What is Materials testing for Paint and coatings – and why do I need it?
This type of testing explores the material properties of coatings, including paint, to assess how it behaves when applied to a surface, and any impact on the surface itself. We can also simulate extreme conditions, assessing quality, performance, and compliance in even the most demanding situations. Our expertise includes regulatory compliance testing, failure analysis, process evaluation, chemical analysis, de-formulation, hardness assessment, adhesion strength, material selection, and consulting.
Industries such as automotive, construction, aerospace, and manufacturing rely on this testing to ensure coatings meet safety and regulatory requirements whilst maintaining desired aesthetics and protective properties. Our comprehensive paint and coatings testing safeguards against defects, promoting product longevity, all within rigorous environmental and safety standards.
Key Benefits of working with Element for Paint and Coatings Testing
- Material-Focused Testing for Your Peace of Mind: Our comprehensive paint and coating testing services ensure your coatings not only meet but exceed specific requirements under different environmental conditions. This means a more durable product, preventing headaches like peeling and defects that could affect your product's lifespan.
- Technical Guidance Throughout Your Testing Journey: Element's experts are here for you every step of the way. We provide information and support at every testing stage, helping you understand the technical aspects of coatings, testing methods, and findings and guiding you through necessary next steps.
- Comprehensive Testing for Consistent Quality: Rely on us for meticulous testing results, ensuring your coatings meet the highest quality and performance standards. We don't just meet requirements; we prioritize ensuring your paints and coatings precisely match your unique needs and remain compatible with your specific product and application.
Looking for Cost-effective solutions?
In a world where saving money matters, our all-in-one services, including lab testing, engineering support, and R&D guidance, are your go-to solution.
Whether you're after a quicker timeline or better resource planning, our integrated approach makes things easy, speeding up decisions and solutions. When you partner with Element, our experts handle all your needs, so you don't have to juggle multiple vendors. It's not just a time-saver; it cuts the hassle and costs of managing everything separately.
Secure Global Market Access and a competitive edge
In today's global marketplace, gaining market access and staying competitive is key for businesses in every industry. That's where paint and coatings testing, with a focus on material properties, comes into play. At Element, our paint and coatings testing services do more than just meet regulatory requirements—they ensure you exceed the strict global standards for quality and performance. This not only opens doors to new markets but also positions you as a strong player internationally. By showcasing the reliability, durability, and safety of your coatings through our thorough material-focused testing, you're not just meeting global demands; you're building a reputation that instills trust and confidence in both current and future customers.
Our paint and coatings expert
Our Materials Testing Capabilities for Paint and Coatings
- Paint and coating adhesion
- Paint and coating film thickness
- Flexibility
- Film hardness
- Color and gloss measurements
- Paint or coating deformulation/material identification
- Basic and controlled irradiance spray
- Humidity testing
- Cyclic corrosion
- Immersion testing
- Rotary and vertical dip/dry
- Temperatures up to 260°C (500°F) (ovens) and 1100°C (2000°F) (furnaces)
- Subambient testing to -100°C (-150°F)
- Chemical compatibility
- Gravelometer testing
- Thermal cycling
- Autoclave testing
Industry-specific Services to Support your Needs
In addition to materials testing for paint and coatings, we also offer a wide variety of testing tailored for specific needs and industries, including the energy sector, medical devices, and for environmental factors:
- In the oil and gas industry, coatings play a crucial role in shielding your equipment and structures from tough conditions. Element's experts make sure your coatings can handle extreme temperatures, corrosion, and chemical impacts. Learn about our energy coating testing services.
- For medical products, we know that safety and reliability are non-negotiable, so our testing services ensure that coatings used in medical devices and equipment meet rigorous quality and safety standards, prioritizing patient well-being and compliance with regulations.
- Whilst for environmental applications, we offer services that consider the particulate release of a product, allowing for assessments to be drawn regarding the environmental impact of your coatings - essential for sustainability and compliance with environmental regulations.
Why Choose Element
When you choose Element for your paint and coatings testing, you're tapping into a global network of cutting-edge laboratories that specialize in material properties. Plus, you connect with experts who really understand industry regulations.
Our team is ready for any challenge, and we don't just test to meet standards – we collaborate with you to create customized paint testing plans.
With our worldwide network covering in-lab testing, engineering support, and comprehensive research and development guidance, we can provide better efficiency and cost-effectiveness for your project, no matter where you are.
Contact us today to explore our comprehensive material testing range for paint and coatings.
Testing and Evaluating Thermal Spray Coatings
Thermal spraying is a popular method of applying a metallic, ceramic, plastic, or composite coating to a device or material. The process finds uses across a wide range of industries, including medical, aerospace, manufacturing, and energy. READ MOREPaints and Coatings Failures: A Guidebook on Causes and Remedies
Failure analysis is a valuable tool when investigating the root causes of asset failure, and developing a corrective action plan to ensure your paints and coatings adhere and remain intact.
READ MOREFailure Analysis of Pipeline Coatings
Case study on the failure analysis of a Fusion Bonded Epoxy (FBE) coated steel pipe that was under cathodic protection while in service and showed blistering of the FBE coating and corrosion on the surface.
Read MoreOur Services
Element’s coating testing laboratories will help you determine what test types are appropriate for your products.

Corrosion Testing
Find out how Element's corrosion testing programs can drastically reduce the risks associated with corrosion.
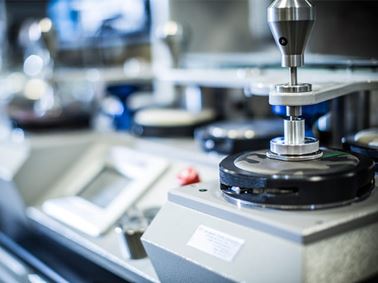
Abrasion & Wear Testing
Our Engaged Experts perform abrasion and wear testing that will help predict the lifetime and durability of a material or coating.
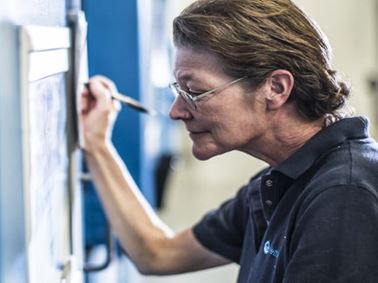
Ultraviolet Exposure and UV Testing Services
Element’s comprehensive exposure services can evaluate polymers, coatings, metals and other materials to a variety of methods and specifications.
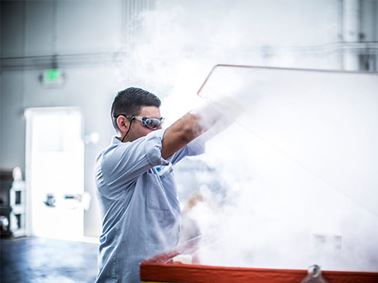
Salt Spray Testing
Find out how our Engaged Experts conduct salt spray testing, or natural salt spray (NSS) to evaluate the integrity of a coating in a corrosive environment or to test the corrosion resistance of a product or material.
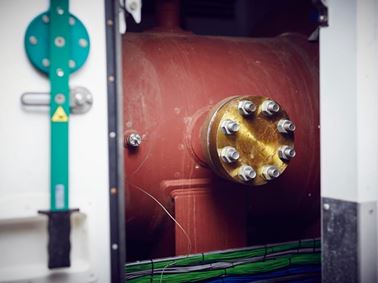
Thermal Insulation Coatings
Our industry-leading coating expertise covers a wide range of applications and client needs. Using state-of-the-art equipment and techniques, we provide consulting, investigation and testing of thermal insulation coatings.
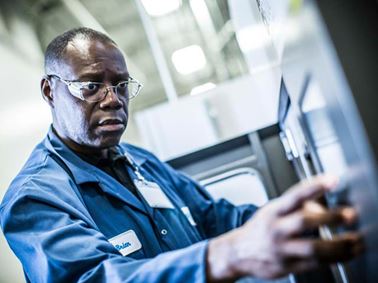
Accelerated Weathering Testing
We provide Xenon Arc testing, Carbon Arc testing and UV Exposure testing to simulate exposure of your products or materials to ultraviolet radiation, temperature and moisture.
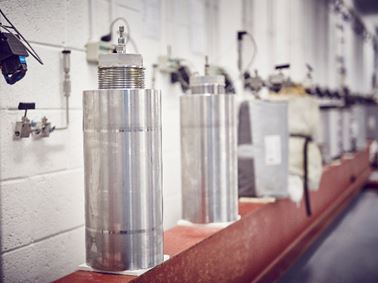
Coatings Chemical Resistance
Element has the capability to conduct coatings chemical resistance tests to evaluate the resistance of coatings to chemical attacks in a variety of service environments.
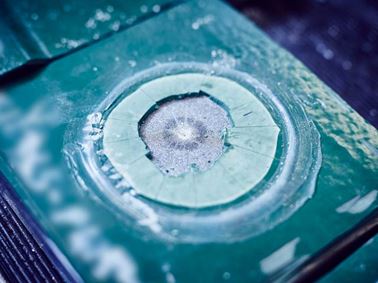
Mechanical & Physical Testing of Coatings
With a wide range of coatings testing services, Element provides flexibility testing (Mandrel and T-bend tests), measuring coatings density, volume solids and fingerprinting services.