowledge in corrosion testing. They can offer further supportive testing such as CO2 corrosion, H2S corrosion, and galvanic corrosion testing, ensuring that the most practical combination of corrosion inhibitors is applied to your metals and alloys.
Unique Tests for Unique Projects
Prolong Your Product Lifespan
With custom corrosion testing, we can help you extend your infrastructure's lifespan, reducing the need for costly repairs and replacements. This leads to significant cost savings and promotes environmental sustainability. Prioritizing the lifespan of oil and gas pipelines is essential for maintaining the operational efficiency of your project and ensuring it produces a reliable energy supply.
Your Corrosion Inhibitor Testing Expert
Corrosion inhibitor test methods
Our corrosion inhibitor testing examines metals, carbon steel, and corrosion-resistant alloys using electrochemical methods that replicate various environments, including sweet (CO2) and sour (H2S) conditions for oil and gas applications.
We employ Potentiodynamic Polarisation, Linear Polarisation Resistance (LPR), and Electrochemical Impedance Spectroscopy (EIS) test methods in accordance with the most relevant ISO and ASTM standards to assess the impact and effectiveness of corrosion inhibitors.
Our State-of-the-art Facilities and equipment
Element's advanced testing laboratories can replicate a wide range of high-pressure, high-temperature flow conditions and sweet and sour environmental factors:
- HPHT dynamic autoclaves
- Flow regimes
- Acid gases (sweet and sour)
- Electrochemical monitoring systems
- RCE (Rotating cylinder electrode)
- Flow loop (sweet use)
Why Choose Element?
Our experts specialize in corrosion testing, including CO2, H2S, and galvanic corrosion. With a network of global laboratories, we deliver effective corrosion inhibitor testing with fast, accurate results.
Element is the top provider of Materials Testing, Inspection, and Certification services to the Oil and Gas Upstream sector and a leading international provider to the conventional Fuel and Nuclear Power Generation sector. Our global reach and expertise help prevent corrosion in your critical assets through inhibitor testing. For more information or to speak with an expert, contact us today.FAQ: What is Hydrogen Embrittlement?
Discover hydrogen embrittlement as Vikram Nanda, an expert in metallurgy and metallurgical failure analysis, provides answers to commonly asked questions in this article.
Read MOREPredicting component life with corrosion modeling
Erosion within oil and gas pipelines is a serious problem. Corrosion modeling using the Computational Fluid Dynamic method can accurately predict the location of burn-throughs.
Read MoreIntergranular Corrosion Testing: An Overview of ASTM A262
ASTM A262 is a common intergranular corrosion testing method that can quickly screen batches of material to determine corrosion susceptibility. The ASTM A262 testing specification contains five unique intergranular corrosion tests.
LEARN MORERelated Services
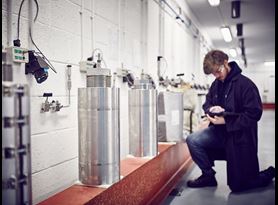
High Pressure High Temperature (HPHT) Testing
Element offers an advanced HPHT testing program for polymers, metals, coatings and components used in highly aggressive environments.
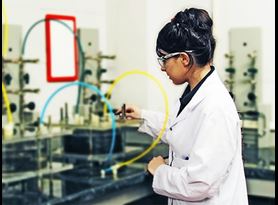
Corrosion Testing
Find out how Element's corrosion testing programs can drastically reduce the risks associated with corrosion.
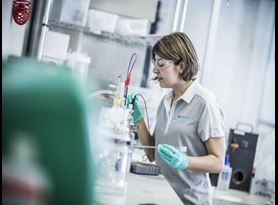
Electrochemical Corrosion Testing
Element provides electrochemical corrosion testing using Electrochemical Impedance Spectroscopy, cyclic potentiodynamic polarization measurements and galvanic corrosion measurements.
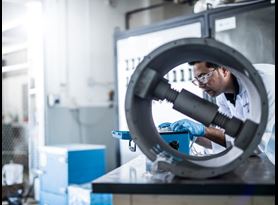
Sour Service Corrosion Testing
Element is one of a few ISO certified sour service labs in the world, providing sour service corrosion services for a variety of test types including NACE MR0175/ISO 15156.