Element’s polymer testing labs offer world-class expertise in testing for polymeric materials, including elastomers, thermoplastics, composites, coatings, and structural adhesives in a variety of industries.
Element’s network of cutting-edge polymer testing labs provide insight on how plastics and other polymeric materials will perform under mechanical and environmental stresses. Our expert staff and advanced laboratory technology allow us to perform a truly comprehensive range of tests, including compositional and chemical analysis, thermal analysis, permeation testing, and mechanical testing of polymers.
Trust an Element polymer testing lab to help you understand the limits of your materials and get the most value throughout their life cycle. For a full list of the standards and methods we utilize, or to learn more about custom testing, please contact us.
Mechanical Testing of Polymers
Polymer mechanical testing subjects the test specimen to different degrees and types of mechanical stress to understand how it will perform under extreme conditions. Element’s capabilities for mechanical testing include, but are not limited to:
- Hardness testing for polymers and composites
- Polymer tensile testing (strength)
- Polymer compression, impact, creep and fatigue testing
- Yield, adhesive and peel strength
Chemical & Compositional Polymer Testing
Element’s labs can also provide detailed information on the chemical makeup of a polymeric material, which gives insight on its quality, determines its compatibility with other materials and identifies any impurities or contaminants.
Our labs can identify the components of an unknown polymeric material in great detail using expert chemical and thermal analysis techniques. Chemical polymer testing may be necessary for material verification, failure analysis, or deformulation.
To learn more about Element’s polymer testing capabilities, or request a quote, contact us today.
Our services
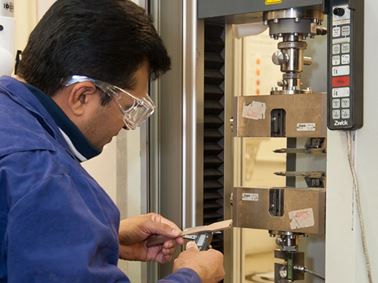
Mechanical Testing Services for Polymers
Element offers comprehensive mechanical testing services for polymers, elastomers, composites and thermoplastics, including fatigue, impact, creep, tensile, compression, bending and shear.
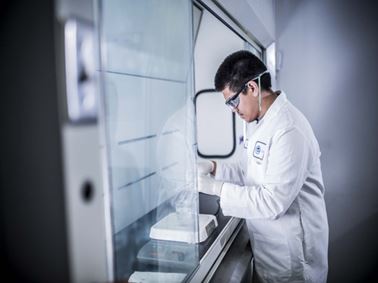
Compatibility Testing
Our compatibility testing services evaluate whether a fluid-polymer solution can sustain operation functionality, or if there are potential issues that could result in system failures.
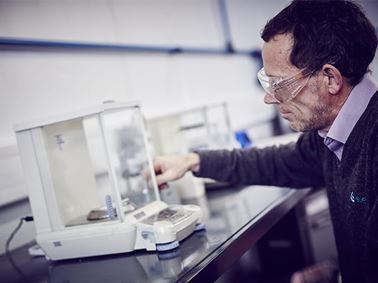
Analytical Testing
Element provides a range of analytical testing services for polymers, such as glass transition temperature, melting point, crystallinity, specific heat, thremal conductivity, weight loss, and dimensional and modulus changes.
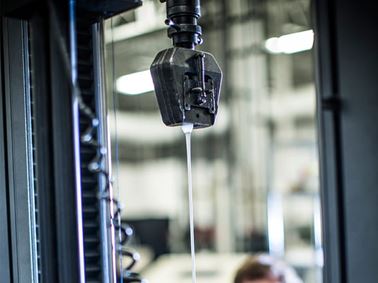
Polymer Failure Analysis
Element experts are here to help you with your failure analysis on plastics, composites, rubbers, adhesives, sealants, paints and coatings.
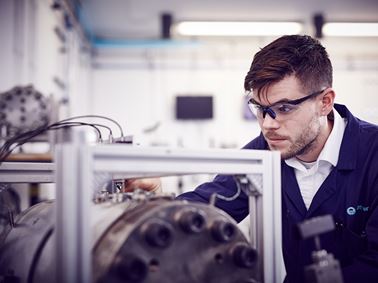
Permeation & Diffusion Testing
With a unique range of permeating capabilities for polymers, thermoplastics, elastomers and composites, we can simulate the high pressure and extreme temperatures found in deep wells, or the conditions in an automotive applications, utilities industry or chemical processing equipment.
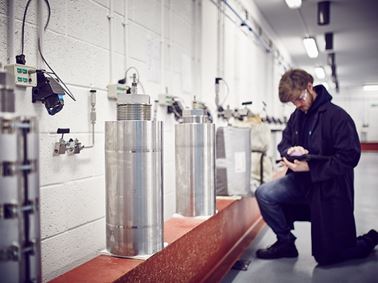
High Pressure High Temperature (HPHT) Exposure Testing Services
We offer extensive services for the qualification and compatibility of polymer materials exposed to production fluids at high pressure and high temperature (HPHT).
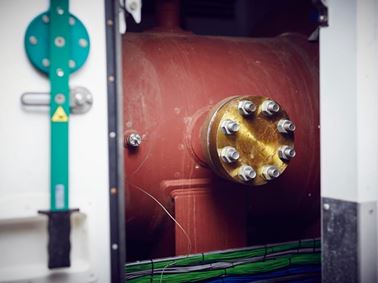
Thermal Insulation Coatings
Our industry-leading coating expertise covers a wide range of applications and client needs. Using state-of-the-art equipment and techniques, we provide consulting, investigation and testing of thermal insulation coatings.
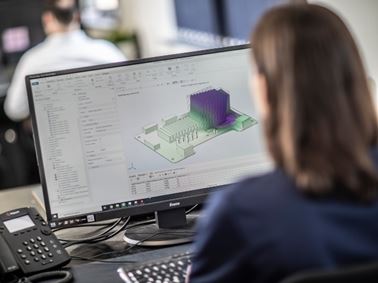
Finite Element Analysis Services (FEA)
Element offers advanced numerical analysis service using Finite Element Analysis (FEA) techniques using industry standard software to predict the long term behavior of materials components and products when in service.
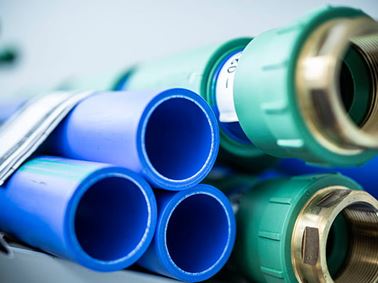
Plastic Pipes & Fittings Testing
Our plastic pipe testing program offers test data for product classification and lifetime evaluation to resin manufacturers, pipe extruders and certification bodies worldwide.
Our Materials Testing Services
Related Services
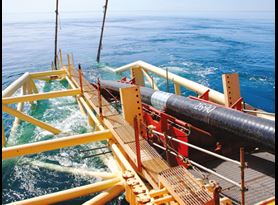
Coatings Testing
Find out about Elements range of coatings testing services designed to help to make certain that materials, products and pipelines we test for our customers are protected from corrosion, ultraviolet light, water penetration, heat, abrasion and chemicals.
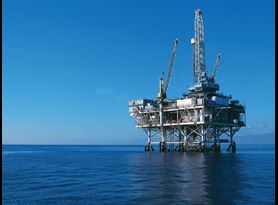
Oil & Gas
Element's global platform of laboratories offers advanced services designed to test and qualify materials intended for use within the environments of the future.
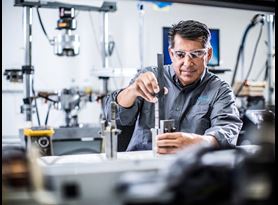
Polymer Matrix Composite Testing in Aerospace
Polymer Matrix Composites (PMCs) are helping push the limits of aerospace technology with lighter, stronger, more durable materials.
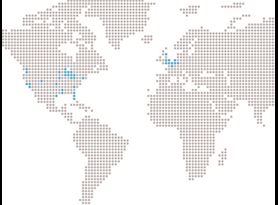
Element Locations
Learn more about our laboratories - where they are located; the unique capabilities they have and how they can help you solve your technical and commercial challenges.