Element’s on-site metallographic testing and analysis services help optimize material selection process, monitor real-time component condition and detect potential or existing damage in an early stage, to avoid costly failures and extend the lifetime of your equipment.
On-site metallography or metallographic replication is a non-destructive testing (NDT) method to evaluate the metallurgical condition of a metallic component. On-site metallography, also called field metallography, enables the necessary investigations to be carried out at the site without destroying the component.
Metallurgical test methods
With over 20 years of experience in the industry and access to a global network of expertise, Element offers a comprehensive range of metallurgical test methods in the field for components and materials that are too large, too heavy, or too fragile to be transported to a lab.
On-site metallographic analysis and testing services
- Production and preparation of test samples for non-destructive testing
- Chemical analysis and material identification using PMI and OES methods
- Coatings inspection
- Hardness tests including hardness measurements and portable hardness
- Ferrite content measurement for duplex steel and austenitic weld metal
- In-situ replication for mechanical and chemical microstructure evaluation and microscopic examinations
- Damage and degradation analysis
- EPR measurements to determine the Degree Of Sensitization (DoS)
- Support with interpretation of photo micrographs
The Element advantage
We are world leaders in providing materials characterization, mechanical testing, chemical analysis and metallurgical testing which enables us to commit to projects of all types and sizes, provide excellent turnaround, and deliver on-site metallographic testing and analysis services to clients worldwide.
We combine the most up-to-date equipment with the expertise of our highly skilled metallurgists to select the testing method that best meets your needs and requirements, and provide you with the same quality testing and accurate results of our on-site services that you would get in one of our accredited labs.
For more information about how we perform on-site metallographic testing and analysis, or to request a quote, contact us today.
Our Services
Element offers the most comprehensive range of on-site metallographic testing and analysis services for the Aerospace, Transportation, Industrial, Petrochemical and Oil & Gas sectors.
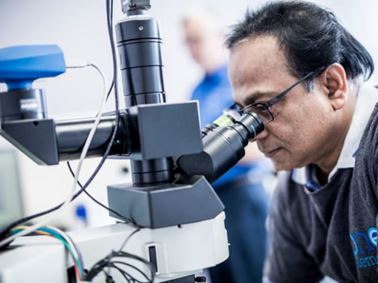
In-situ Replication Metallography & Replica Testing
Element conducts in-situ field metallography and replica testing services to evaluate the strength, quality and remaining lifetime of your materials.
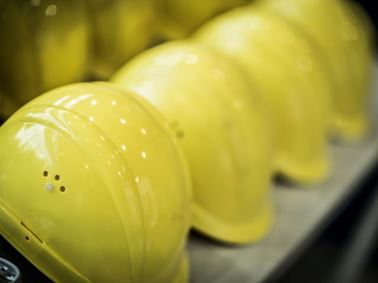
On-Site EPR Measurements - DoS Testing
Element performs on-site Electrochemical Potentiokinetic Reactivation (EPR) to determine the Degree of Sensitization (DoS) for faster and more efficient test results.
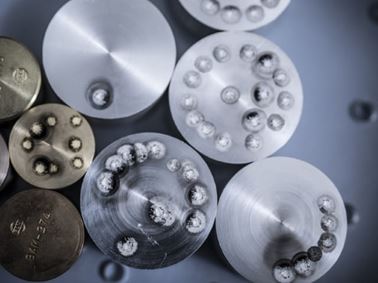
Optical Emission Spectroscopy (OES) Analysis
Element offers on-site Optical Emission Spectroscopy services for full chemical analysis of all metal alloys.

Positive Material Identification (PMI) Testing
Element offers Positive Material Identification (PMI) on-site with a portable XRF-analyzer for identification of medium and high alloyed metals or in one of our NDT laboratories.
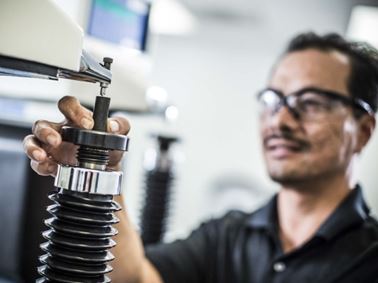
Hardness Testing
Element uses portable versions of hardness testing equipment to make on-site hardness measurements on large installations or equipment.
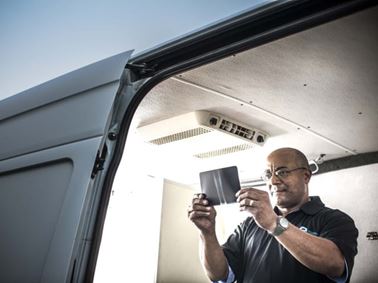
NDT Field Services
When employed at critical stages of the manufacturing or fabrication process, our NDE technicians work in the field to optimize production and ensure the quality of your finished product.
Other Energy Services
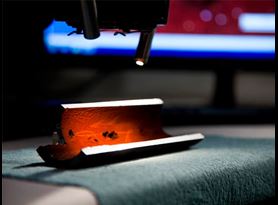
Failure Analysis
Find out how Element's global team of failure analysis experts learn from the past, to help prevent future failures in service.
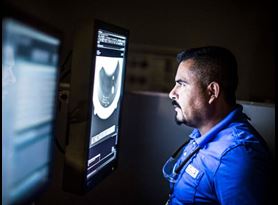
Non-Destructive Testing (NDT)
Element's NDT services comply with a wide variety of industry standards, government contracts, military specifications and unique customer requirements.
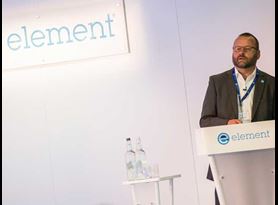
Resources
Discover blog posts, articles, white papers, webinars, and advice from our world-leading testing, inspection, and certification experts.
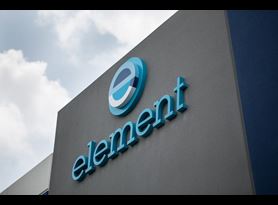
Local laboratories, global platform
Doing business with one of our laboratories enables our clients' access to our global platform of expertise, capacity and capabilities.