Materials operating in low-temperature service must retain suitable properties including elongation, yield, and tensile strength and ductility. Element offers a full range of mechanical testing services on advanced materials at cryogenic temperatures to ensure they perform as expected in these extreme conditions.
Different industry sectors are continually exploring new materials with better performing chemical properties and laboratories are challenged to develop new test methods on these demanding materials, which includes mechanical testing at cryogenic temperatures such as tensile testing, impact testing and fracture toughness. Cryogenic or very-low temperatures are in the range of 120 Kelvin (-153° Celsius/-243.4° Fahrenheit) and absolute zero (0 Kelvin/-273.15° Celsius/-459.67° Fahrenheit).
Cryogenic testing capabilities as low as 4 Kelvin
With one of the most comprehensive ranges of materials testing services, we have the experience and expertise in mechanical testing with the use of low cryogenic fluids in providing thermal environments as low as 4 Kelvin (-269 °C/-450 °F). Our state-of-the-art laboratories utilize the latest testing facilities and equipment to carry out cryogenic testing in Helium cooled down to as low as 4.7 Kelvin and in liquid nitrogen (LN2).
We can evaluate and test such materials as austenitic stainless steels, steel alloys, aluminum alloys, composites, and Al-Li alloys. Using our most advanced computer systems, we are able to monitor control rooms and equipment for seat leakage, temperature, oxygen, and pressure.
Low temperature testing for many industries
From specimen design and prototyping to test plan development and engineering analysis, Element delivers high quality, reliability, and optimum performance of materials operating in low temperatures to clients from the aerospace and the energy sector including oil & gas and hydrogen.
One example is the International Thermonuclear Experimental Reactor (ITER) project, where Element has provided mechanical testing services at cryogenic temperature to F4E parts producers for over nine years, including tensile, impact, shear, fracture mechanics, and fatigue growth testing.
Mechanical testing at cryogenic temperatures
As cryogenic testing operations create potentially hazardous test conditions, safety is of paramount importance at all times. Our highly skilled engineers utilize specialist testing areas equipped with the latest in safety protection to eliminate all hazards. We operate our stringent cryogenic testing programs in compliance with health and safety rules, regulations, and industry standards.
Our mechanical testing capabilities include:
- Mechanical Fracture Toughness at cryogenic temperatures
- Fatigue Testing at cryogenic temperatures
- Tensile Testing at cryogenic temperatures
- Charpy Impact Testing at cryogenic temperatures
- Fatigue Crack Growth Rate (FCGR)
- Surface Crack Tension (SCT)
Element also performs Fitness for Service (FFS) and Residual Life Assessments (RLA) to determine the safety and remaining life of equipment operating at low temperatures. Assessments and studies of this type are frequently used in the Oil & Gas, Power Generation, and Chemical Processing sectors, and on technological plants of hospitals, airports and infrastructures in general.
Why choose Element?
Our cryogenic testing services not only assure the high performance of your materials but also helps optimize costs, improve operational safety, and reduce environmental impact in even the most challenging operating conditions.
For more information about our cryogenic testing services or to request a quote, contact us today
Ready to request a quote?
Our deliverable is certainty - high quality data, test reports and certificates that you can absolutely rely on when making decisions about your materials and compliance. Engage with an expert today.
Material Behavior at Cryogenic Temperatures
The behavior of metallic materials under cryogenic temperature conditions differs significantly from their behavior at room temperature for the same type of test. Learn more about the effects of cryogenic temperatures on materials.
LEARN MOREWhat is Mechanical Testing and why is it Important throughout the Product Lifecycle?
Find out about what mechanical testing is and how it plays a key role in ensuring a cost-effective design as well as technological evolution and superiority.
Read MOREDo's and Dont's of Medical Device Mechanical Testing
Although mechanical testing is just one part of bringing a medical device to market, it is an important one. Understand how to get success the first time around when deciding on a mechanical testing partner.
READ MOREMore from Element

Mechanical & Destructive Testing
Element's mechanical tests are part of our destructive testing services, they show whether a material or part is suitable for its intended mechanical applications.

Temperature and Thermal Testing
Element can recreate the conditions your parts or products will face in actual use.
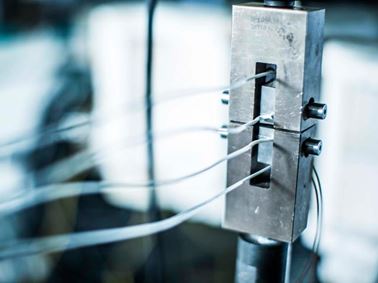
Fracture Toughness Testing
Element provides fracture toughness testing for determining material characteristics and longevity of metallic, nonmetallic, and advanced materials.
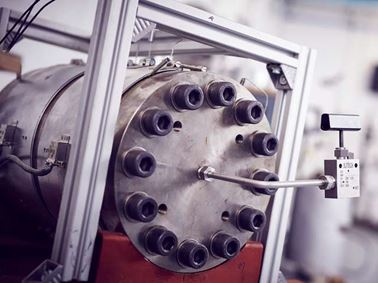
Hydrogen
Element has decades of experience in testing materials and components for their behavior in hydrogen-containing environments.