How to Prepare for Radio Compliance Testing?
As the use of radio devices grows, it is now more crucial than ever for manufacturers to conduct compliance testing to prove that their products meet the necessary requirements before they can be sold on the market.
What is radio compliance testing?
Radio compliance testing is the process of ensuring that radio products meet the necessary regulatory requirements, rules, and standards that apply to the countries where they will be sold. This testing can be a complex and daunting process, especially for those unfamiliar with the intricacies of radio technology and regulations.
In this article, we will discuss some of the key considerations for manufacturers preparing for radio compliance testing, including sample preparation, the types of testing required, and using pre-approved modules. By understanding these requirements, manufacturers can help ensure that their products meet the necessary regulatory standards and reach their intended markets on time.
Prepare the sample for testing
The first step is to ensure the sample is fully ready for testing. When preparing a sample, it is useful to know the common modes that will most likely be required to put the device in to facilitate the testing. This will then enable you to consider any issues that may arise with each mode, such as:
Channel
Will the channels need to be changed?
Modulation scheme
Will the modulation scheme need to be changed? For example, from QPSK to 16QAM
Signal bandwidth
Have the signal bandwidths been agreed, for example 5, 10, 20, 40, 160 megahertz
Carrier power (if tuning is required)
Does there need to be the ability to change carrier power? It may be possible to test channels in the middle of the band at full power, but at the edges of the band some of these tests may be difficult to pass when the transmitters are on full power and may require turning the wick down at the edges of the bands.
Signal type
Will it be necessary to remove modulation and just have a continuous wave to help with the testing?
Receive only mode / digital device if supported
Does the device have a receive only mode or a mode where you completely disable the radio?
Number of ports/antennas
Does the device supportmultiple antennas/ports? Are all antenna ports accessible for testing?
It’s also worth considering the instructions and the interface when preparing a sample for testing. It’s not unusual for a product to arrive at Element’s test laboratories to find that there are no, or only very basic, instructions. To prevent delays, comprehensive instructions on how to set up and configure the unit for testing should be prepared and readily available.
Regarding the interface, which should preferably be removable for the test, commands are typed in and sent down a serial cable to the device to set up in a particular mode. It is important to make sure that the cable can be disconnected if necessary.
Consider the type of sample required
The type of sample that will be required should also be considered in advance of testing. For Wi-Fi testing, when much of the tests will be conducted rather than radiated tests, a 50 ohm connection on the unit will be required. This means providing samples with a temporary antenna port soldered on where the antenna would have been. A normal sample, with a built-in antenna already installed, will also be necessary for any radiated emissions testing.
Some tests may require extremes of testing. This could be extremes of temperature or extremes of supply voltage. If it's a battery powered device being tested, a connection to a bench power supply may be needed to enable the voltage to be varied. If it's a mains device, standards will usually say to test within + or -15% of the nominal value of the mains voltage. For voltage extremes, if it's a USB device, then the extremes given by the standard will usually also be the extremes of the USB.
In terms of additional equipment, consider if an adapter will need to be supplied for testing. Element has had instances where the product manufacturer has presumed AC conduct and emissions won’t be applicable because their device is DC powered, with a DC power port on the side rather than batteries. However, if an adapter is not supplied with the device, ANSI advises the testing house to take an adapter off the shelf to carry out AC mains testing. A device is not exempt because it only has a DC power port.
Using pre-approved modules
When using pre-approved modules, the module manufacturer’s integration instructions should be followed carefully. When using pre-approved or pre-certified modules, the module manufacturer should provide a set of comprehensive integration instructions. These need to be read and followed to the letter to ensure that the final product fully complies. This is especially true with power supply and the antenna type and gain, although if the device has a module with a built-in antenna, then it will not be an issue.
You also need to consider how the conducted RF testing can typically be inherited from the module. This is why the module integration of even the pre-approval module really helps.
Using pre-approved modules will mean that you need to ensure access to the test mode interface. If the module has been brought in, it’s vital to remember that the test laboratory will need to gain access to the test mode or device test mode interface. If the manufacturer hasn’t designed it themselves, they will need to ask the module manufacturer how it is put into test mode. If it's specific software that the module manufacturer doesn't want to release to the customer, it should be possible for the laboratory to get it under NDA, but this can take time and cause delays. If it needs a special interface, like a serial interface, ensure that it is available on the end product so it can be connected to for testing.
When integrating a cellular module, Element can control the device under test, including RAT, frequency, and level, by a communication test set. The test equipment can control any radio access technology and enable the device under test to switch between modes. For example, it can switch between GSM mode, 3G mode, LTE mode, then go into narrowband IOT mode, or MTC mode for LTE. However, the manufacturer needs to be aware that a soldered down SIM should be a special test SIM and a software SIM needs to have the test mode profile enabled.
For 2.4 GHz Wi-Fi, it is important to note that, for FCC authorisation, the radiated restricted band edge limits (2483.5 -2500 MHz) may require that the output power is reduced at the channel edges. You therefore need to be aware that a lot of time can be spent carrying out power tuning for Wi-Fi.
Intermodulation
Intermodulation is the amplitude modulation of signals containing two or more different frequencies, caused by nonlinearities or time variance in a system. This can happen when integrating two pre-approved modules. The two signals can potentially radiate into each other's antenna and any nonlinearities can cause intermodulation products.
If, during normal operation, two individual transmitters can operate at the same time then it needs to be ensured that any intermodulation products are within the limit. For example, a cellular radio transmitting at 900 MHz and a Zigbee device transmitting at 2405 MHz could produce intermodulation products at 1505 MHz, 3305 MHz, 4205 MHz and so on.
Element also frequently sees issues during testing where there is a single transmitter, but the antenna is a poor match and that will also cause intermodulation products.
Chipset versus module implementation
When designing a radio product, one of the first points to consider is if it should be designed as a chipset or a module. Both chipsets and module implementations have their advantages and disadvantages for radio products and their manufacturers.
Chipsets tend to mean a lower cost per device as they have a lower component cost. However, they will have an increased design cost and increased certification cost. Chipsets provide the manufacturer with the ability to retain control but can result in an additional quality burden.
Modules tend to have a high component cost but a reduced design cost. The inherited testing also means a reduced certification cost. However, the manufacturer must accept that a third party has control and will therefore have to rely on the third party for maintaining quality.
Ultimately, the decision of chipset versus module usually comes down to scale of production. If the production numbers are not expected to be that vast then the module is usually the more popular choice but if the quantity is going to be sizeable, then a chipset tends to be the preferred option.
Avoiding the common pitfalls
Element often finds a manufacturer has booked a laboratory and scheduled the testing on a certain day to discover it can't start because the sample is not ready. So, what stops the laboratory from performing the testing?
Some of the most common reasons testing gets delayed include:
- Test modes – the customer does not realize that test modes are required. Make sure you check in advance of testing if you have got the test modes there
- The test mode has not been checked prior to testing
- The test sample hasn’t been configured for continuous transmission. Samples need to transmit continuously to maximize the signal and if it's only transmitting for a brief amount of time, for example every 10 seconds, it will be impossible to test
- Support equipment has not been supplied.
How Element can help
Manufacturers with little RF experience may be more likely to experience issues with test modes, while those who design their own RF section may be less likely to have such issues. By being aware of these common pitfalls and taking steps to avoid them, manufacturers can ensure that their samples are ready for testing and avoid unnecessary delays in the testing process.
Element’s engineering team can support you throughout the entire radio testing process, from generating bespoke test plans and performing pre-compliance investigations through to full formal conformance testing. We aim to deliver fast and efficient solutions against complex product testing requirements, enabling you to demonstrate that your products will use the radio spectrum effectively and comply with country-specific regulatory requirements.
For more information on how Element can help you from R&D to reality please contact our smart experts
Find related Resources
More from Element
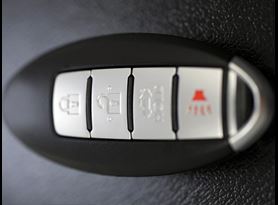
Radio Testing
We can help with EMC and safety testing and assist manufacturers who want to take their radio and wireless product to the global market
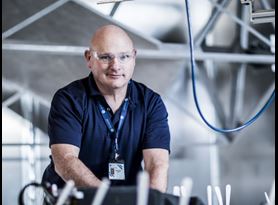
Wireless Coexistence Testing
Our wireless coexistence testing programs evaluate how wireless medical devices and other sensitive equipment interact and perform with other electrical and radio equipment.
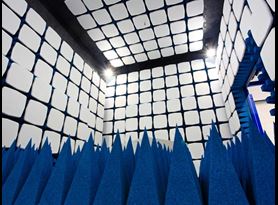
EMI EMC Testing
Element’s global EMI and EMC testing services include programs for aerospace, defense, medical devices and commercial products.
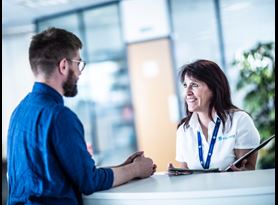
Regulatory Approval - The Radio Equipment Goal
In this article, we look at the authorization of radio equipment for some of the world’s main market regions.