With the ever-increasing demands to reduce material costs (i.e., installation, operation, and maintenance), composites are becoming more relevant for a variety of industries. This is due to their high strength to weight ratio, corrosion resistance, and impressive fatigue performance. As the use of these materials expands, so does the need to test the environmental effects on composites in their intended settings.
Environmental Impact on Composite Materials
The properties of composite materials may change as the materials are exposed to environmental factors.These include moisture, thermal cycling, fluid exposure, and sunlight and UV.Element hasa broad range of capabilities to simulate those factors so you can understand how your material will perform throughout life.
Polymer based composites absorb moisture from the air in regular service. This moisture can plasticize the polymer chains, resulting in a lower glass transition temperature (Tg), and degrade mechanical properties. The diffusion of the moisture is slow at operating temperatures, so moisture ingress can be accelerated by exposure to high temperature and humidity for characterization purposes. ASTM D5229 provides standardized methodology for moisture conditioning of composite test specimens. Specimens are generally exposed to high temperature and high humidity in a humidity chamber. Representative travelers are conditioned at the same time in the same chamber. These travelers are carefully weighed at regular intervals. When the travelers show no additional weight gain, specimens have reached moisture equilibrium. These specimens will be removed from the chamber and tested.
Thermal Cycling of Composites
In some applications, composites may experience thermal cycling. Under some circumstances these temperature changes can cause microcracking of the polymer matrix and loss of mechanical properties. Element maintains a variety of thermal shock and thermal cycling chamber to simulate end uses.
Composites have started to replace metals in Oil and Gas industry applications, especially in deep water corrosive environments, and in aircraft load bearing and non-load bearing structures. These components are in contact with different types of fluids in the service environment, which can affect their long-term mechanical integrity.
Fluid effects on composite materials
By exposing materials in service fluids in the laboratory, we can quantify environmental effects on composites’ mechanical integrity. Long term performance can be evaluated by accelerating the rate of chemical change, usually by increasing temperature.
To perform this testing, composite samples are exposed to fluids (single phase or multi-phase) in a pressure vessel, as defined by the service environment of the final part. The temperature and pressure of the vessel are increased to accelerate the physical and chemical aging. Testing the environmental effects on composites involves selecting specific conditions relative to the in-service environment, and how that effects the mechanical and physical properties of the material over the expected service lifetime of the component.
By choosing the right pressure and temperature, the physical and mechanical degradation of the composite over 25 years in service can be simulated in a laboratory and then measured with relevant mechanical testing methods.
Composite testing at Element
Our composite material experts have a large range of experience testing composite material samples. Element has the capability of running exposure for any type of liquid or gas required by our clients, including pure H2S, supercritical CO2, and seawater. We offer a complete suite of mechanical and physical testing to evaluate the effect of the exposure, including but not limited to: tensile, compression, shear, flexure, DSC, TGA, thermal conductivity, and more.
For more information about our composite testing services or to request a quote, contact us today.
Related Services

Mechanical Testing of Composite Materials
Element’s global network of composite testing laboratories offers an array of mechanical testing services, including compression, shear, tensile, and fatigue.
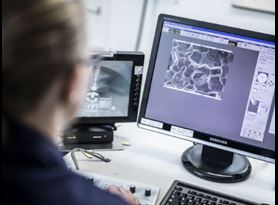
Composite Material Testing
Element’s composite raw material testing helps manufacturers understand the physical, thermal, and mechanical properties of the constituents used to create their composite product.
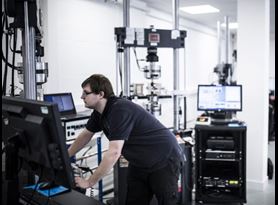
Composite Fatigue Testing
Whether testing to a specific standard or developing a custom program, Element’s experts are ready to assist with your composite fatigue testing needs.
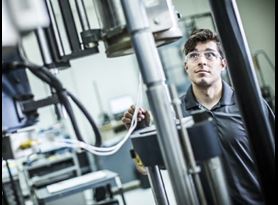
Shear Testing of Composites
Our composite testing experts provide shear testing methods including interlaminar, in-plane, and v-notch to measure the shear properties of your material.