Element provides a comprehensive range of in-situ replication metallography and replica testing services to help you determine the strength, quality and remaining lifetime of your materials, avoid disastrous failures, and ensure safe and productive operations.
What is replication metallography?
Replication metallography is a non-destructive sampling procedure which records and preserves the topography of a metallographic specimen as a negative relief on a plastic film. The microstructural replica can be examined using a light microscope or Scanning Electron Microscope (SEM) for subsequent analysis.
The replicas may pick up loose particles or residue from the surface, which may be used for Energy Dispersive X-Ray Spectroscopy (EDS) analysis.
In-situ replication metallography and replica test capabilities
As one of the largest independent providers of non-destructive testing (NDT) services, Element offers unrivaled experience and expertise in in-situ replication metallography to perform and analyze replica tests for obtaining microstructures on-site, for subsequent examination and evaluation in fully accredited laboratory.
With over 20 years of experience in Petrochemical, Refinery, Industrials and Oil and Gas industries, we can perform replica tests on a wide range of metals and alloys such as austenitic stainless steels, nickel and chromium based alloys, carbon steel, low alloy steel, and duplex stainless steel.
From on-site evaluation of a component’s metallurgical and heat treatment condition to conducting a remaining life assessment study and a failure analysis project, our skilled teams of metallurgists can verify the on-site, non-destructive microstructure of any given component.
In-situ testing, analysis and interpretation
Element combines a diversity of advanced metallographic equipment and tools with a dedicated team of experienced metallurgists to conduct high quality of all replica examinations and deliver accurate and reliable results that you can trust.
We follow the guidelines in ASTM 1315, ASTM E3, ASTM E340 and ASTM E407 to identify, prepare and examine in-situ metallographic replicas.
Our metallurgists are highly skilled in the preparation of the replicas using a number of techniques and can advise you in choosing the appropriate method for your specific project needs.
In-situ replication metallography and replica examination services
- Microstructure evaluation
- Creep damage assessment – mostly on high-pressure and high-temperature equipment such as steamlines, boilers and reactors.
- Thermal degradation of the materials - mostly on stainless steels in high-temperature equipment, where detrimental precipitation and the Degree of Sensitization (DOS) can be assessed. Thermal degradation can also occur during unwanted high-temperature exposure, such as fire damage or hot spots.
- Failure analysis/crack analysis
- Hydrogen Embrittlement (HE)
- Stress Corrosion Cracking (SCC)
- Intergranular Corrosion (IGC)
- Graphitization
The Element advantage
Our Engaged Experts combine tests to get the most complete indication of the examined equipment; for instance, to determine whether a material has been thermally degraded, the replica tests are combined with hardness measurements. If microstructure examination is not sufficient on the surface alone, our metallurgists can take boat samples for examinations on (partial) cross-sections.
For more information about how we perform in-situ replication metallography and replica testing, or to request a quote, contact us today.
Replication Metallography: A Non-Destructive Solution
Element discusses replication metallography as a non-destruction solution to metallurgical evaluation.
Read MOREWhite Paper: What is Metallurgical Testing?
Metallurgical testing covers a huge scope of industries. Could metallurgical testing be helpful for you? Dr. John Tartaglia helps guide you through the basics of metallurgical testing.
Read MOREFAQ: What is Hydrogen Embrittlement?
Discover hydrogen embrittlement as Vikram Nanda, an expert in metallurgy and metallurgical failure analysis, provides answers to commonly asked questions in this article.
Read MORE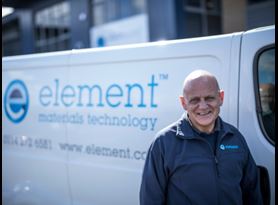
On-Site Metallographic Testing and Analysis
Element offers a wide portfolio of on-site metallographic testing and analysis to monitor real-time component condition and detect potential or existing damage.
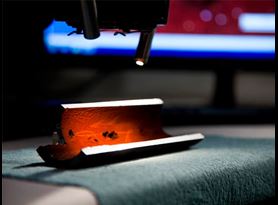
Failure Analysis
Find out how Element's global team of failure analysis experts learn from the past, to help prevent future failures in service.
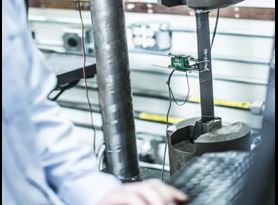
Stress Rupture and Creep
Find out how Element uses a variety of stress rupture and creep test methods to assess the effect of long term stress on metals, composites and a range of other advanced materials.
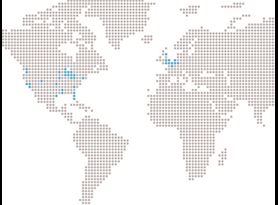
Element Locations
Learn more about our laboratories - where they are located; the unique capabilities they have and how they can help you solve your technical and commercial challenges.