Our spinal implants testing capabilities extend to fusion and non-fusion spinal devices, as well as predicate components, for feasibility testing and regulatory submission requirements.
Spinal implants can experience a variety of forces within the human body, so ensuring their durability and lifespan is important for the well-being of the user. Our trusted medical device testing allows your company to mitigate risk knowing that we are working diligently to help ensure your success and bring a safe product to market.
Common mechanical testing for spinal implants includes static and fatigue tests in different loading modes, such as axial, torsional, shear, flexion/extension, bending, lateral bending, and axial rotation.
Spinal implants are categorized into two groups: fusion devices and non-fusion devices. Spinal cages and stabilization systems are typically used to treat fractures, disc compression, and deformities, whereas non fusion devices are used to maintain spine mobility while relieving pressure.
Spinal Cage Testing Methods
Spinal cages are used to promote interbody fusion by being fixated in the disc or vertebral space. Element utilizes both ASTM F2077 and ASTM F2267 to characterize the mechanical properties of these interbody fusion devices (IBFDs) and Vertebral Body Replacements (VBRs). Additionally, hybrid and standalone devices that combine cage and screw systems have been on the market over the last several years and require additional evaluation. Additive manufacturing has also transformed the spine industry, adding requirements for both design and material qualification.
Static and Dynamic Testing (ASTM F2077): This method calls for various tests to determine mechanical properties, including static and dynamic compression, torsion, and shear. Prior to testing, profiled test pucks are manufactured to precisely mimic the profile of the device. These pucks are then affixed to the test frame along with the specimens, which are tested either statically or dynamically. Dynamic testing is generally performed in-vitro using saline solution to allow for SEM evaluation of the particulate generated during testing. In addition, mass-loss evaluations are performed to characterize the rate of wear during testing.
Load Induced Subsidence Testing (ASTM F2267): This static axial compression test is performed to determine the likelihood of spinal cage subsidence when subjected to compressive forces. Per ASTM F2267, the sample is placed between two Polyurethane test blocks and loaded until failure is achieved.
Spinal Construct Testing Methods
Spinal constructs generally consist of a combination of rods, hooks, screws, and connectors. Depending upon the intended goal, device designs can vary greatly. By using standardized test methods, mechanical properties can be compared across designs.
Spinal Implant Constructs in a Vertebrectomy Model (ASTM F1717): This standard outlines the requirements for static and dynamic characterization. Prior to testing, the plates or pedicle screw systems are carefully assembled and fixated to a pair of test blocks. These assemblies are then subjected to static and dynamic loading. ASTM F1717 specifies three static test methods: compression, torsion, and tension. The standard also calls for a dynamic compression curve consisting of multiple failures and at least two run-outs to 5,000,000 cycles under a constant axial load.
For Occipital-Cervical and Occipital-Cervical-Thoracic constructs, ASTM F2706 provides additional static and fatigue test methods for these specific device types.
Subassemblies Used in Spinal Arthrodesis Implants (ASTM F1798): This test method evaluates the various subassemblies and interconnection mechanisms used in spinal implants, such as rods, hooks, screws, and bands. The goal of ASTM F1798 is to determine the fatigue strength and resistance to loosening. Loading methods include: static A-P load (Fx), transverse load (Fy), axial gripping capacity (Fz), transverse moment (My), and axial torque (Fz).
Our medical device experts are ready to assist with your research, development and testing needs. For more information about our spinal implants testing services or to request a quote, contact us today.
Our Medical Device Testing Services
More from Element
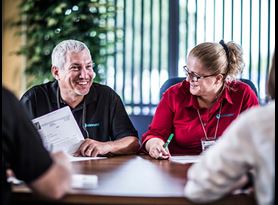
Advisory Services
Element's advisory services deliver world-class strategies that steer systems compliance at the program management level.
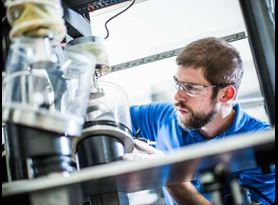
Medical Device Testing
As a comprehensive testing partner, you’ll enjoy the benefit of a single supplier source for all of your testing needs, from mechanical testing and environmental simulation to EMC and wireless device testing.
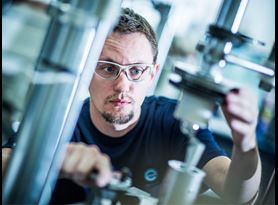
Fatigue testing
Element performs a wide variety of mechanical testing including fatigue testing of medical devices.
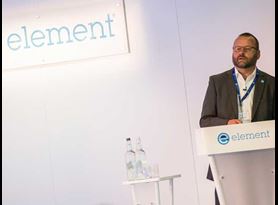
Resources
Discover blog posts, articles, white papers, webinars, and advice from our world-leading testing, inspection, and certification experts.