EMC Principles for Electronics Product Design

By Engaged Expert
Steve HayesSteve Hayes has over 30 years of experience in the product approvals industry and serves on numerous national and international standards committees.
From research and development to final certification, electromagnetic compatibility (EMC) principles should be a key focus of electronics product design. In addition to ensuring product safety and wireless coexistence, considering EMC principles in the early stages helps smooth the path to compliance and prevents costs and time associated with redesign.
EMC Principles made easy
Electromagnetic Compliance (EMC) is often described as a ‘Black Art’ but the key to unlocking it is understanding its basic principles. Once these EMC principles have been learned, EMC can suddenly appear much simpler. It's important to understand the difference between EMI vs EMC.
EMC electromagnetic interference basics
When a product is being designed – be it a physical product or a system – it is important to ask what needs to be considered to ensure EMC is achieved. To do this, it is essential to take a step back to basics and consider how EMC interference is generated.
In the simplest of terms, interference is caused by moving from one state of energy to another. As with the flick of a light switch, we expect this transfer of energy to be instantaneous.
EMC regulations, from commercial to medical to military, are essentially all asking how to stop the voltage overshoot or undershoot during energy transfer so that a product can function without interference.
EMC Principles - Asking the right questions
It is the probability of such interference which must be identified. No matter how much electromagnetic noise is generated, it must be remembered that there has to be someone or something receiving that noise for interference to occur. The key questions which must be asked are:
- Where is this product going to be used?
- With what/whom is it going to interfere?
- How will the energy travel from the product to its “victim”
- Energy will travel either down the cabling or through the air, the two mechanisms, therefore, being radiation and conduction. Standards used are based around radiated and conducted tests.
EMC coupling
There are mechanisms of which to be aware, such as capacitive coupling and induction. These are more unusual, even though induction is predicted to increase in significance as new technologies, such as wireless charging of electric cars and appliances, continue to emerge and become more widely adopted, the potential interference that they cause is limited.
“With our experience getting thousands of products successfully through final compliance and certification, we have identified the three most essential elements of EMC on product design: filtering, shielding, and earthing/grounding.”
Steve Hayes
Technical Director, Connected Technologies
Three considerations in EMC for product designers
Take three key factors into account.
Whether it is a product, a system, or a printed circuit board, the basic EMC principles remain the same. When considering how the design of the product could ensure greater electromagnetic compatibility, there are three key factors to consider:
- Shielding
- Grounding/Earthing
- Filtering
EMC shielding
Depending on a product’s function, some devices produce unwanted electrical noise. The best way to prevent this noise from spreading to other, more effective radiators (such as cables) is to create a containment strategy.
A screening can (which is only solder fixed at each corner) may not be sufficient and having a weld along the full length of the folds is critical to ensure metal-to-metal contact, so a slot antenna is not inadvertently produced.
If shielding is used, then ensuring a complete Faraday Cage is important. Holes for cabling, monitors, and ventilation will affect the integrity of the shield, so EMC honeycomb mesh and screened cables or metal-to-metal contact will help with a 360-degree termination of enclosures for shielding. Thicker shield material will attenuate better by either reflection and/or absorption.
EMC grounding/earthing techniques
Earthing or grounding is the treatment of ‘potential differences.’
Grounding example: In the event of an electrostatic discharge (ESD), a voltage exposed to a product is simply trying to find the quickest route to the ground. If an ESD event is applied to a cable, and that same cable is directly connected to a PCB, the energy will travel along the cable and cause the ground plane on the PCB to jump up to the potential of the ESD level, potentially causing damage or malfunction. If that same cable was terminated on the board where the earth/ground connects to the mains entry point, the issue would be resolved.
Earthing/grounding can be achieved through various methods which can include:
- Flexible wires
- Flexible braid
- Metal plating
Flexible ground straps can be more usable, but this comes at the expense of effectiveness.
EMC filters and filtering
Filters are typically passive components that suppress RF noise and can be used internally on PCBs or externally on cables. The amount of electrical noise a product emits is not important; it needs to be connected to an antenna (i.e. cables, pcb track, etc.) for it to radiate or receive and cause issues. Consequently, all signal lines, especially those connected to the outside world, should be given specific treatment. This means filtering either at the point of source (emissions) or the point of entry (susceptibility).
There are various methods of filtering, which include:
- Capacitor or inductor components
- A small amount of capacitance from signal to ground
- Ferrite beads act as an inductor on whole signal/cables bundles
Filters can be a simple retrofit installation but can be expensive if required to be added to a significant production run. Different materials have different properties concerning frequency, and the manufacturer's literature helps you to select the most effective material for the frequency range. Design improvements during the product and pre-testing stage can reduce reliance on filters.
“By testing during the design phase, most of the potential issues and failures found in compliance testing can be mitigated.”
Steve Hayes
Technical Director, Connected Technologies
Cost-effective electronic prototype design
Qualify the prototype design early
The most cost-effective approach to product development will always be to qualify the prototype design early in the development cycle.
A key target should be to achieve success the first time at the testing, approvals, and certification phase. If a product has to be re-designed it can be prohibitively expensive, resulting in delays to market and a loss in consumer confidence.
Consider which countries your product will be exported to
While many countries have adopted regulations almost identical to CE marking, once a product is to be exported, it is much more likely that mandatory third-party testing will also be required to gain global market access.
It is vital to consider where the product may be exported to as early as possible in the design process, taking advice if necessary. Modifying a product later to meet unforeseen export requirements can be a costly and time-consuming exercise, a mistake seen often.
CE Marking has been a legal requirement for over twenty years, yet thousands of products still fail every year through incorrect CE marking.
Our EMC experts are here to help
Test houses such as Element, are asked to provide guidance and advice on EMC compliance, be it at the beginning or the end of the design process. By giving early advice we can prevent issues from arising later, a safer and more cost-effective option.
For more information on our EMI / EMC testing services, please contact our experts today.
Find related Resources
More from Element
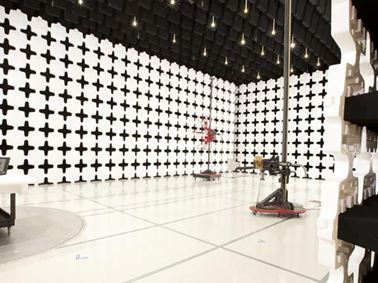
EMC Testing Services
Find out how Element delivers electromagnetic compatibility testing (EMC) solutions to RTCA/DO-160, MIL-STD-461 and Def-Stan 59-411 standards.

Are you ready for EMC Testing?
Element’s team of EMC Engaged Experts have therefore put together the following 8 point checklist and EMC test plan, to help ensure that you are fully prepared to present a device for EMC testing.
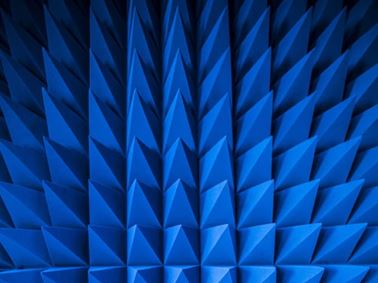
EMI vs EMC Testing
What's the difference? While these tests might be closely related, it is important to understand that EMC and EMI are not the same thing.
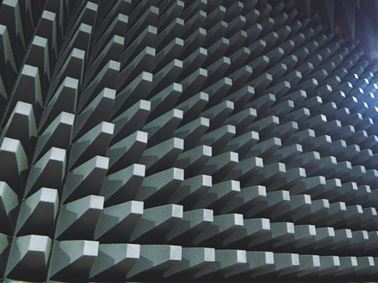
EMC Risk Assessments
EMC risk assessments are a combination of analysis & evaluation of potential EM hazards associated with the product & environment. Read our free guide.