What is Aircraft Structural testing and why do you need it?
Structural integrity of an aircraft is crucial to the safety of passengers, crew and the environment. It’s therefore critical to be sure how the aerospace structure will withstand a wide range of conditions and scenarios over time, including the most extreme. Aircraft and aerospace structures testing involves rigorously assessing behaviour under multiaxial, dynamic loads, various stress scenarios, temperatures, and extreme conditions, to ensure the structure’s reliability and compliance with safety standards. This testing can help identify failures during the research and development phase before they occur, and quickly isolate issues as they arise. It can also help assess the efficiency of the aerospace structure which, on top of being completely safe, must be hyper lightweight and high performing.
Benefits of Aircraft Structural testing with Element
- Safety Assurance: Ensure the safety and reliability of your aerospace structures and components with our comprehensive testing solutions. Test in our diverse range of simulated real-world environments to feel confident in your structure’s integrity and durability.
- Early Defect Detection: Minimize risk of inflight failures or malfunctions with our rapid and precise identification of the smallest defects. With Acoustic Camera and Optical 3D Measurement options, covering specialist aerospace industry materials, like carbon-fibre-reinforced composites.
- Meet Industry Compliance: Ensure legal compliance with relevant industry regulations and certifications, allowing your access to market. Our team are experts at helping navigate the complex regulations required.
- Faster Time-to-Market: Accelerate the test and validation process to get your products to market faster and gain competitive edge. We understand the need to balance rigorous testing with the importance of getting to market quickly. Our combined testing, engineering, design, and production services help streamline your process, reducing lead times and ensuring efficient project execution.
- Non-Destructive Testing Methods: Harnessing the power of nondestructive testing methods like Acoustic defect detection, Instrumentation, Deformation measurement, and Multiaxial Testing (including multiaxial structures testing), we can uphold the integrity of your aircraft structural components. Our non-destructive testing techniques safeguard component quality, minimize expenses, bolster safety measures, and deliver comprehensive defect detection, without damage.
Cutting-Edge Testing Facilities
The safest, most efficient and innovative designs require the very best facilities to put them through their paces. Element has multiple hydraulic cylinders and high capacity measuring systems that can handle more than 250 channels. These systems are available to test complex assemblies and components under multiple multiaxial stress scenarios. We can also test these components at temperatures from -70°C up to 415°C as well as under extreme loads or special climactic conditions (e.g. moisture and temperature). With a large suite of structures testing inventory comprising of more than 60 actuators and load cells covering a range of 1kN to 1MN, two configurable multichannel control as well as appropriate expandable data acquisition systems, Element has demonstrated the capability and the know-how to perform most complex and highly sophisticated test campaigns over the last decades.
Supporting Design and Innovation
We continue to work with all of the Aerospace Primes and their Supply Chain partners and provide comprehensive design services to create fixtures, adaptors, support frames, and other necessary components required for testing. Our design team utilizes state-of-the-art software and advanced engineering principles to develop robust and efficient solutions that optimize the testing process. By working with you throughout the early R&D stages, utilizing a combination of engineering (Rig Design and test preparation) and Digital engineering (Analysis and Digital Twin) Element is your partner in development and testing of innovative new aerospace designs and technologies to advance the field and keep ahead of the competition, enabling you to create structures that are not only safe but lightweight and high performance.Aircraft structural testing capabilities from Element:
Our aircraft structural testing hardware includes hydraulic cylinders, load frames, a unique autoclave system, furnaces, climate chambers, an impact drop tower, and a mobile gas gun; we offer impressive key specifications:
- The capability to apply stressor loads of up to 1MN, ensuring thorough testing under significant stress.
- Our equipment offers various base plates, with the largest reaching sizes of up to 10 x 5 meters, providing exceptional flexibility to accommodate a wide range of test setups.
- Operating frequencies of up to 200 Hz can be applied, allowing for dynamic testing scenarios.
- A wide temperature range from -70°C to 415°C enables testing under extreme environmental conditions.
- Our robust data acquisition system, featuring over 256 channels, ensures comprehensive data collection during testing and provides a detailed understanding of structural performance.
- Two control systems, each supporting up to 32 channels, offer precise control and monitoring capabilities.
- The maximum pressure units for this equipment are 100 bar for fluids and 76 bar for gases, ensuring structural integrity under high-pressure conditions.
As well as the above test procedures, our experts can also offer further supportive engineering services.
Why Choose Element?
In aerospace, rigorous testing is crucial - Element offers some of the most comprehensive aerospace structures testing solutions available, with advanced facilities, cutting-edge techniques and decades of expert testing experience. Being the largest, independent provider of materials testing, product qualification testing, and advisory services to the global Aerospace industry we have the capabilities to simulate extreme temperatures and climates and an extensive inventory of actuators and load cells, our experts excel in executing sophisticated test campaigns, ensuring the longevity and integrity of aerospace components.
To learn more about Element, or to discuss your options, contact our team today.
Understanding creep and stress rupture testing
Creep damage is an everyday reality, affecting almost everything around us in some way. It is constant, irreversible, and mainly affects equipment subjected to continuous, elevated temperatures during its normal service life. Learn how to mitigate the risks. LEARN MOREWEBINAR: Repair of Carbon Fiber Composite Materials
Join Lars Wistfors and Annelie Eveborn for an on-demand webinar to help you understand what a carbon fiber composite is, the damage that can occur, and determine if it is safe and cost-effective to repair your materials. WATCH NOWMore from Element
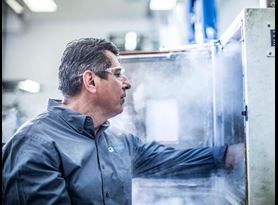
Product Testing
From environmental & dynamic testing to highly specialized tests such as bird strike and hydrodynamic ditching testing, we're the trusted testing partner to the world's most recognized component and system manufacturers.
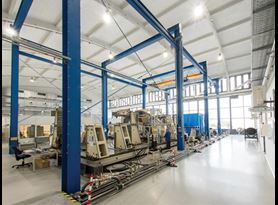
Element Berlin
Element Berlin is a leading Aerospace laboratory specializing in complex product testing services requiring large scale rigs and equipment such as spin testing, structures testing and fluid dynamics testing.
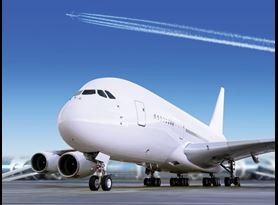
Our Services in Aerospace
Engaged in testing virtually every material, component and system on commercial aircraft, Element's deliverable is mission critical, certainty.
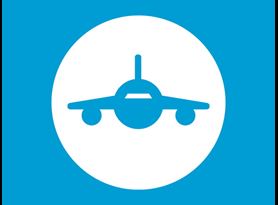
Element Acquires TRaC GLobal
Element’s continued investment in its Aerospace Product Qualification Testing (PQT) ensures that it remains uniquely positioned to deliver on both the PQT and Materials Testing requirements of Primes and their supply chain partners.