A Comparison of Random Vibration Testing Methods
Random vibration testing, sine-on-random testing, and narrow-band random-on-random testing all have their own strengths and benefits in regards to revealing design weaknesses of a product that might otherwise only be revealed later during transport or deployment and use.
By simulating the real-world environment that a product may encounter during its life cycle, a comprehensive vibration testing program can provide you with detailed accuracy on how robustly you need to engineer your product in order to avoid failures in service. This reduces the costly risk of product recall and enables you to achieve your product qualification milestones.
In order to perform a vibration test on a product’s future specific operating environment, it is important to not only understand the environment it will be required to perform in, but also how the different approaches to vibration testing might best simulate it.
Random vibration testing
Random vibration testing applies vibration energy at all frequencies over a specified frequency range. Random vibration is the most common type of validation and qualification test. The majority of mounted devices, including mechanical and electronic devices, will usually experience random vibration conditions in their operating environments.
Sine-on-random vibration testing
Sine-on-random (SOR) vibration testing applies single or multiple sine frequencies on a random profile. In a swept sine test, a vibration sine tone is swept up and down through a range of frequencies at a specific rate and duration upon a random profile.
Sine-on-random vibration testing is particularly useful when the product’s application environment includes rotating or reciprocating equipment like turbines, engines, motors, and propellers. When used early in the design process, sine-on-random vibration testing can be a powerful tool to help reduce the probability of fatigue failure.
Narrowband random-on-random testing
Narrowband random-on-random (ROR) vibration testing simulates real-world complex vibration environments with a combination of a broadband random signal and one or more superimposed random narrow bands. Both signal types are usually present simultaneously and the narrow bands can appear at fixed frequencies or be swept over a predefined range.
Narrowband random-on-random testing is particularly applicable for product qualification and fatigue tests. A typical example is the repetitive stress on a vehicle’s headlights, as the vehicle changes speed while traveling on rough terrain. ROR is often the most appropriate type of vibration testing for caterpillar-tracked vehicles, such as bulldozers and tanks, and machines with rotating components, such as propeller-driven aircraft that do not operate at fixed frequencies.
Mitigate risk from the start
By working with a testing company who has an expert understanding of the environment in which you are looking to operate, you can reduce the risk of product failure early on in the design stage. We can achieve this in many ways, including computer simulation (Finite Element Analysis) during the design phase, and engagement with Element’s Early Stage Qualification (ESQ®) team to ensure that the optimum vibration testing conditions are selected. Commercial, Military, and Aerospace standards we commonly test to include RTCA DO-160, MIL-STD 810, DEF STAN 00-35, and BS EN 60068, and can take care of your complete testing process to meet unique, bespoke, or complex project requirements.
To learn more about the different types of vibration testing suitable for your product including combinations of temperature, humidity, and altitude extremes and unique corrosive, explosive or harmful environments, please contact us or call UK +44 808 234 1667 or US +1 888 786 7555.
Find related Resources
More from Element
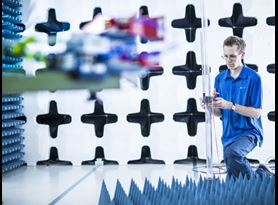
Commercial EMC Testing
At Element, we test thousands of products every year, having one of the largest capacities for electromagnetic (EMC) testing of commercial and industrial electronic devices.
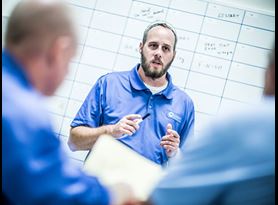
CE Marking and Testing
CE marking is a mandatory conformity mark enabling you to enjoy free movement between all 28 Member states.
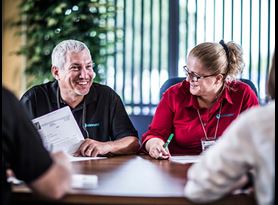
Advisory Services
Our team of Engaged Experts can help you understand the various regulatory requirements and reduce the test burden by comparing the various standards and producing compliance strategies that fulfill the brief of ‘test once, approve to many’.
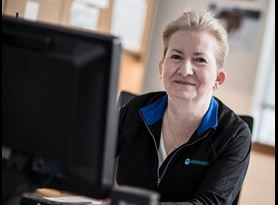
Global Approvals
Element can serve as your single point of contact for all of your global product approvals.