AC 20-135: Understanding Fire Protection Test Methods, Standards, and Criteria
A guide to understanding the AC 20-135 fire testing standard, including when to use it, material covered in change 1, and its use in key aerospace standards.
What is AC 20-135?
AC 20-135 was issued in 1990 by the Federal Aviation Administration (FAA) as a reference for fire protection regulation. AC 20-135 Powerplant Installation and Propulsion System Component Fire Protection Test Methods, Standards, and Criteria is an advisory circular that guides manufacturers on demonstrating compliance with the powerplant fire protection requirements of the Federal Aviation Regulations (FAR). Many international aviation standards reference AC 20-135 fire protection regulation, including RTCA DO-160 and ISO 2685.
The AC 20-135 document includes methods for fire testing of materials and components used in propulsion engines, APU installations, and areas adjacent to designated fire zones, as well as the method rationale.
Manufacturers of aerospace systems, subsystems, and components must be able to demonstrate that the products continue to operate as intended when exposed to fire, with fire testing a vital prerequisite to airworthiness.
AC 20-135 is currently undergoing a full review by SAE, and the SAE 22 working group expects to present a revised standard in 2021.
Testing methods for fire resistance and fireproofing according to AC 20-135
The primary objectives of fireproof and fire-resistant materials and components are to contain and isolate a fire, prevent other sources of fuel or air from feeding the existing fire, and ensure components of the engine control system function effectively to permit a safe shutdown of the engine or APU.
Fire testing according to the current version of AC 20-135 requires the component or system under test to be exposed to a 2000-degree Fahrenheit minimum average flame temperature. Test times range from five minutes for fire resistance to 15 minutes for fireproofing.
Fireproof
A fireproof material or component must withstand a 2000°F flame (±150°F) for 15 minutes minimum while still fulfilling its design purpose and perform as well as or better than steel. When applied to materials and parts used to confine fires within designated fire zones, “fireproof” means that the material or part performs under conditions likely to occur in such zones and withstands a 2000°F flame (±150°F) for 15 minutes minimum.
Fire-resistant
When applied to powerplant installations such as fluid-carrying lines, flammable fluid system components, wiring, air ducts, fittings, and powerplant controls, ‘fire resistant’ material can perform its intended functions under heat and other conditions likely to occur at the particular location. Items under test must withstand a 2000°F flame (±150°F) for 5 minutes minimum.
A thermocouple rake and a calorimeter calibrate the flame. Component or system operation is facilitated hydraulically, pneumatically, or mechanically. In some cases, adding a physical load can simulate what would happen on the installed platform.
AC 20-135 change 1 – kerosene burner testing
Only kerosene burners should be used for fire resistance or fireproofing testing under AC 20-135. AC 20-135 change 1 (1990) re-evaluated the use of propane burners, as propane does not represent any combustible fluid likely to exist in an engine.
Kerosene burns at a higher intensity than propane; testing with a propane burner may result in a less severe test than a kerosene burner using representative combustible fluids.
AC 20-135 and ISO 2685
AC 20-135 and ISO 2685 are closely linked standards that cover similar environments in aircraft. ISO 2685 ‘Aircraft – Environmental test procedure for airborne equipment — Resistance to fire in designated fire zones’ specifies the test conditions applied to all components, equipment, and structures located in zones designated as ‘fire zones.’
ISO 2685 defines a ‘designated fire zone’ as a “region of an aircraft, for example, compartments containing main engines and auxiliary power units, designated as such by the aircraft designer in accordance with the requirements of the approving authority.” Components, equipment, and structures located in fire zones must satisfy the minimum specified level for resistance to fire.
Once the updated AC 20-135 is approved, it is expected that ISO 2685 will closely follow any amendments. Other committees will also take the guidance and apply it to relevant documents, impacting standards such as the aerospace specific standard for fire testing hoses, AS 1055.
AC 20-135 and RTCA DO-160 certification
AC 20-135 methods for fire testing of materials and components form one of the fire protection tests required for RTCA-DO-160 certification.
Understanding the requirements of AC 20-135 can play an essential role in the development of new components or systems either at the proof of concept stage or when determining confidence before RTCA D0-160 certification testing.
Key considerations when preparing for AC 20-135 fire testing
It is vital to take the following considerations into account to minimize the chances of test failure:
- The target area for the official flame thermocouple
- What defines the “worst-case operation” for use during the test
- If the test is to be run with or without vibration
- If there is any structural load to be applied
- If there are any unique failure criteria to be considered
- How the unit is secured for the test
- If portions of the unit should be insulated from the direct flame
It is not uncommon to run fire tests three to five times before the design is mature and can pass the test. Each failure provides vital information on how to improve the design to prepare for the next iteration of testing. Improvements could be through the redesign of the unit, a change to the operational conditions, or, if necessary, the addition of shielding.
AC 20-135 revision scheduled for late 2020, or early 2021
AC 20-135 has not received a significant update since its publication in 1990. Apart from AC 20-135 change 1, its fire testing guidelines have remained mostly unchanged for nearly 30 years. In 2017, the FAA asked standards development organization SAE to form a committee, the SAE A22 working group, to re-examine AC 20-135 and modernize it where necessary. The new specification is tentatively designated SAE AS6826 and will likely consist of a top-level document and four subsections.
- Powerplant Fire Test Standard Top-Level and Scope
- Powerplant Fire Test Standard Flame and Fire Test Guidelines
- Powerplant Fire Test Temperature and Heat Flux Calibration
- Powerplant Fire Test Pass/Fail Criteria
- Powerplant Fire Test Boundary Conditions
Element participates on the SAE 22 committee, meeting twice a year along with other leading industry experts to create the new document. The revised standard is scheduled to be out for approval in late 2020, or early 2021.
When the updated AC 20-135 document becomes available, it is expected that there will be some changes to how fire testing must be carried out in the future. Definitions and guidelines will most likely become much more comprehensive, including more details regarding flame calibration and the criteria used to develop operational boundary conditions.
Developing best practices in aerospace fire testing
Element is committed to developing and implementing best practices for fire testing. Our automated multiple cell fire test facilities offer the most comprehensive capacity from an independent testing house in the United States. Our fire test facilities are fully outfitted with the infrastructure to provide heated fuel, oil, or airflow, mechanical operation, including high-speed drives. Our experts work with state-of-the-art robotics to ensure the critical fire and operational conditions precisely meet all of the specification test requirements with high-speed videos recording multiple views of the test so they can carefully re-examine any failures. For more information on fire testing and AC 20-135, please contact an Element expert.
Building Product Testing Services
Find related Resources
Related Services
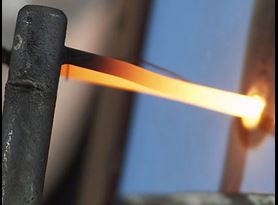
Reaction To Fire
Find out how Element's reaction to fire testing services help to provide a competitive advantage by demonstrating the product’s superior reaction-to-fire qualities.
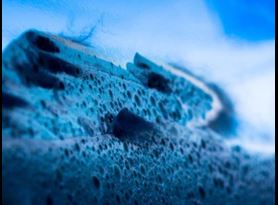
Bespoke Fire Testing
Find out how to develop an appropriate bespoke fire testing method to provide the information that you need.
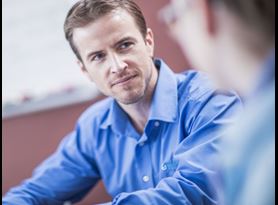
Flame Resistance and Fire Proof Testing
Element conducts fire testing and fire-resistance testing to ISO, NEBS, SAE, FAA and Roll-Royce standards. Our engaged experts experts frequently test critical aircraft components and components mounted in engine compartments.
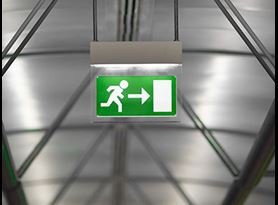
Fire Risk Assessment
Find out more about our third party accredited fire risk assessment experts and how they can help you comply with fire safety regulations and legislation.