Ensure your oil and gas pipelines and infrastructure assets are safe, compliant, and performing their best, with Element's cutting-edge corrosion testing solutions. We understand how critical it is to prevent leaks or material failures when working with high-risk fuels like oil and gas. As a recognized world leader in the provision of corrosion testing services for the Energy sector, we help you reduce material failure costs and meet your environmental and safety responsibilities.
Why is Corrosion Testing so Important for the Oil & Gas Sector?
Within the energy sector, it is vital to be confident in the integrity of pipelines and infrastructure - particularly when it comes to high-risk fuels like oil and gas. Gas leaks and oil spills can have catastrophic consequences, not only for the safety of the environment and people around them, but also for the reputation of those who supply the energy source. Corrosion testing helps assess that the materials and coatings selected for use in components that come into contact with oil and gas are fit for purpose, even in the harshest environments. It also helps to predict what factors could cause future failures to occur; and when. As continuous provision of oil and gas services are is relied upon to keep society functioning, preventing disruptions is crucial.
Benefits of Corrosion Testing for the Oil and Gas Industry
- Assure Pipeline Integrity: Corrosion testing helps reduce the chance of leaks and failures, ensuring your pipelines are verifiably reliable, even in harsh conditions
- Avoid Supply Chain Disruption: Identify potential failure risks before they occur, preventing disruption of energy supplies to your customers
- Improve ROI & Reduce Unplanned Costs: Improve your product’s lifespan and reduce costs associated with unplanned maintenance & downtime
- Accountability for Safety: Meet your regulatory compliance obligations and prioritize safety in your Oil and Gas operations, reducing risk for workers and the environment.
- Reduce Environmental Impact: Proactively reduce the likelihood of contributing to oil spills or gas leaks
- Informed R&D: Data from testing ensures you make informed decisions when selecting appropriate materials and coatings to use with oil and gas
- Access Innovative Test Methods: When you work with a world-leading corrosion testing partner like Element, you benefit from new and innovative methods, such as our SOHIC testing and Axial Full Ring testing, and Computational Fluid Dynamic modeling for data analysis.
Protect Your Reputation – As Well As Your Assets
For oil and gas suppliers and production line operators, having safe, reliable pipelines which can operate at the most efficient level is key to securing the trust and confidence of customers. Leaks, spillages, regulatory breaches, employee health scares, and disruption to energy supply chains can all significantly damage reputation. Through expert analysis and simulation exposure data, Element’s experts help you reduce corrosion risks in deep-sea pipelines and other critical infrastructure assets. With Element at your side, you can make certain of the longevity, safety, and compliance of your assets in oil and gas operations.
Predict Performance in the Harshest Environments
The oil and gas industry often operates in extreme environments, where the corrosion threat is greater. Element’s experts are specialists in simulation exposure and data analysis – helping you to predict how your pipeline and infrastructure components would respond in the harshest of conditions. We offer both non-sour and ‘sour’ corrosion testing (for reaction to substances that contain high thresholds of hydrogen sulfide (H2S) or sulfuric acid (H2SO4), ensuring you can verify the corrosion resilience of your products in a wide range of intended uses.
Corrosion Testing Services for the Oil & Gas Industry
- CUI (Corrosion Under Insulation) Prevention: Evaluating solutions using CUI inspection to mitigate corrosion under insulation, providing testing to verify performance following ISO19277:2018.
- Specializing in pipeline corrosion testing for “sour” and non-sour service applications such as Hydrogen Induced Cracking (HIC) or Sulfide Stress Cracking (SSC).
- Testing metallic and non-metallic materials.
- SOHIC testing.
- Axial Full Ring testing under longitudinal tensile load.
- Simulation exposure data analysis – including Computational Fluid Dynamic (CFD) modeling.
Why Choose Element?
Element’s specialized corrosion laboratories meet stringent international standards and protocols such as ASTM, NACE, and API. All Element locations performing corrosion testing are ISO/IEC 17025-accredited.
Combining industry experience with state-of-the-art laboratory testing and simulation facilities worldwide, we can simulate and evaluate the reaction of your materials under standard sour conditions or specific field conditions.
Trust in our global reach, expertise, and knowledge to ensure your assets are fully utilized for their optimum service life and safety in Oil and Gas operations.
To learn more about Element’s credentials, please visit our About Us page. For more information about our corrosion testing services, or to speak to our experts, contact us today.
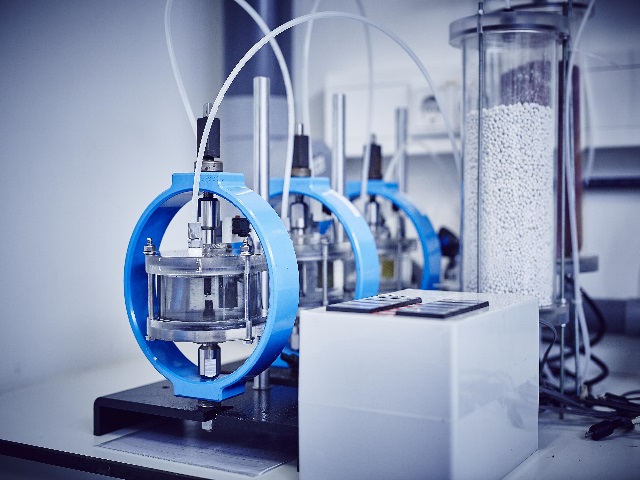
Corrosion and Materials Testing
Element provides a wide range of other ISO/IEC 17025-accredited corrosion testing services, to protect your assets, avoid failure and loss production, qualify welds, assess your materials, and improve safety.
Read MorePredicting component life with corrosion modeling
Erosion within oil and gas pipelines is a serious problem. Corrosion modeling using the Computational Fluid Dynamic method can accurately predict the location of burn-throughs.
Read MoreWebinar: Criticality of Failure Analysis in the Energy Industry
Element’s experts for Failure Analysis in the Energy industry explain during the on-demand webinar how Failure Analysis is being performed, and its benefits by providing real-life case studies from around the world.
Read MoreRelated Services
Element offers the most comprehensive range of corrosion testing services for the Oil & Gas sector.
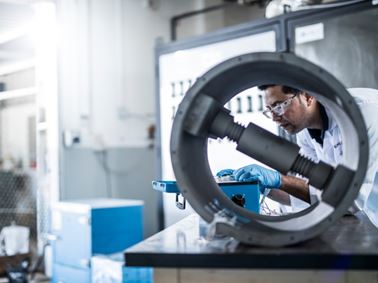
Sour Service Corrosion Testing
Element is one of a few ISO certified sour service labs in the world, providing sour service corrosion services for a variety of test types including NACE MR0175/ISO 15156.
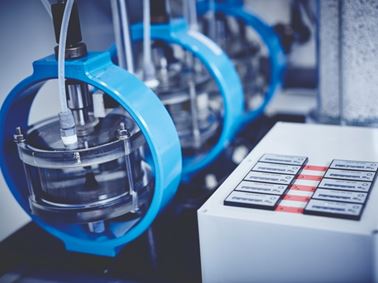
Sulfide Stress Cracking (SSC) Testing
Element's SSC (Sulfide Stress Cracking) testing according the NACE TM0177/ ISO 15156 standard helps ensure sour service pipelines’ reliability and longevity.
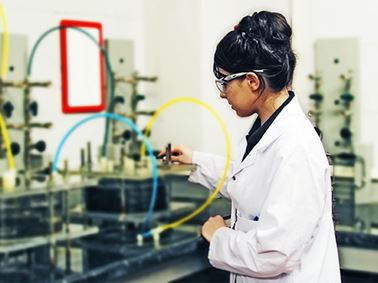
Hydrogen Induced Cracking (HIC) Testing
Element’s HIC tests evaluate material susceptibility to hydrogen induced cracking in a sour environment in accordance with NACE TM0284.
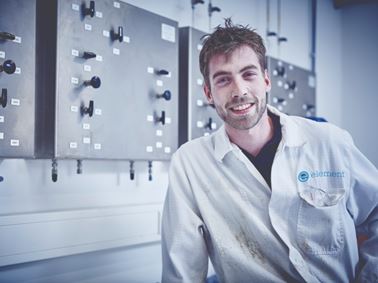
Hydrogen Embrittlement Testing
Element performs Hydrogen Embrittlement (HE) testing to ASTM F591, Galvanically Induced Hydrogen Stress Cracking (GHSC) to NACE MR0175/ISO 15156 and Hydrogen Induced Stress Cracking (HISC) testing.
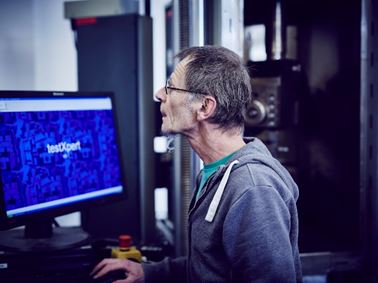
Corrosion Inhibitor Testing
Element’s corrosion inhibitor testing experts select the most suitable corrosion inhibitor to protect your assets and extend their life span within the energy industry.
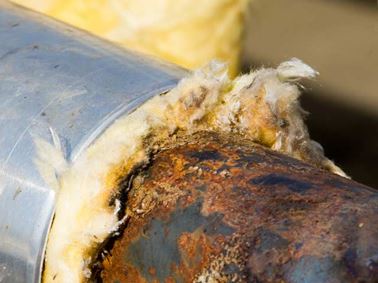
Corrosion Under Insulation (CUI) Testing
Element supports clients to assist in evaluating solutions to try and mitigate corrosion under insulation (CUI).
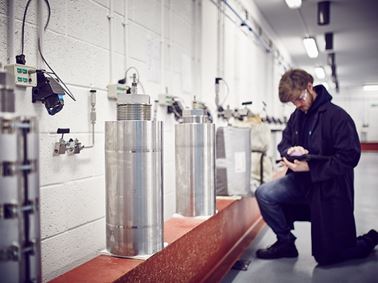
High Pressure High Temperature (HPHT) Testing
Element offers an advanced HPHT testing program for polymers, metals, coatings and components used in highly aggressive environments.
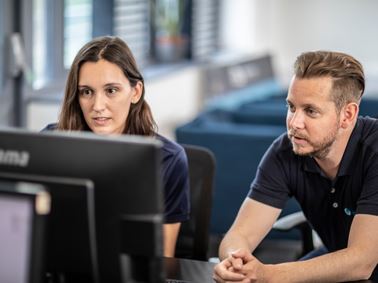
Computational Fluid Dynamics (CFD)
We use Computational Fluid Dynamics (CFD) to simulate and analyze complex problems involving fluid-fluid, fluid-solid, and fluid-gas interactions.