With extensive experience, a wide range of tests, and labs conveniently located in global aerospace hubs, Element's experts simplify your RTCA DO-160 testing process. We tailor solutions to your specific needs, ensuring efficiency and peace of mind so you can go to market with confidence.
What is RTCA DO-160?
RTCA DO-160, the "Environmental Conditions and Test Procedures for Airborne Equipment," is vital for the global aviation industry. The latest DO-160G standard ensures the safety and reliability of airborne electronic equipment and mechanical systems. Tailored to meet Federal Aviation Administration (FAA) and global aviation regulations, it's universally adopted by aircraft manufacturers. This standard guarantees your electronic systems and components work safely in diverse conditions, prioritizing passenger safety and ensuring confidence in the reliability of your electronic systems and components.
Key benefits of RTCA DO-160 testing
- Stay Compliant with Regulations: With Element's tailored RTCA DO-160 testing, you’ll meet the rigorous requirements set by aviation authorities like the FAA, ensuring you're always in line with regulations.
- Enhance Safety and Reliability: Our testing validates your product's resilience in diverse conditions, from extreme temperatures to vibrations and EMI, ensuring its reliability and safety in real-world scenarios.
- Boost Quality and Trust: Our rigorous testing not only assures build quality but also fosters trust among your customers. It's concrete evidence of your commitment to best practices, enhancing your market position.
- Mitigate Risks: By adhering to comprehensive testing and making necessary adjustments, you can proactively address potential risks that may arise during your product's lifecycle.
- Streamlined Testing: Element offers all RTCA DO-160 tests in one place, utilizing cutting-edge equipment and concurrent testing setups. This means faster setup, smoother witness testing, and quicker results, helping you reduce time to market and minimize errors.
- Expand Market Reach: As a recognized international testing provider, Element opens doors to multiple markets for your product. Explore our global market access opportunities.
- Uphold Industry Best Practices: DO-160 is a cornerstone of environmental testing in aviation. Following these industry best practices is vital in avionics design and manufacturing.
Easily navigate complex testing procedures
When it comes to RTCA DO-160 testing, navigating the complexities can be overwhelming. Element is here to help - our dedicated experts are actively involved in RTCA Special Committee 135, ensuring you're always up to date with the latest standards. We provide solutions for even the toughest technical challenges, working closely with you to design a specialized test program that efficiently meets all your needs, no matter the scale. With more than a century of experience, we handle everything from full-size airframe testing to comprehensive operational and performance testing. Trust us to simplify DO-160 testing and guide you toward success.
Achieve a lifetime of compliance
We recognize that achieving RTCA DO-160 compliance is more than a one-time task; it's a lifelong commitment to safety and quality. Our dedication goes beyond initial testing, ensuring your product's compliance throughout its lifespan. We offer comprehensive support and monitoring to navigate evolving standards and regulations. Our expertise ensures that your product, whether an avionics system, airframe, or component, consistently meets RTCA DO-160's stringent requirements, aligning with FAA and relevant standards. With our guidance, your commitment to compliance remains steadfast, fostering long-term trust and confidence in your product's performance.
What RTCA D0-160 testing services does Element offer?
Our comprehensive range of RTCA DO-160 testing services include:
- Temperature and altitude testing
- Temperature variation testing
- Humidity testing
- Operational Shock and Crash Safety Testing
- Vibration Testing
- Explosive atmosphere testing
- Waterproofness Testing
- Fluids Susceptibility testing
- Sand and dust testing
- Fungus Resistance Testing
- Salt Fog Testing
- Magnetic Effect Testing
- Power input testing
- Voltage spike testing
- Audio frequency conducted susceptibility testing
- Induced Signal Susceptibility Testing
- Radio Frequency Susceptibility (radiated and conducted) testing
- Emission of radio frequency energy testing
- Lighting-induced transient susceptibility testing
- Lightning direct effect testing
- Icing testing
- Electrostatic discharge testing
- Fire, flammability testing
Why choose Element?
With a century of experience, Element is trusted by leading commercial aerospace companies, supply chains, and the top 25 OEMs for RTCA DO-160 testing. Plus, with over a decade of experience in ITAR/EAR jobs, Element North America and its subsidiaries is a trusted supplier to US government prime contractors. Element Materials Technology North America is duly registered and able to handle CUI, ITAR, EAR and other similar engagements. Element Materials is fully committed to comply with all applicable FAR and DFARs regulations.
Our state-of-the-art labs provide accredited testing services, accommodating projects of any size. What makes us unique is our streamlined, single-location-per-project approach. We employ cutting-edge equipment and parallel test setups to expedite testing and ensure precise, high-quality results. This approach enhances witness testing accessibility and convenience.
Ultimately, our method accelerates time-to-market for your products, meeting critical deadlines while upholding the highest safety and performance standards for avionics equipment.
We've also incorporated capacity redundancies to minimize development cycle risks, strengthening your supply chain. To learn more about Element, visit our About Us page. For inquiries about our superior RTCA DO-160 testing services, reach out to us with your requirements today.
Key considerations for RTCA/DO-160G EMI testing
Why should you test to RTCA/DO-160G? What’s the difference between EMI and environmental testing requirements? How does RTCA/DO-160G compare to other standards? WATCH ON DEMANDHow to prepare for success: DO-160 environmental testing requirements
Download a free webinar on RTCA/DO-160 Environmental test requirements presented by Element's John Homan.
WATCH NOWMore from Element
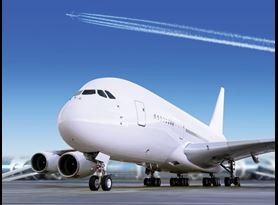
Our Services in Aerospace
Engaged in testing virtually every material, component and system on commercial aircraft, Element's deliverable is mission critical, certainty.
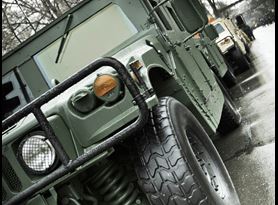
MIL-STD 810 Testing
Element's product testing labs in the US and UK evaluate components and systems to defense standards including MIL-STD 810 and others.
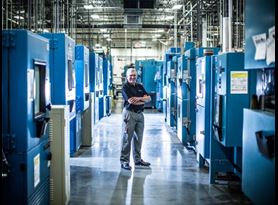
Environmental Testing
Element can provide you with critically important data on your product or part's performance in response to typical or extreme environmental stresses and conditions.
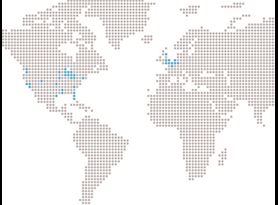
Element Locations
Learn more about our laboratories - where they are located; the unique capabilities they have and how they can help you solve your technical and commercial challenges.