Element has the capability to conduct coatings chemical resistance tests to evaluate the resistance of coatings to chemical attacks in a variety of service environments. We specialize in a broad spectrum of testing methods including ISO 2812-1, Atlas cell and Isothermal Immersion (NACE TM0174), Pressurized Atlas cell (modified NACE TM0174) and Autoclave testing (NACE TM0185).
Coatings are utilized to protect substrates from a variety of and sometimes very hostile chemical exposure environments. Chemical resistance testing of coatings can be used to determine a material’s resistance to chemical attack, which can include, acid, alkali, hydrocarbons, alcohols as well as specific production fluids and area-specific crude oils. Temperature and pressure aspects of the environment may also be necessary to consider.
With years of experience in coatings testing and a global reach of laboratories, Element’s team of coating specialists can support you with coating evaluation and select the most appropriate testing for the service environment.
Chemical resistance test methods
Element performs coatings chemical resistance testing by entirely or partially immersing test specimens into a series of chemicals, similar to ones in which the coating is subjected to in the real-world environments. The test samples are examined for film failures, alterations or discoloration, change in gloss, blistering, softening, wrinkling, loss of adhesion or any other deterioration.
• ASTM D6943 – Immersion testing of coatings and linings
• ISO 2812-1 – Chemical immersion
• NACE TM0174 – Isothermal immersion; standard and pressurized atlas cell testing
• NACE TM0185 – Autoclave testing
Fluids we test
Our coatings chemical resistance laboratories provide testing with numerous chemicals found in typical Oil and Gas industry operating environments. We can consider a wide variety of different chemical types and work to ensure they can be handled safely.
Atlas cell test - NACE TM0174
Element provides atlas cell testing services to assess the immersion resistance of a coating in accordance with NACE TM0174. We help you evaluate internal coatings and linings for materials selection, determine chemical resistance and qualify new coating for your specific project needs.
The Standard Atlas Cell (SAC) tests determine the performance and suitability of internal protective coatings or linings when exposed to the chemically aggressive environment. The test can also assess the coating’s ability to withstand the temperature difference between the internal and external surfaces of a coated substrate, causing the ‘cold wall effect’.
When service conditions involve pressure, our Pressurized Atlas Cell testing services can measure the coating’s ability to cope with the temperature difference between the internal and external surface when exposed to pressure, temperature, and any other internal environment.
Autoclave testing - NACE TM0185
In addition, Element’s coating chemical resistance programs include autoclave testing services in accordance with NACE TM0185. The test involves exposing test specimens to simulated Oil and Gas production fluids and gases (sweet or sour) at elevated temperature and pressure.
For more information about our chemical resistance testing services, or to request a quote, contact us today.
Failure Analysis of Pipeline Coatings
This free white paper includes an extensive case study of the failure analysis of a 12-inch diameter Fusion Bonded Epoxy (FBE) coated steel pipe that showed blistering of the coating and corrosion on the surface.
Read MorePaints and Coatings Failures: A Guidebook on Causes and Remedies
Failure analysis is a valuable tool when investigating the root causes of asset failure, and developing a corrective action plan to ensure your paints and coatings adhere and remain intact.
READ MOREStandard Update: Norsok M 501 edition 7
One of the most important standards for coatings testing in the oil and gas industry has undergone a major revision. This article explains the consequences for manufacturers and testing requirements.
Read MoreRelated Services
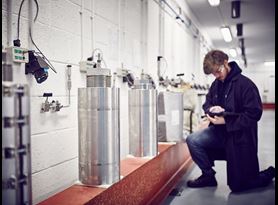
High Pressure High Temperature (HPHT) Exposure Testing Services
We offer extensive services for the qualification and compatibility of polymer materials exposed to production fluids at high pressure and high temperature (HPHT).
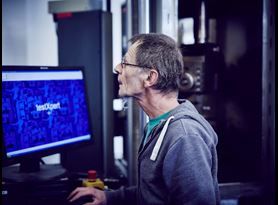
Corrosion Inhibitor Testing
Element’s corrosion inhibitor testing experts select the most suitable corrosion inhibitor to protect your assets and extend their life span within the energy industry.
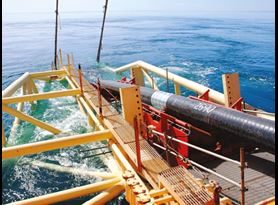
Coatings Testing
We offer world-class materials expertise in polymers, elastomers, thermoplastics, composites, and structural adhesives. With a global reach of coatings laboratories in the UK, USA, Europe, and Asia, Element provides a comprehensive range of coatings testing services to the Energy, Aerospace, Defense, and Transportation sectors.
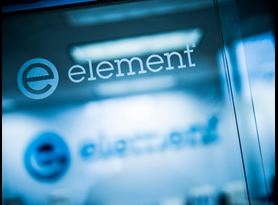
Water Immersion Testing
Element’s immersion testing services evaluate a coating’s resistance to in-service immersion conditions. This helps determine its suitability for corrosion protection during its service life.