With knowledge spanning all major industries, the experts at Element’s dynamics testing labs provide reliable, consistent data to ensure that your products are fit for purpose.
The long-term performance and reliability of your products – from construction materials to microelectronics – often depends on comprehensive dynamics testing.
Our testing laboratories have the capability to perform validation tests on a wide variety of components and systems, subjecting them to extreme stressors such as vibration, high temperatures, and mechanical shock and providing detailed performance data.
In addition to test execution, we also offer full-service fixture design and fabrication solutions.
Dynamics testing methods
Our dynamics testing methods focus on evaluating components in high-stress, high-performance environments. Combining multiple test methods, we create a single, comprehensive program that ensures product safety while saving you time and money.
Element’s experts work with you to design the ideal test regime for your components and products in every stage of your component lifecycle.
Vibration and mechanical testing
Element’s full-service testing laboratories have made us the testing partner of choice for hundreds of major OEMs and suppliers.
Our dynamics testing laboratories provide consistent and reliable vibration and mechanical shock testing for major industry sectors including automotive, military, aerospace, heavy truck, medical, industrial, and electronics. Our capabilities include:
- Vibration testing
- Combined temperature/humidity mechanical shock
- Mechanical shock at ambient conditions
- Fixture design and manufacturing
The Element advantage
Element’s long history of experience serving global manufacturers has allowed us to develop into the premier full-service testing organization.
In addition to dynamics testing, Element is one of very few test laboratories capable of providing full range product validation support from concept and design to post-test material analytics.
We provide hands-on support to meet the demanding timing needs of competitive markets. Program management is a critical component of our offerings, and we never shy away from tight schedules or strict timetables.
For more information about our structural dynamics testing services, contact an expert today.
Related Services
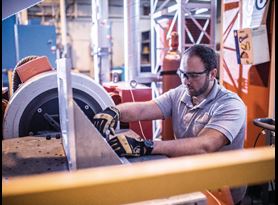
Vibration Test Fixture Design
Vibration fixture design is crucial to the development of an accurate vibration testing program. Element employs standard vibration table fixtures and can design and build custom fixtures.
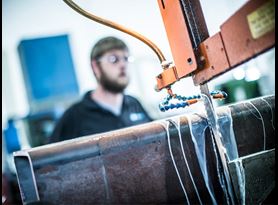
Manufacturing and Fabrication
Element’s fabrication services support your prototyping and product testing needs with custom-manufactured fixtures, tools, attachments, transfer carts, and more.
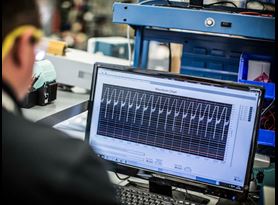
Vehicle Dynamics Testing
Element is at the forefront of vehicle dynamics testing, providing critical testing services to clients across a wide range of global sectors.

Shock Testing
Shock testing is used to measure the impact of sudden acceleration caused by explosion, drop, or collision. Element experts perform shock testing to prepare products for harsh industrial, transportation and military environments.