Thermal insulation coatings provide a variety of benefits to offshore pipeline systems besides temperature control such as corrosion inhibition, impact and abrasion resistance. Our testing services help ensure subsea pipeline coating performance throughout their service life.
Element’s thermal insulation coating testing services include a variety of mechanical (link), environmental (link), chemical (link) and ageing methods designed to simulate real-world use and provide accurate and reliable data about materials properties. Our oil and gas experts have experience in the lab and in the field, and can assist with a wide range of testing, consulting and investigative projects.
Thermal insulation coating capabilities
• Pre-qualification testing of factory-applied and field-joint coatings
• Simulating environmental and operating temperatures at sub-sea conditions
• Short- and long-term exposure testing
• Insulation materials testing
• Hydrostatic water
• Validating coating integrity
• Developing new subsea pipeline coatings
• Determining failure modes and how to prevent them
• Wet ageing
• Water absorption
• Pressure effects
• Ring shear
• CTE
ISO 12736 - Simulated Service Test (SST)
Our labs provide wet thermal insulation coating qualification using the simulated service testing outlined in ISO 12736 (full-scale pipes with factory applied-coatings and field-joint coatings). We can perform long-term tests at pressures up to 300 bar, and temperatures down to 4-10 C (external) and 200 C (internal).
From pipelines, flow lines, components and subsea equipment and structures, our SST services cover testing of a wide range of wet insulation materials for subsea deployment.
Our unique SST capability include testing two 5 meter pipes simultaneously, as well as other types of subsea pipeline equipment.
For projects with other requirements, our experts can assist in designing and implementing custom or unique programs.
Our Services
Element has one of the most comprehensive ranges of materials testing and qualifications services for the Oil & Gas sector.
Ready to request a quote?
Our deliverable is certainty - high quality data, test reports and certificates that you can absolutely rely on when making decisions about your materials and compliance. Engage with an expert today.
Our Materials Testing Services
Related Services
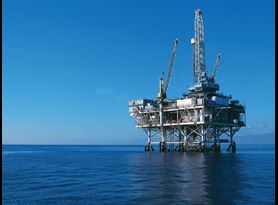
Oil & Gas
Element's global platform of laboratories offers advanced services designed to test and qualify materials intended for use within the environments of the future.
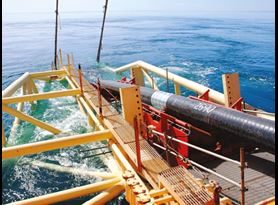
Coatings Testing
We offer world-class materials expertise in polymers, elastomers, thermoplastics, composites, and structural adhesives. With a global reach of coatings laboratories in the UK, USA, Europe, and Asia, Element provides a comprehensive range of coatings testing services to the Energy, Aerospace, Defense, and Transportation sectors.
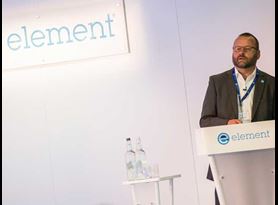
Resources
Discover blog posts, articles, white papers, webinars, and advice from our world-leading testing, inspection, and certification experts.
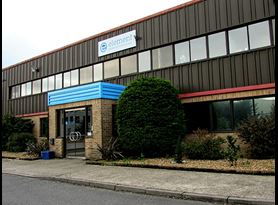
Element Hitchin
As Element's Global Center of Technical Excellence for Polymers, Element Hitchin has decades of experience providing a comprehensive range of highly specialized services.