Coatings provide critical asset protection in some of the harshest operating environments within the global Energy sector. As a recognized leader in the provision of coatings testing, inspection and advisory services, Element helps you understand how your coating products and systems will perform once deployed in the field.
Energy coatings testing under extreme environments
With a global reach of coatings laboratories in the UK, USA, Europe and Asia, Element provides a comprehensive range of coatings testing services to the Energy, Aerospace, Defense and Transportation sectors.
Our coatings testing and evaluation services for the energy sector, ranging from the large-scale simulation of deepwater environments in pressure cells to lifetime insulation performance of flowline systems, covering everything from standard pre-qualification coatings testing up to high-level polymer testing using various exposure techniques.
Element has the capability to conduct a vast number of environmental exposure tests which include IMO PSPC test protocols for seawater ballast water tanks and cargo oil tanks. Combined with this we have a large global capacity and capability for testing to Norsok M501 and ISO 12944 pt 6 & 9 which is utilized by the industry to evaluate heavy duty coatings for some of the harshest environments.
The combination of high-capacity labs and advanced technical knowledge allows us to replicate difficult operating environments in accordance with all of the applicable local, national, regional and international standards, including subsea, marine, ageing, chemical, offshore and onshore applications.
The Element advantage
Our Engaged Experts consistently provide accurate and reliable data regarding material properties, allowing clients to develop new types of coatings, validate the integrity of coatings and in the process help solve, mitigate and prevent coatings related problems occurring in the Oil & Gas sector.
Whether they are applied to pipelines, oil rigs, chemical plants or ships, Element has the skills to help protect your most critical assets. Contact an expert today.
Failure Analysis of Pipeline Coatings
This free white paper includes an extensive case study of the failure analysis of a 12-inch diameter Fusion Bonded Epoxy (FBE) coated steel pipe that showed blistering of the coating and corrosion on the surface.
Read MoreStandard Update: Norsok M 501 edition 7
One of the most important standards for coatings testing in the oil and gas industry has undergone a major revision. This article explains the consequences for manufacturers and testing requirements.
Read MoreFailure Analysis of Pipeline Coatings
This free white paper includes an extensive case study of the failure analysis of a 12-inch diameter Fusion Bonded Epoxy (FBE) coated steel pipe that showed blistering of the coating and corrosion on the surface.
Read MoreOur Services
Element has a the most comprehensive range of coatings testing services in the Energy sector.
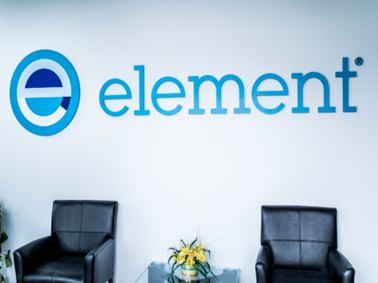
Thermal Conductivity Testing and Measurement
Element offers effective thermal conductivity and measurement services for a wide range of materials, to ensure they insulate, conduct and withstand temperature changes in Aerospace, Oil & Gas and Transportation applications.
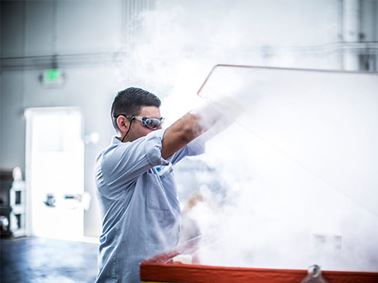
Salt Spray Testing
Find out how our Engaged Experts conduct salt spray testing, or natural salt spray (NSS) to evaluate the integrity of a coating in a corrosive environment or to test the corrosion resistance of a product or material.
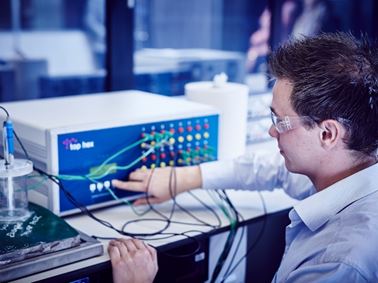
Pipeline & Field Joint Coatings
Element offers innovative testing solutions per ISO 21809 1-3 to improve pipeline and field-joint coatings performance in the subsea applications.
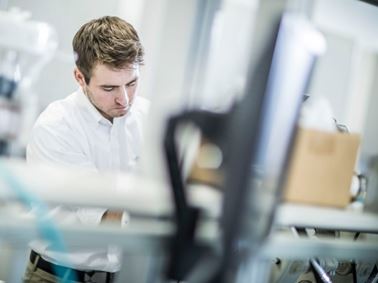
Coating Testing for Seawater Ballast and Cargo Oil Tanks
Element is accredited to perform the IMO set of testing standards for Protective Coatings of Seawater Ballast Tanks and Cargo Oil Tanks.
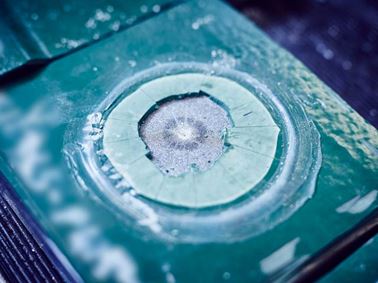
Mechanical & Physical Testing of Coatings
With a wide range of coatings testing services, Element provides flexibility testing (Mandrel and T-bend tests), measuring coatings density, volume solids and fingerprinting services.
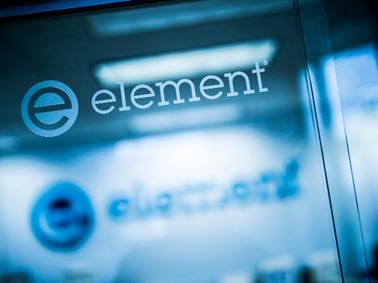
Water Immersion Testing
Element’s immersion testing services evaluate a coating’s resistance to in-service immersion conditions. This helps determine its suitability for corrosion protection during its service life.
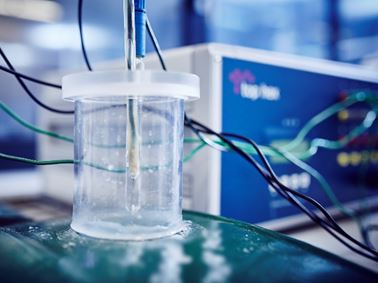
Cathodic Disbondment
Cathodic disbondment testing is often used as part of a suite of tests to to investigate the behavior of the coating system when subjected to either sacrificial or impressed current flows.
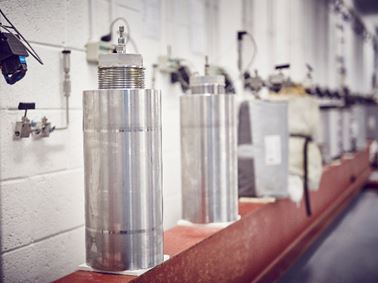
Coatings Chemical Resistance
Element has the capability to conduct coatings chemical resistance tests to evaluate the resistance of coatings to chemical attacks in a variety of service environments.
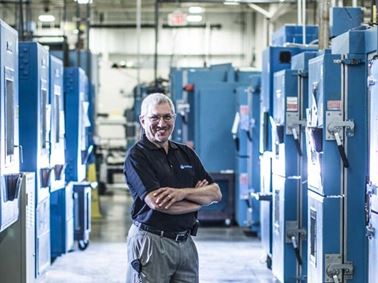
Accelerated Weathering
Find out how Elements experts help to make certain that plastics, rubbers, composites, paints and coatings, metals, textiles, stone and concrete can withstand extreme weather conditions around the globe.
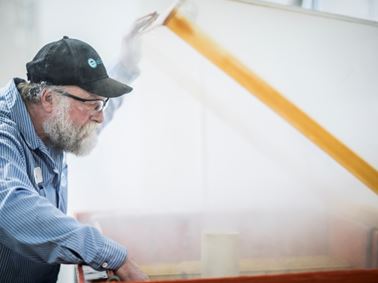
ISO 12944
Element offers testing to international standards ISO 12944-6 and 12944-9 (formally ISO 20340) to aid in the selection of suitable paint systems for corrosion protection.
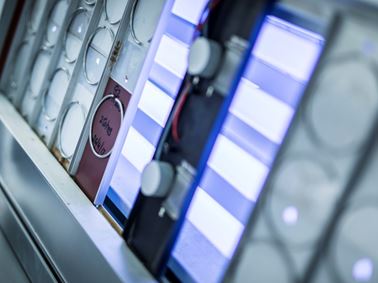
NORSOK M-501
Element offers testing to NORSOK M-501 to support the selection of coating systems providing optimum protection for offshore installations.