Sandwich panel composites are made of two thin, stiff face sheets bonded to a relatively thick, lightweight core. To understand the durability and performance of a sandwich panel, the entire construct must be tested together.
Composite sandwich materials have stiff skin around the core which provides superior bending properties with lower weight. The constructs are commonly used in aircraft, satellites, marine and automotive applications, and wind turbines.
ASTM Composite sandwich panel test methods
Element provides a variety of mechanical testing methods to evaluate the properties of composite sandwich structures, including flatwise tensile, core and plate shear, bending, and compression.
Out of plane/Flatwise tensile ASTM C297
Our experts perform out-of-plane or flatwise tensile according to ASTM C297. The test set up requires bonding the skins to loading blocks and pulling them apart perpendicular to the sandwich panel. The failure mode typically takes place in the core and sometimes in the adhesive.
Core shear/Plate shear testing ASTM C273
Core shear or plate shear testing is a useful method for understanding the shear properties of the sandwich construct. When testing according to ASTM C273, the sample skins are bonded to the plates and loaded in opposite directions in the plane of the sandwich panel, creating a shear condition. The failure mode typically takes place in the core. In-plane shear may also be performed using a “picture frame” configuration. Element provides panel shear testing of composites for specimens of various sizes and to high loads.
Bend testing sandwich materials ASTM C393
ASTM C393 outlines the process for bend testing sandwich materials. Different properties may be measured by changing the span of loading. For example, a shorter span of loading provides data for core shear properties and a longer span of loading provides data for skin properties.
Compression testing ASTM C364 and ASTM C365
Element performs compression testing both in-plane and out-of-plane. ASTM C364 provides guidance for in-plane or edgewise compression testing, and ASTM C365 covers out-of-plane or flatwise compression testing. Both compression methods help determine modulus data.
To simulate in-service damage, composite sandwich panels undergo fatigue testing in either bend or compression to evaluate damage growth. In these cases, the materials may have impact damage, or flaw deliberately included during construction.
Adhesive bond testing ASTM D1781
The adhesive bond used to connect the sandwich panel materials is evaluated in peel. Climbing drum peel, outlined in ASTM D1781, is a common quality control test for sandwich panel construction. Element is involved in the development of current methods for more analytical cantilever peel methods.
Composite testing at Element
Our composite testing experts have a breadth of experience testing composite sandwich panels to a variety of test methods and specifications. We work diligently to ensure your materials and constructs are quality, compliant, and fit-for-purpose.
For more information about testing sandwich panel constructs or to request a quote, contact us today.
Repair of Carbon Fiber Composite Materials
When you use composite products, it’s essential to understand if and how the materials can be repaired to ensure your end products are safe and fit for their purpose. LEARN MOREQualification of the Properties of New Composite Materials
Composite materials are made from two or more different materials that, when combined, are stronger than those materials individually, composites are typically designed with a specific use in mind. LEARN MOREStructural testing of composite components
What are the stages of composites testing? Can I rely on standard tests available, or do I need a test method that is bespoke to my components? LEARN MOREUnderstanding Composite Compression Test Methods
Composite compression testing is crucial for screening new materials and maintaining quality control. Discover common test methods and how they compare against each other.
LEARN MOREReady to request a quote?
Our deliverable is certainty - high quality data, test reports and certificates that you can absolutely rely on when making decisions about your materials and compliance. Engage with an expert today.
Related Services
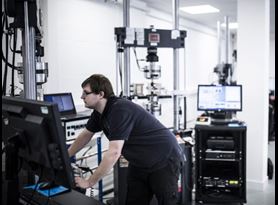
Composite Fatigue Testing
Whether testing to a specific standard or developing a custom program, Element’s experts are ready to assist with your composite fatigue testing needs.
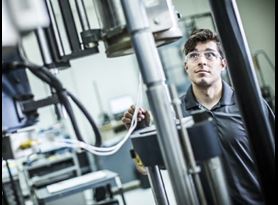
Shear Testing of Composites
Our composite testing experts provide shear testing methods including interlaminar, in-plane, and v-notch to measure the shear properties of your material.
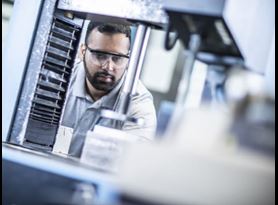
Understanding Composite Compression Test Methods
While there is no set standard for testing the compressive strength of composites, our experts can help you select the test methods that will generate the required result.
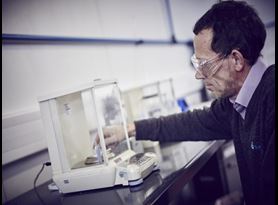
Polymers Testing
Element performs a range of mechanical, electrical, flammability tests and utilizes thermal analysis tests to characterize the composition of polymers and composite materials.