Element is a leading provider of specialized real-time simulation and testing services to the global automotive industry. Our experts apply automotive simulation testing to components, systems, and full vehicles to provide the highest quality data to ensure the proper functionality of your products.
Real-time simulation provides valuable data for evaluating product life and identifying deficient areas in the design. Simulation also reduces test duration compared to proving ground durability schedules and is, therefore, a useful tool to accelerate time to market and minimize long-term costs.
Be it evaluating individual components, sub-systems, or full systems, Element’s engineers support you through the whole product development process, developing comprehensive test plans tailored to fit your specific needs. We have experience with steering, exhaust, interior, and suspension systems, and can perform corner module, half vehicle and full vehicle fixed reacted, or inertia reacted simulation tests.
Our real-time automotive simulation testing capabilities
Element’s team of simulation experts offer extensive real-time simulation testing capabilities that cover a broad range of motor vehicles, including passenger cars, light and heavy trucks, buses, off-highway equipment, and more.
We utilize innovative test equipment, including Multi-Axial Simulation Tables (MAST), 4-Post road simulators, single and multi-axial servo-hydraulic systems, custom-built bed plates, and spindle-coupled simulators (MTS 329 simulators). Our equipment allows us to test a broad range of vehicle components and systems, from chassis and suspensions to seats, interiors, cooling modules, axles, engines and powertrain systems.
We also offer real-time simulation for testing Buzz, Squeak, and Rattle (BSR) to determine the fit and wear of vehicle components as they are perceived acoustically.
To learn more about our real-time simulation testing, or to speak with one of our experts, contact us today.
More from Element
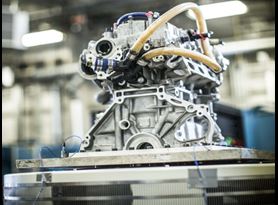
Vehicle Dynamics Testing
Element is at the forefront of vehicle dynamics testing, providing critical testing services to clients in the global automotive, defense, rail, aerospace, and transportation sectors.
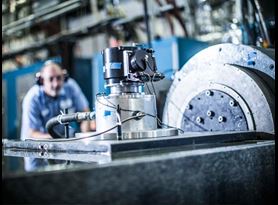
MAST Testing
Element is your partner in multi-axial simulation testing. Our Multi-Axial Simulation Table (MAST) is able to perform six degrees of freedom real time simulation in order to ensure your products are able to handle their end-use environments.
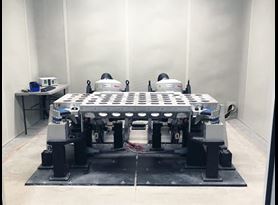
Automotive Buzz, Squeak & Rattle Testing
Element’s large multiaxial silent shaker can perform buzz, squeak, and rattle (BSR) testing with fast turnaround times on components up to 700lbs, to help manufacturers create quieter products.
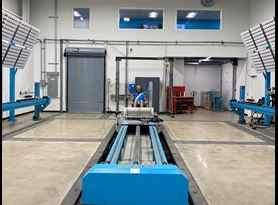
Sled Testing
Element’s unique electromagnetic sled has the highest level of accuracy, repeatability, and efficiency when compared to any other sled system currently available on the market.