From benign hydrocarbons to sour fluids, polymer chemical resistance testing ensures that polymer-liquid interactions don’t result in catastrophic failures or malfunctions. We test a wide spectrum of properties that could be affected by fluid interactions, including mechanical strength, chemical deterioration and material swelling.
Our chemical resistance testing services help determine whether a polymer-fluid combination will remain functional throughout its service life, or if there are issues that need to be addressed before putting a system into service. Our experts work with you to design a test program that includes all possible variables, including sweet and sour fluid exposure, HPHT environments, thermally accelerated degradation and coating assessment.
Our Polymer Chemical Resistance Test Services
We understand the importance of testing against chemically hostile fluids to the success of your project. Element's Engaged Experts have considerable experience in reviewing polymer chemical resistance for oilfield applications. We work with you to reduce test requirements by eliminating specific fluids and materials where compatibility is known or strongly suspected and indicate likely performance of remaining polymer-fluid permutations, helping you complete your project on time and within budget.
For more information about our polymer chemical resistance services, or to request a quote, contact us today.
Ready to request a quote?
Our deliverable is certainty - high quality data, test reports and certificates that you can absolutely rely on when making decisions about your materials and compliance. Engage with an expert today.
Our Materials Testing Services
Related Services
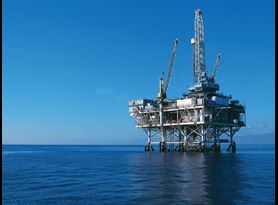
Oil & Gas
Element's global platform of laboratories offers advanced services designed to test and qualify materials intended for use within the environments of the future.
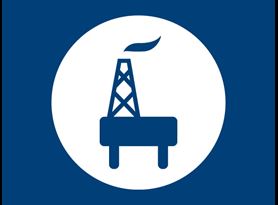
Element Adds Offshore pipeline testing Capability
Element offers cyclic straining and aging testing services
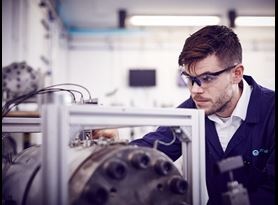
Liquid and Gas Permeation Testing for Polymers
Our unique range of permeation testing services determine the permeation coefficient (permeability), diffusion coefficient (diffusivity) and solubility coefficients.
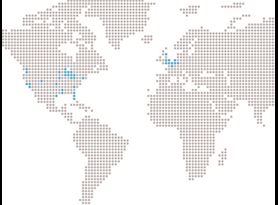
Element Locations
Learn more about our laboratories - where they are located; the unique capabilities they have and how they can help you solve your technical and commercial challenges.