Helping to establish failure thresholds and service life limits, high cycle fatigue (HCF) testing is an integral part of our aerospace engine qualification programs. Our unique, world-class capabilities enable us to handle everything from small sub-components to the largest fan blades in service today.
High vibrations conditions of airfoils during operation can impact the structural integrity of a test specimen, which makes HCF testing indispensable. Individual metallic and future advanced material turbine blades or segments of a bladed disk are tested in the natural resonance frequency range until crack initiation. Our equipment allows us to run a very high number of cycles in a short amount of time, simulating a components' service life. Our HCF testing service portfolio also includes the ability to carry out strain gauge calibration on instrumented airfoils.
Performing High Cycle Fatigue Testing (HCF)
During HCF testing, individual turbine blades (or blade samples) are cycled at an extremely high rate to mimic their natural operating frequency. Once cracking starts to occur, the failure cycle count is recorded, and the product is analyzed for performance characteristics and durability criteria.
We understand the unique environments and challenges that airfoils and aerospace engine components face. To better support your testing program, we offer a range of options for high cycle fatigue testing, including testing at temperatures up to 1200 C, sample notching and machining services, fixture and clamp design, and specialist test methods.
High Cycle Fatigue Testing for Aerospace Engine Qualification
We support a range of high cycle fatigue test methods, including:
- Piezo-electric
- Electro-dynamic
- Constant Airjet
- Chopped Air
- Sonic Fatigue (Hot/Cold)
For more information about out high cycle fatigue testing programs, or to request a quote, contact us today.
Related Services
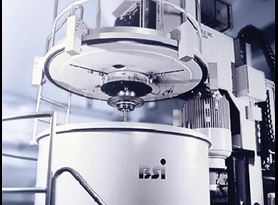
Spin Testing
Find out how Element tests all rotating components within aero engines to help make certain that they are safe and reliable when in-service.
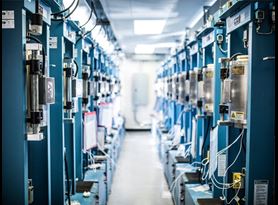
Aerospace Materials Testing
As the largest independent materials testing provider in the global Aerospace sector, Element is well-positioned to meet your every requirement, from early stage R&D development projects, materials testing for production through to solutions for in-service challenges.
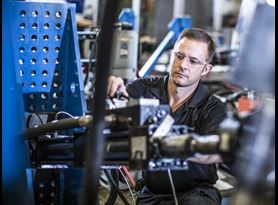
Dynamics Testing
In addition to vibration testing, Element provides a range of dynamics testing including acceleration, shock, drop, structural, fatigue and rotating load simulations.
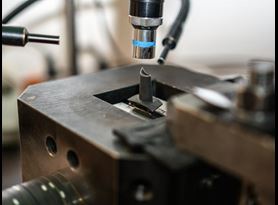
Airfoil Blades
Find out about Elements extensive range of High Cycle Fatigue (HCF) testing services for engine airfoils.