Certain oilfield polymers exposed to fluids containing hydrogen sulfide (H2S) will age chemically, with the rate of deterioration determined by H2S concentration and temperature. The resulting irreversible alteration in material property levels can have significant detrimental consequences for the functional performance of the part in an application (e.g., a seal). Element’s dedicated sour service teams can evaluate the performance of elastomers, thermoplastics and composites in sour fluids in accordance with standards such as NORSOK (M-710), ISO (23936, 10423), API (6A, 16C) and NACE (TM0187, TM0296).
Element has more than 25 years of experience of delivering testing solutions for polymeric materials used in a huge range of Oil & Gas sector upstream and downstream applications.
H2S is a toxic gas present in many fields throughout the world, sometimes at very high levels. Seals and other polymeric components must be specified and qualified appropriately to established international standards. In addition, Element can offer significant experience in designing and executing custom sour fluid exposure programs to meet demanding client requirements for both material evaluation/qualification, and functional testing.
Our Engaged Experts can evaluate non-metallic materials used in your offshore, renewable, and oil & gas applications. Our staff have contributed to both ISO and NORSOK standards development and are members of the relevant ISO Working Group committee. Element has run two internationally supported JIPs in the area of oilfield polymers: SOUR and SOUR2.
Our sour fluid exposure capabilities
– World-class scale sour fluid exposure facilities in the UK and the US.
– Routine exposure to 340 bar and 250 °C with mixtures containing up to 30% H2S.
– Exposure temperatures to 320 °C in special vessels.
– Customer-specific services; consultancy, material and functional testing programs.
– Rapid Gas Decompression (RGD) tests with sour gas mixtures.
Our experts can work with you to advise on the most suitable testing methods for your materials, develop and review test protocols, build custom R&D programs, and evaluate components and systems to meet your project requirements.
For more information about our sour service capabilities, or to request a quote, contact us today.
Our Materials Testing Services
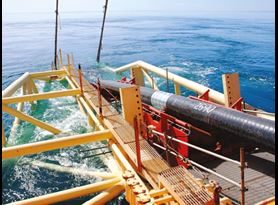
Coatings Testing
We offer world-class materials expertise in polymers, elastomers, thermoplastics, composites, and structural adhesives. With a global reach of coatings laboratories in the UK, USA, Europe, and Asia, Element provides a comprehensive range of coatings testing services to the Energy, Aerospace, Defense, and Transportation sectors.
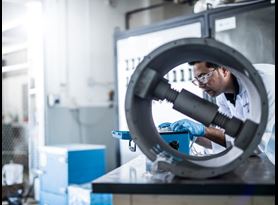
Sour Service Corrosion Testing
Element is one of a few ISO certified sour service labs in the world, providing sour service corrosion services for a variety of test types including NACE MR0175/ISO 15156.
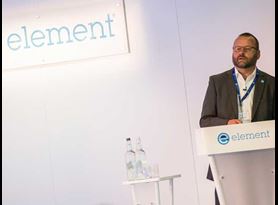
Resources
Discover blog posts, articles, white papers, webinars, and advice from our world-leading testing, inspection, and certification experts.
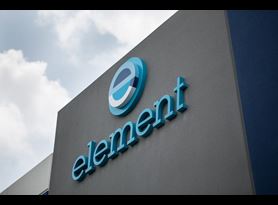
Element Houston
Element's Global Corrosion and Materials Technology Center for Metals and Polymers in the Energy sector