Qualify your products with confidence – verify their performance, safety, and compliance using Element’s world-leading PQT services. With one of the largest and most complete sets of product qualification testing capabilities and services available, we can help you drive innovation across Aerospace, Construction, Consumer Products, Defense, Digital Engineering, Energy, Life Sciences, Transportation, and Telecommunications.
What is Product Qualification Testing?
Product qualification testing (PQT) is the evaluation of a product to ensure it meets defined standards and regulations. Through a series of tests, it verifies performance, safety, and compliance with industry requirements. This process guarantees your product's quality and reliability, assuring that your products are safe and fit for purpose before entering the market.
Key Benefits of Product Qualification Testing Services
- Strategic Support for R&D Challenges: Our experts provide crucial specialist knowledge, aiding you in overcoming intricate research and development challenges.
- Efficient Testing for Faster Time to Market: Sound testing programs save time and money, ensuring a faster time to market and superior product outcomes.
- Comprehensive Risk Mitigation: Designed to minimize risk, our program improves product reliability and safety through thorough iterative testing and full life-cycle guidance.
- Global Market Access and Compliance: International certification programs and accredited reports facilitate swift global market access across all continents, ensuring legislative and governmental compliance.
- End-to-End Assurance and Expertise: With over 100 years of testing experience and ISO 17025, ISO 9100, NADCAP, and JOSCAR accreditations, we provide you with end-to-end services, certifying your products as safe, quality, and compliant.
Product Qualification Testing (PQT) Expertise
Element collaborates with customers in cutting-edge research, development, and testing. Whether it's the integral components of future aircraft and spacecraft, groundbreaking innovations in autonomous vehicles, delicate medical implants for the human body, or the latest in digital and wireless communication devices, Element is at the forefront of providing expertise for product safety across a diverse range of industry sectors.
Replicating Real-World Conditions, for Your Product's Success
In our state-of-the-art testing facilities, we simulate real-world conditions through electromagnetic, environmental simulation, climatic, and mechanical testing to advance your products. We help your creations to stand resilient against lifetime challenges, providing you with the assurance that your product is tested and certified for success.
Your Product Qualification Testing Experts
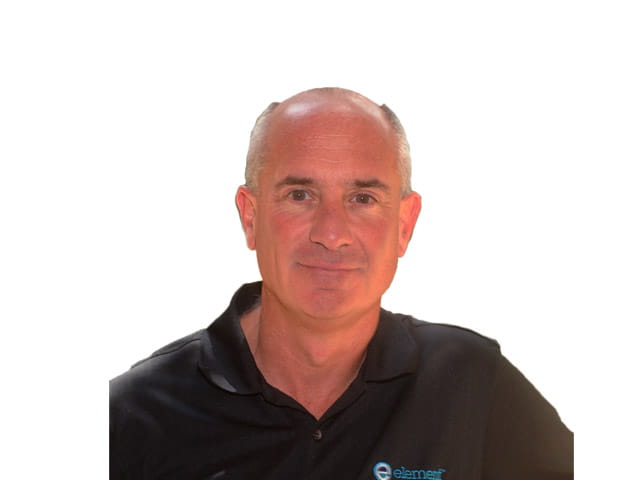
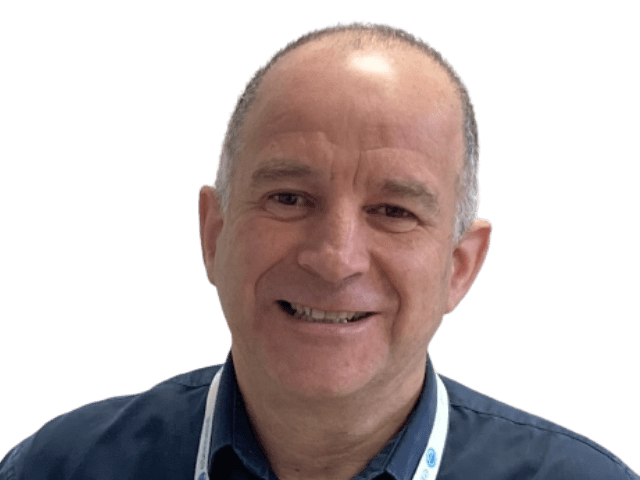
Chris Stone
Department Head of Testing Solutions.
“Element offers both routine testing (Dynamics, Climatic, and EMI/EMC) as well as specialty and bespoke testing. Our goal is not to be just your test house, but your active partner in helping to achieve your end objectives. Our experts can design custom test rigs that can benchmark failures in the field, allowing for improved redesigns that can be tested for success very quickly. We are your one-stop shop for any of your testing needs.”
David Lichtman
ELEMENT TECHNICAL DIRECTOR, AEROSPACE & DEFENSE
Product Quality Testing Key Services
Our comprehensive product qualification testing process is designed to empower customers at every stage.
- Advice: We offer a robust testing program for cost-effective and accelerated market entry. Our experts can help you to overcome complex challenges, ensuring successful outcomes from the start.
- Testing: Our leading engineering simulation and testing facilities in North and South America, Europe, and Asia replicate the electromagnetic, climatic, and mechanical conditions encountered in a product's working life.
- Certification: Our international certification program helps you understand the requirements of your target market, identify what standards and tests are required, and compile the technical documentation needed to apply for certification.
- Market access: Our approvals team uses our accredited test reports and in-country authorities to give you fast global market access to virtually any territory worldwide.
Why Choose Element?
As your global market access partner, we offer a comprehensive suite of end-to-end services, supported by certifications from ISO 17025, ISO 9100, JOSCAR, and NADCAP-accredited labs, ensuring unmatched customer confidence. With over a century of testing expertise, our customers trust us to deliver unparalleled product qualification testing across diverse industries.
For more information about our global product testing services or to request a quote, contact us today.
Find out more about Element and our credentials within the testing, inspection, and certification industry.
“Professional service, smooth communication, and fast testing.”
Joshua xue
Beijing Oriental Yuhong Waterproof Technology Co. Ltd
How to get a product tested for safety and pass first time?
Why do so many Products Fail Safety Testing? Read our helpful guide to ensure your electrical products pass their safety tests first time.
LEARN MOREUnderstanding the requirements for Global Market Access (GMA)
Read our article to learn what Global Market Access (GMA) is and how to gain certification for your wireless, electronic, & radio devices globally.
Read moreFeatured services
Click on one of the links below to find out more about our Product Qualification Testing Services
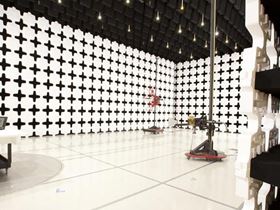
EMC Testing Services
Find out how Element delivers electromagnetic compatibility testing (EMC) solutions to RTCA/DO-160, MIL-STD-461 and Def-Stan 59-411 standards.
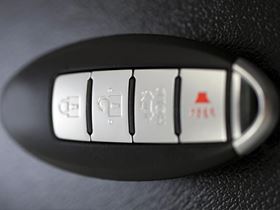
Radio Testing
We can help with EMC and safety testing and assist manufacturers who want to take their radio and wireless product to the global market
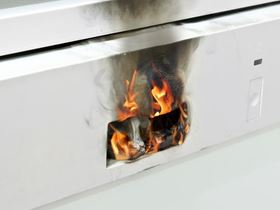
Product Safety Testing
Element is the ideal partner to help electrical device manufacturers, importers and distributors obtain the fast and efficient product safety testing and certification needed to trade their products worldwide.
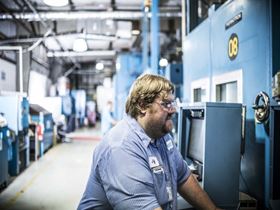
Environmental Simulation
Find out how Element provides combined altitude, humidity, temperature and vibration test to simulate real-world environmental conditions for the Aerospace sector.
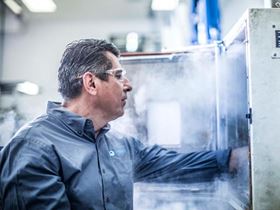
Combined Temperature, Altitude, Humidity & Vibration Testing
Element provides combined altitude, humidity, temperature & vibration testing to meet test requirements and simulate real-world conditions.
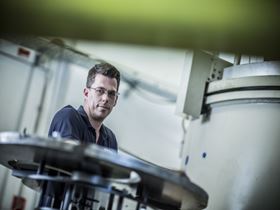
Structural Dynamics Testing
Find out more about Element’s structural dynamics testing services, which provide reliable, consistent data to the world’s most critical industries. From aerospace to construction, we help ensure that your products are fit for use, no matter what the application.
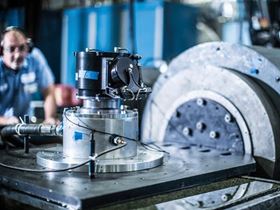
Vibration Testing
Find out how Element's vibration testing services help to make certain that the products we test for our customers will perform safely and as expected when in the field.
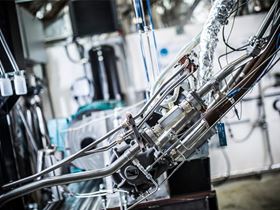
Fuel Systems
Find out how Element's comprehensive fuel system testing programs simulate in-service conditions at our world-class testing facilities.
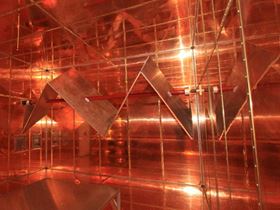
RTCA DO-160 Testing
Working with Element, our clients enjoy access to the most comprehensive EMC and environmental testing capacity of any independent Aerospace product qualification testing company in the world.
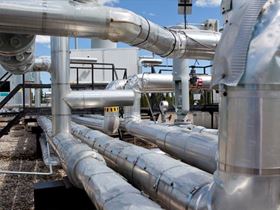
Explosive Atmospheres Testing
Find out how Element works with airplane manufacturers to produce and design equipment that can operate in fuel-air explosive atmospheres.
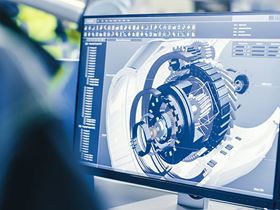
Modeling and Simulation Services
Optimize your project with our modeling and simulation services. Our expertise ensures cost-effective, compliant solutions. Enhance your project today.
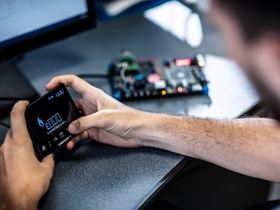
Matter Smart Home Standard
Element offers certification to the Matter smart home standard. Our experts are one of the few test and certification laboratories globally to offer guidance and testing.