Ensure your materials are safe, robust, and fit for purpose. Element offers one of the most extensive ranges of hardness testing available – covering micro/macro hardness testing, in lab and field options plus all the choice techniques (Rockwell, Brinell, Bickers) alongside less common specialized testing like hot hardness testing. With precisely calibrated equipment and tailored solutions to meet a wide spectrum of standards, trust our experts to determine your materials’ ability to withstand other, harder materials.
What is hardness testing and what are the different techniques?
Hardness testing assesses how your material will resist force and penetration by other, harder materials, for example by scratching or denting. The results often correlate closely with tests into other crucial material properties, such as tensile strength. Used together, these tests help build a comprehensive picture of whether your material is robust enough to be widely adopted by engineers for materials selection, lot verification, and evaluating material processing. Hardness testing services offer a quick, efficient, and cost-effective method of evidencing the next steps in the development or manufacturing process.
Key Benefits of partnering with Element for Hardness Testing Services
- Utmost Accuracy and Precision: Ensure precise and reliable material quality for your manufacturing processes through specialized hardness testing techniques tailored to your materials.
- Testing as Diverse as Your Materials: Make informed decisions for your specific applications by relying on our expertise to guide your material selection process and conducting hardness testing on a wide range of materials.
- Fast Turnaround, Efficient Processes: Experience streamlined test procedures tailored to you through our efficient hardness testing, providing quick and reliable results.
- Full Compliance with Standards: Uphold the highest quality standards in your materials by utilizing our hardness testing to verify compliance with industry standards consistently, ensuring the reliability of your investments.
- Troubleshoot All Environments: Anticipate potential issues affecting your product in various end-use environments by leveraging our predictive hardness testing process tailored to your materials and conditions.
- Prevent Failure Before It Occurs: Gain confidence in your materials' integrity by employing specialized hardness testing as a proactive measure to prevent failures, identifying weaknesses before they impact your production.
Solutions as Diverse as your Materials – including Hot Hardness testing
The wide range of industries, uses and types of metallic / non metallic metals which may require hardness testing can pose a challenge when it comes to testing. That’s why Element offers an extensive range of different solutions, ensuring you can find a testing option to suit your needs – or multiple complementary test methods consolidated with one single testing partner. Our suite of hardness testing services includes microhardness, macrohardness, and covers all key and less common tests. We are proud to be one of very few commercial laboratories with hot hardness testing capabilities, allowing us to measure hardness at temperatures up to 1,600F. Whether your specifications involve complex alloys or advanced polymers, we can deliver precise and tailored hardness testing services that consistently meet the highest standards.
On-site and Lab-based Solutions for all types of samples
No matter your sample type, we offer flexibility in terms of where your testing takes place. Larger installations or equipment that require hardness assessments can often be challenging due to the practicalities of transporting them to a laboratory. With our portable testing equipment, Element’s experts can carry out comprehensive on-site tests, removing the logistical hurdles associated with transportation.
Our equipment supports various testing methods, supporting you with Leeb, Rockwell C, UCI (Ultrasonic Contact Impedance), and TIV (True Indentation Vision). For those who prefer the rigors of laboratory-based testing or have specific equipment requirements, we can offer this too – for example our cutting edge Hot hardness testing, using vacuum chambers to immerse your sample at particularly high temperatures.
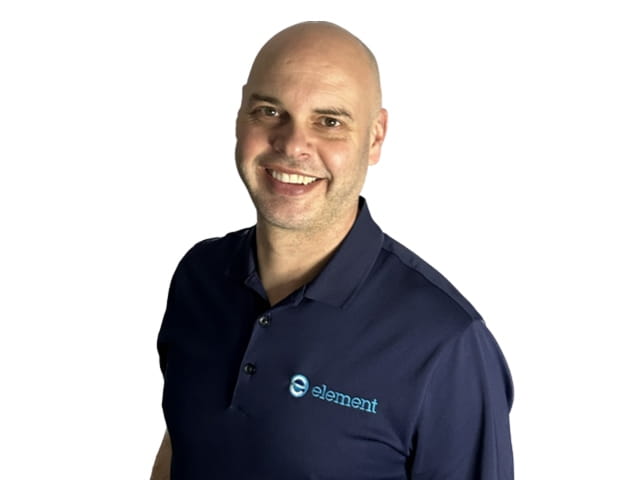
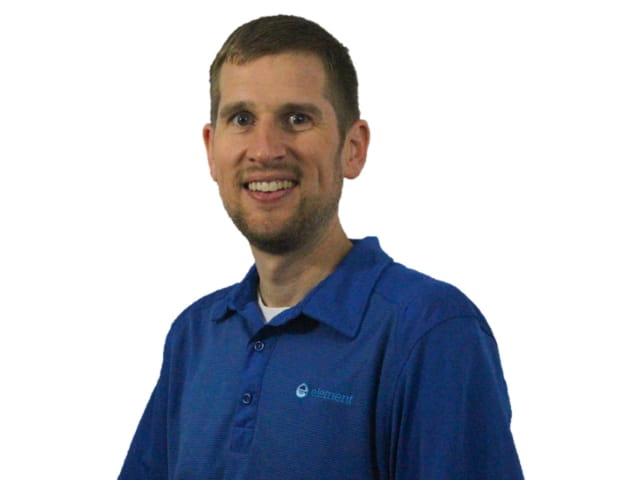
Justin Riebesel, PE, CWI
Expert metallurgist, Quality Manager and Deputy Export Compliance Officer READ MORE ABOUT JUSTINElement’s Hardness testing services and capabilities
Our experts can advise on which test is best for your specific requirements depending on your project goal – for example, if it requires material verification or further failure analysis.
- Brinell hardness test
- Rockwell hardness test
- Vickers hardness test
- Knoop hardness test
- Hot hardness test
- Shore hardness test
- Barcol hardness test
- VST hardness tests
We are able to offer both macrohardness testing (applied to loads of more than 1 kg) and microhardness testing (typically used for smaller or thinner samples and applied to loads of less than 1 kg) in accordance with a wide range of industry standards.
Why choose Element?
You can rely on Element’s breadth, range, and experience of Element’s hardness testing offerings. We can support you whether you require micro or macro hardness testing, on-site or in one of our cutting-edge laboratories, using destructive or non-destructive methods. Our team is truly global, operating from labs in more than 14 locations so you can benefit from our worldwide network and Element’s position as an established Testing, Inspection, and Certification market leader. Learn more about our credentials or, to discuss your hardness test requirements, contact us today.
Brinell Hardness Test vs Rockwell
Element expert Lee Mangham discusses the difference between Rockwell & Brinell hardness tests, the accuracy, and the advantages of each. Learn more
READ MOREWhat is Destructive Testing?
Destructive testing, also known as mechanical testing, subjects a material to different loads and stresses to evaluate its strength and durability. Read the article to learn about the different methods used for destructive testing.
READ MOREMore from Element

Metallurgical Testing
Find out about Element's range of metallurgical testing services, including microscopy, corrosion evaluation, hardness and on-site services.
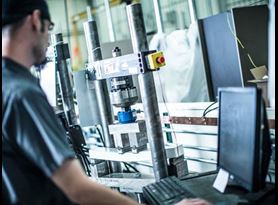
Fatigue Testing
Find out how Element's fatigue testing labs help companies meet quality requirements and create safer, stronger, more successful parts and products.
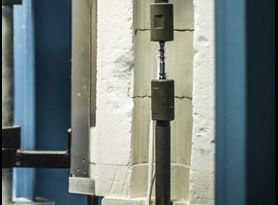
Stress Rupture and Creep Testing
Creep testing is critical to understanding and preventing product failures. Element performs both stress rupture and creep testing for metals, composites, and plastics to determine the long-term stress on materials.
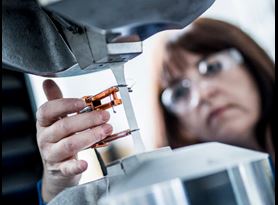
Tensile Testing Services
Element’s tensile testing labs provide conditions for exposing materials to a static or slowly applied force, determining their ultimate tensile strength. We perform industry-leading tensile tests for virtually any metallic or non-metallic material.