Understanding the Importance of Fluid Systems Testing
Vehicles contain a variety of fluids that are critical to nearly every function. These specialized fluids create energy, provide cooling, generate hydraulic pressure, and much more.
Fluids in a vehicle are managed by “fluid systems,” which are generally composed of hoses, chambers, lines, pumps, and other components that store and move fluid throughout a vehicle. Like all vehicle components, fluid systems are subject to incredible stress throughout a vehicle’s lifetime, both from factors within the system such as pressure and from external factors such as road vibration and weather. Testing fluid systems is essential, as a failed fluid system can compromise an entire vehicle, endanger passengers, and harm the environment, but their complexity means that testing them requires specialized equipment and expertise.
Examples of vehicle fluid systems:
- Transmission lines
- Brake and vapor lines
- Fuel lines
- Air conditioning lines
- Heater hoses
- Radiator hoses
- Coolant hoses
- Intercooler hoses
- Power steering hoses
- Battery cooling hoses
- Battery trays and battery packs
- Radiators, transmission coolers, heater cores
- Washer bottles
- Air conditioning condensers and evaporators
How are Fluid Systems Tested?
Fluid systems testing uses laboratory processes to simulate the stress vehicle fluid systems would endure under real-world conditions. Technicians test different levels of fluid pressure, different temperatures of fluid and different environmental temperatures, different flow rates, and other factors. They can test variables independently or in various combinations, giving manufacturers detailed insight into the systems’ potential longevity, any design flaws, and how they will perform when in use.
Two common tests we perform at Element are high- and low-temperature testing and cyclic pressure testing. Our labs can condition fluids to temperatures as low as -40°C and as high as +150°C using environmental chambers, chillers and heaters, simulating extreme conditions systems may face while operating. Cyclic pressure testing applies liquid or air pressure at a cyclical rate (typically a specified amount of time on and time off) to help determine a product’s susceptibility to fatigue failure.
Element also has a fluid systems testing setup specifically for a process called accelerated radiator aging. In accelerated radiator aging, technicians run high-temperature coolant through radiators for an extended period of time, typically thousands of hours, to simulate years’ worth of fatigue. They monitor the performance of the radiator throughout, then conduct physical endurance tests on the “aged” radiator to understand how it may deteriorate and how it will perform. This can provide manufacturers with data on the long-term durability of the radiators and how they will perform after long periods of stress.
Other Fluid System Tests Performed at Element Labs:
- Leak testing
- Burst testing
- Vacuum testing
- Pressure proof and pressure decay testing
- Dynamic fatigue testing
- Static pressure testing, circulated pressure testing
- Impulse testing
- Pressure, vibration and temperature (PVT) testing
- Pressure, motion and temperature (PMT) testing
- Endurance, pressure, displacement and temperature (EPDT) testing
- Life cycle testing on vapor lines and brake lines
How can Element help?
Modern laboratory tests like those available at Element labs can simulate real-world conditions with a high degree of accuracy, even when multiple variables like extreme temperature and extreme pressure are at play simultaneously. This data helps manufacturers to design better products and supports customer safety. For more information about Element’s capabilities, locations, and the standards we test to, visit our fluid systems testing page or contact us.
Find related Resources
Learn more
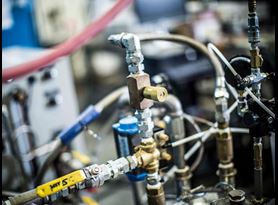
Fluids and Fuel Testing
Element performs fluids and fuel testing across a large spectrum of pressure, temperature, and flow to give you results closer to the real material behavior in the application.
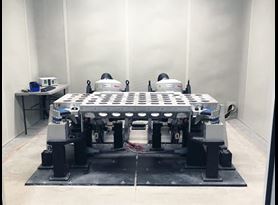
Automotive Buzz, Squeak & Rattle Testing
Element’s large multiaxial silent shaker can perform buzz, squeak, and rattle (BSR) testing with fast turnaround times on components up to 700lbs, to help manufacturers create quieter products.
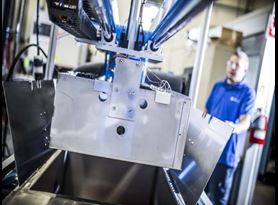
Hybrid & Electric Vehicle Battery Testing
We perform validation testing on Li-ion and Ni-MH battery cells, modules, ultracapacitors and packs to ensure the safety and performance of your products.
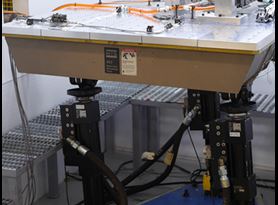
MAST Testing
Element provides multi-axial simulation table (MAST) testing for squeak and rattle, vibration, performance and durability testing of a broad range of vehicle components and assemblies.